Meter start up and operation, Warning – Liquid Controls M-MA Meters User Manual
Page 9
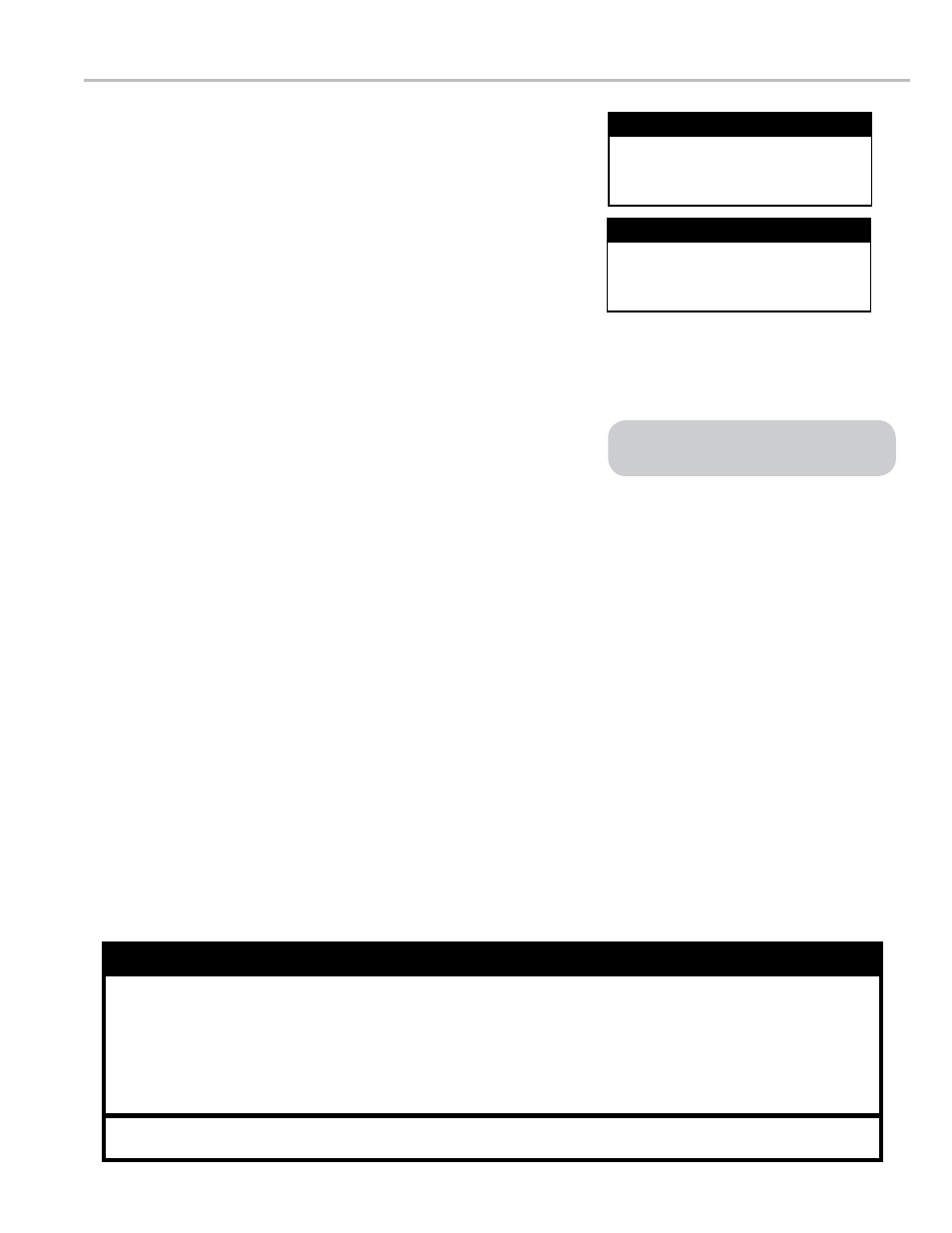
prior to meter start up, use extreme caution. Make sure that:
1. The meter is properly secured
2. All connections are tight
3. All valves are in the closed position
placInG your Meter In operatIon
When placing your meter in operation, the meter and system must be
filled slowly with liquid and be free of air prior to start-up. Extreme care
must be taken to avoid damaging the meter during this time. When filling
the system with liquid for the first time, gravity filling is the preferred
method of filling the system with liquid. Gravity filling uses positive head
pressure from product storage above the inlet port of the meter to fill the system. If necessary, systems can be filled
with the pump.
to fill the meter and system with liquid:
1. Make sure all valves (upstream and downstream of the meter) in the system
are closed.
2. Open the valve located at the storage tank a small amount. Provided there is
not a valve between the tank and the meter inlet, the meter’s register/counter
will start to move and then stop. If there is another valve between the tank and meter, repeat this process with each valve until
the meter is exposed to the liquid.
3. Once you are assured that the meter has registered some volume and stopped, continue to open the tank valve until it is
completely open.
4. With the valve(s) open between the tank and the meter, slowly open the downstream valve until the meter’s register/counter
starts to move. Do not run the meter any faster than 25% of its rated flow during start-up. Once the product is flowing out of the
end of your system, the outlet valve can be opened all the way, provided that the system is designed not to exceed the flow
rate marked on the meter.
Meter start up and operatIon
Make sure that your pump can operate
against a dead head pressure. If not,
consult the factory for assistance.
Dead Head Pressure - Pumps
Prime the pump before using it to fill the
system. Consult the pump manufacturer
for proper pump priming.
Prime the Pump First
Before disassembly of any meter or accessory component:
• all internal pressures must be relieved and all liquid drained from the system in
accordance with all applicable procedures.
• pressure must be 0 (zero) psi.
• close all liquid and vapor lines between the meter and liquid source.
For Safety Rules, refer to local authorities and relevant NFPA Codes.
failure to follow this warning could result in property damage, personal injury, or death from
fire and/or explosion, or other hazards that may be associated with this type of equipment.
!
WarnInG
If the valves are not manual, consult the
valve manufacturer for slow flow start-up.
▪ never operate the Meter or systeM
When partIally fIlled WIth lIquId, or
WIth pockets of coMpressed aIr or
vapor present.
If these conditions cannot be avoided, air and vapor elimination
systems may be required. If you cannot fill the meter slowly by
gravity or by using a valve to throttle back the flow, consult the
factory.
▪ do not operate the Meter above the
MaxIMuM pressure lIsted on the serIal
nuMber plate.
Under any and all pressure producing circumstances (for instance,
thermal expansion and hydraulic shock) the working pressure
must not exceed the maximum pressure indicated on the Serial
Number Plate.
▪ do not operate the Meter above the
MaxIMuM floWrate lIsted on the serIal
nuMber plate
If the meter is operated at a rate greater than the maximum
recommended GPM, excessive wear and premature failure may
occur.
▪ the Meter can be calIbrated for floWs
beloW MInIMuM ratInGs
If the flow remains constant and varies within narrow limits or if
the product is viscous, the meter can be calibrated for flows below
minimum ratings. If the meter is installed in a custody transfer
application (for financial transactions), the flow rate must fall within
flow rate range indicated on the serial number plate. A meter
should never be run beyond the maximum flow rate determined for
that class meter and/or liquid measured.
9