Installation, Install boiler trim, Install water piping – Fulton Vantage (VTG) Fully Condensing Hydronic Boiler User Manual
Page 12
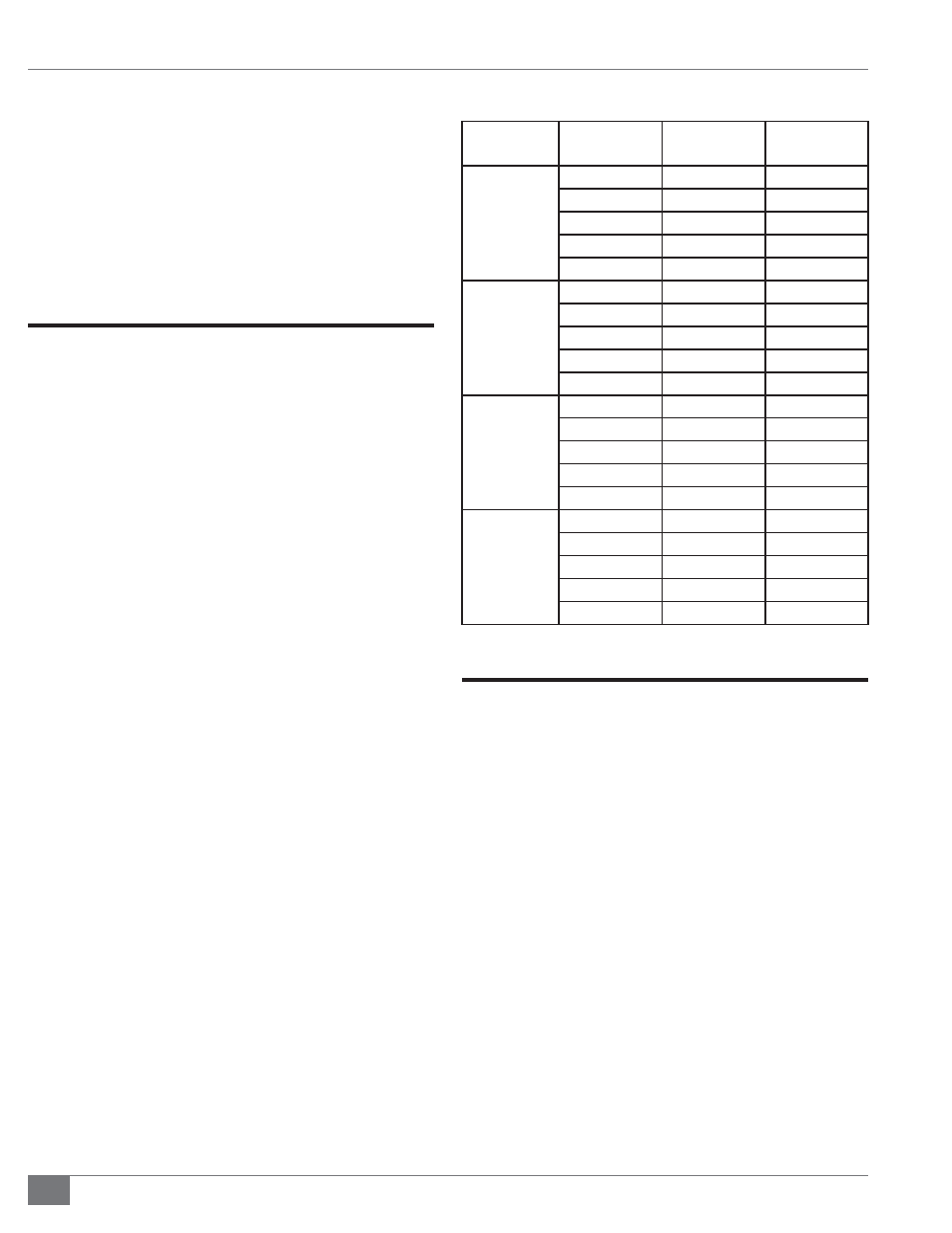
© The Fulton Companies 2013
INSTALLATION
VTG-IOM-2013-0815
SECTION 2
2-6
work environment. An 1 inch (25.4 mm) side clearance
is acceptable between boilers. Custom confi gurations
may not allow 1 inch (25.4 mm) side clearance.
3. Ensure all labels on the boiler will be fully visible for
maintenance and inspection.
4. Do not place any boiler room accessories, or other
components, on the Vantage skid.
Install Boiler Trim
Each Vantage boiler is supplied with a safety relief valve
sized in accordance with ASME requirements. Adhere to the
following installation requirements:
1. The safety relief valve (Figure 2) must:
» Be connected to the coupling located in the
top of the boiler.
» Be installed in the vertical position.
NOTE:
Safety relief valve size is determined by trim
pressure and is supplied in the trim kit along with
appropriate bushing, inlet and outlet sizes. See Table 2.
2. The discharge pipe must:
» Not have a diameter less than the full area of
the valve outlet.
» Be as short and straight as possible and so
arranged as to avoid undue stress on the valve.
» Be supported by means other than the safety
valve itself.
» Be piped to avoid danger of scalding
personnel.
NOTE:
Each boiler is equipped with a pressure-
temperature gauge to be installed in the outlet piping
section of the boiler. Gauge must not be isolated from
the boiler by any valve.
TABLE 2 - SAFETY RELIEF VALVE INLET AND OUTLET SIZES
Model
Trim Pressure
PSI (kPa)
Inlet Size
inch (mm)
Outlet Size
inch (mm)
VTG-2000,
2500
(DF, LE)
30 (206.84)
1 1/4 (31.75)
1 1/2 (38.1)
60 (413.69)
1 (25.4)
1 1/4 (31.75)
100 (689.48)
3/4 (19.05)
1 (25.4)
125 (861.84)
3/4 (19.05)
1 (25.4)
160 (1103.16)
3/4 (19.05)
1 (25.4)
VTG-3000,
3500
(DF, LE)
30 (206.84)
1 1/2 (38.1)
2 (50.8)
60 (413.69)
1 1/4 (31.75)
1 1/2 (38.1)
100 (689.48)
1 (25.4)
1 1/4 (31.75)
125 (861.84)
1 (25.4)
1 1/4 (31.75)
160 (1103.16)
3/4 (19.05)
1 (25.4)
VTG-4000,
5000
(DF, LE)
30 (206.84)
2 (50.8)
2 1/2 (63.5)
60 (413.69)
1 1/2 (38.1)
2 (50.8)
100 (689.48)
1 1/4 (31.75)
1 1/2 (38.1)
125 (861.84)
1 (25.4)
1 1/4 (31.75)
160 (1103.16)
1 (25.4)
1 1/4 (31.75)
VTG-6000
(DF)
30 (206.84)
2 (50.8)
2 1/2 (63.5)
60 (413.69)
1 1/2 (38.1)
2 (50.8)
100 (689.48)
1 1/4 (31.75)
1 1/2 (38.1)
125 (861.84)
1 1/4 (31.75)
1 1/2 (38.1)
160 (1103.16)
1 (25.4)
1 1/4 (31.75)
Install Water Piping
All water supplies contain some solids, dissolved gases or
dissolved minerals. These may cause corrosion, deposition
and/or fouling of equipment. To prevent these contaminants
from impacting boiler performance, valve operation and
general pipe longevity, each location must be analyzed and
treated accordingly.
Adhere to the following for water piping installation (See
Figure 3):
1. Isolation valves are recommended on both water
connections for ease of service.
2. Install piping so that the boiler is not supporting any
additional piping.
3. Install manual purging valves in all loops and zones.
Install a pressure-reducing (automatic fi ll) valve in the
cold water fi ll line to the boiler system. Check that the
proposed operation of zone valves, zone circulator(s)
and diverting valves will not isolate air separator(s) and/
or expansion tank(s) from the boiler. Clearance from hot
water pipes to combustibles must be at least 6 inches
(152 mm).