Controlled Products Systems Group RANGER User Manual
Page 28
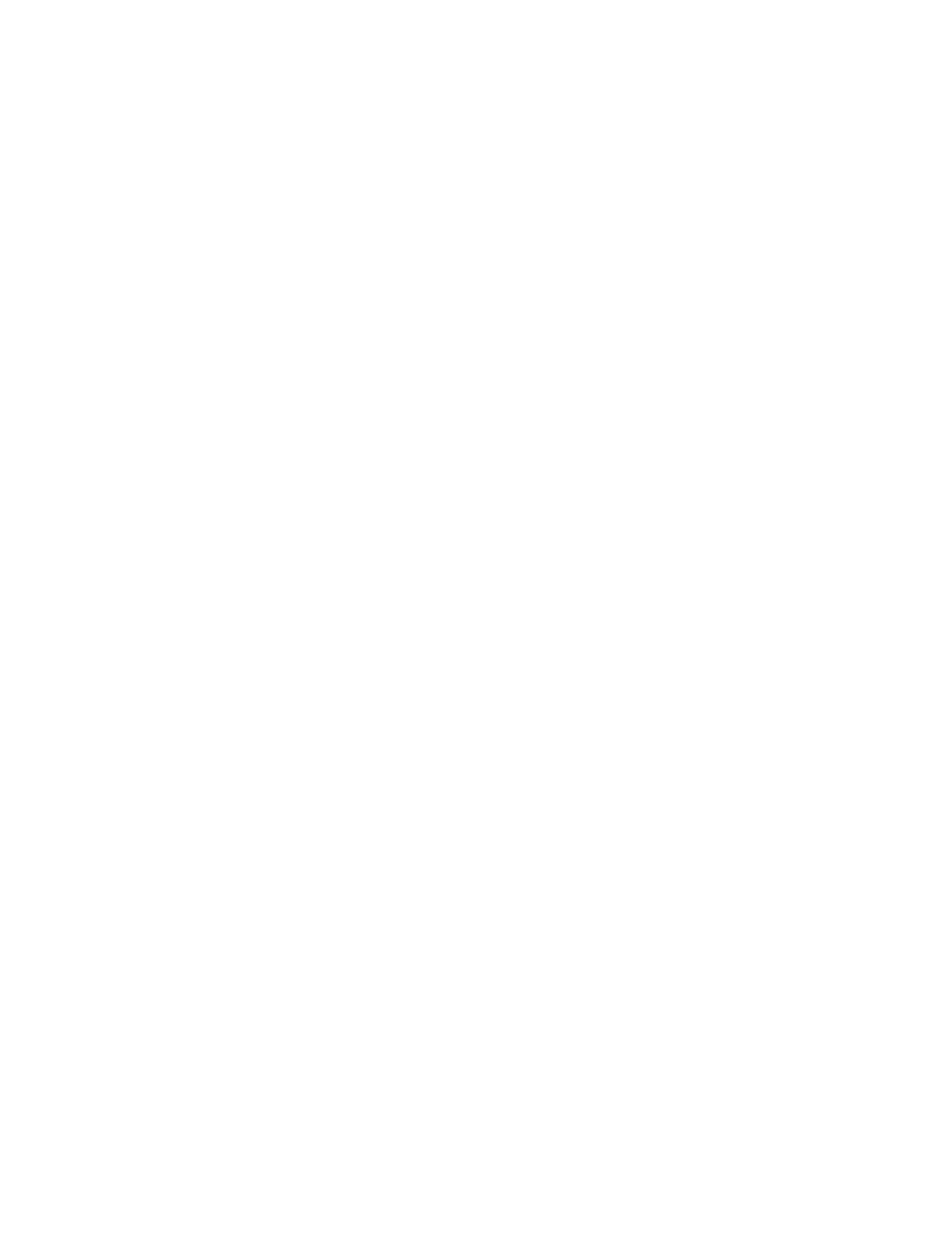
26
1.
My single gate will not operate: (connected to Gate I or Gate II)
STEP 1 Open control box cover and locate the “Open/Close Command” push button and press it to operate the gate.
STEP 2 Press the “Reset” push button located above the open close command, then push the “open/close command” push
button to operate the gate.
STEP 3 When pressing the “open/close command” push button, listen for a clicking sound, if click is heard then verify:
A. Verify the correct control switch is “ON” corresponding to the Gate 1 or Gate 2 connector the linear actuator is
connected to.
B. If step A above check good, then press the “Open/Close Command” push button on the control board. If a clicking
sound is heard coming from the control board then the problem is most likely low power.
C. Low power can be caused by two things – Low battery voltage or a bad connection at the battery. Battery will need to
be load tested to verify it is good. Replace battery or correct connection problem at battery.
STEP 4 Remove the receiver connector that is plugged into the J1 connector. Press the “Open/Close Command” button
and verify gate operates.
STEP 5 Disconnect linear actuator connector from the control board and connect it to the other (Gate 1 or Gate 2)
connector on
the control board. Then set the corresponding control switch to the “ON” position. Press the
“Open/Close Command”
button and verify gate operates. If gate operates on the other connector that is
acceptable.
STEP 6 If gate still does not operate please call USAutomatic for more information.
2.
Gate 1 or Gate 2 will not operate. Dual gate Installation
STEP 1 These instructions are for the failure of one gate to operate in a dual gate installation.
STEP 2 Identify the gate that will not work and check the control switch for that gate and verify that it is turned “ON”.
STEP 3 Swap the Gate 1 and Gate 2 linear actuator connectors on the control board. If problem moves to other gate then
the control board is bad.
STEP 4 If problem remains in the same gate then the problem is either a wire problem or linear actuator problem. Since it
is a possible wire problem we need to check the following:
A. Wire harness for cuts, nicks or bad splices if splice exist.
B. If gate with problem is the gate located on the other side of drive from control box (Gate 2) the cable under the drive
needs to be verified good. This is done by using a voltmeter and going to the junction box located below the Gate 2
linear actuator. Locate the red wire with white stripe and the black wire with white stripe and then operate the gate and
check voltage on these two wires (expect 12 VDC).
C. If voltage is present when gate should be operating then the problem is most likely the linear actuator.
D. If voltage is not present when gate should be operating then move back to the control box side and check voltage on
same two wires located in the wire compartment.
E. If voltage is present on the control box side of drive then the cable in the ground must be damaged.
F. If voltage is not present in the control box then we have missed something in steps 2 or 3, recheck.
3.
Gate 1 and Gate 2 will not operate. Dual gate installation
STEP 1 These instructions are for the failure of both gates to operate in a dual gate installation.
STEP 2 Verify that control switches 3 and 4 are turned “ON”.
STEP 3 Verify the red and black wires on the Quick Connect harness are connected to the battery correctly. Red connects
to positive and black connects to negative post on the battery.
STEP 4 Verify that the battery is charged, press the “Open/Close Command” push button, if a clicking sound is heard
from the control board then most likely the battery is dead. Have the battery load tested to verify it is bad.
STEP 5 If battery checks good (passed the load test) then the control board is most likely the problem. To think that 2
motors have gone bad would not make sense but is also a possibility.
4.
Gate 1 or Gate 2 (Gate 1 and Gate 2 if dual gate) operating speed has slowed down
NOTE: When the gate is running slow the reason is low power, two things need to be considered. Battery
condition (replace or charge) and the ¼” ring terminals located on the Quick Connect harness which are
connected to the battery. The ring terminals can become corroded and need replacing over time.
STEP 1 Determine which situation your operator falls into below: