General maintenance – Controlled Products Systems Group HTG 320-2 ST User Manual
Page 55
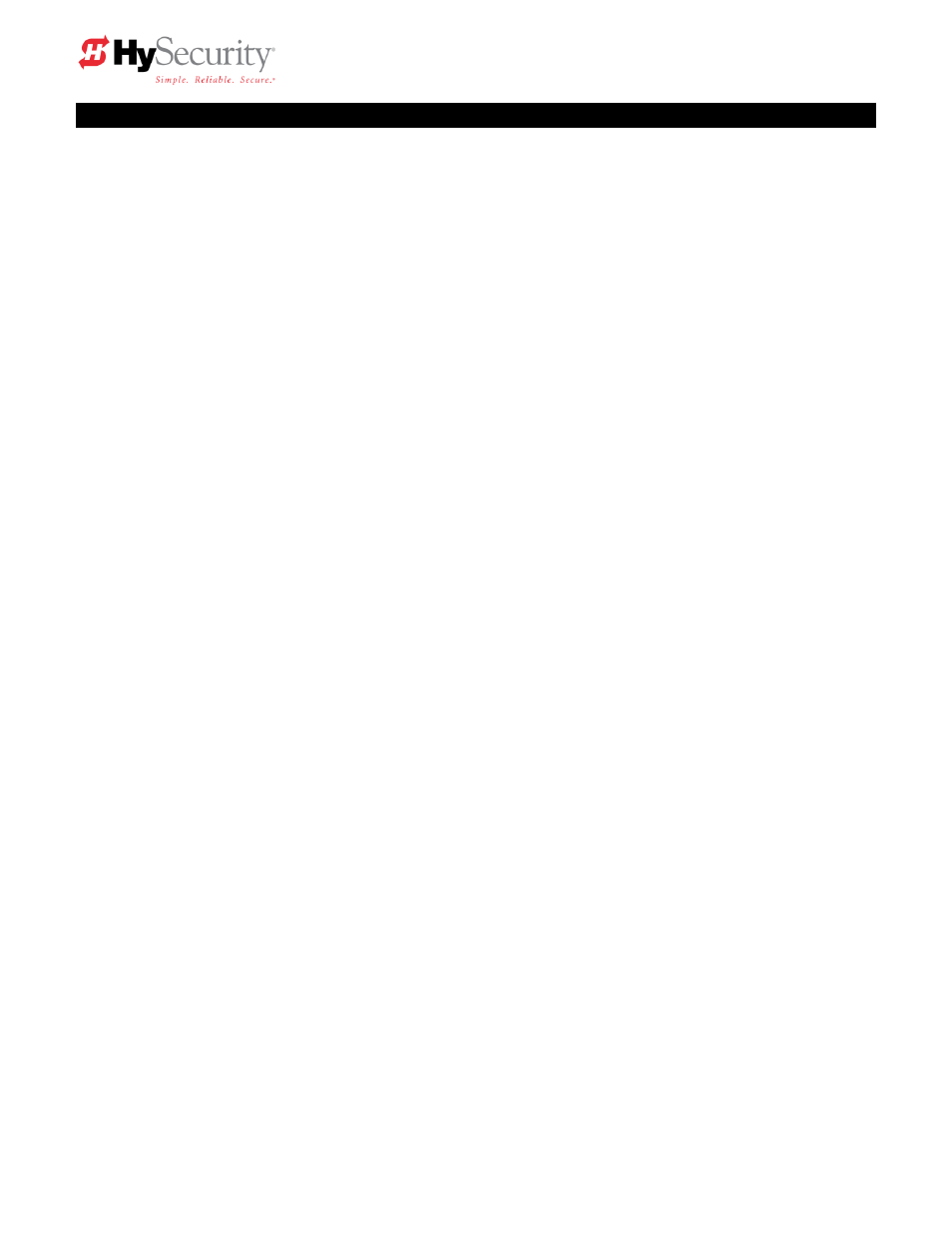
StrongArm Installation and Reference
45
General Maintenance
Hydraulic System
Fluid Level:
Under normal conditions, hydraulic systems do not consume oil. Before adding any oil,
check the system thoroughly for leaks. Remove the bright metal plug in the tank, fill to plug level, then
replace plug. We recommend our Uniflow hydraulic oil; part number H004 1.0, which is sold in one-gallon
containers by our distributors. Never use brake fluid. It will severely damage the entire hydraulic
system. Use of any oil other than Uniflow oil may void the operator warranty.
Look for leaks:
Occasionally there may be slight seeping at the fittings after some usage. Tightening of
the fittings will usually correct the problem. If the leaking persists, replace "O" rings, fittings or hoses, if
required. No further leaks should occur.
Oil Change:
A hydraulic system does not foul its oil, unlike a gas engine, so oil changes do not need to
be frequent. Oil breakdown caused by heat is the main concern. If the unit is subjected to high use,
especially in a warm climate, change the oil more frequently. In general, we recommend draining the
reservoir and replacing the oil at five-year intervals.
To change the hydraulic oil, remove the reservoir from the pump unit and completely, empty it and wipe
the reservoir clean and clean the derby screen before re-assembling. Refill with new Uniflow hydraulic
oil. Slowly pour the oil into the tank until the oil is within one inch of the filler port. Replace the plug and
wipe up any spilled oil. If any oil is allowed to remain, it will dry to a very sticky and messy consistency.
Mechanical Maintenance
Before servicing, turn off power disconnect switch
Depending upon duty cycles, use a grease gun to apply a lithium-based grease into the crank arm zerk
fitting on six month to one year intervals. The main shaft bearings should be greased annually.
Electrical Controls
Before servicing, turn off power disconnect switch
No routine maintenance is needed for the electrical system or controls. If the environment is very sandy
or dusty, or has many insects be certain to seal all holes in the electrical enclosure. Blow the dust out of
the electric panel with compressed air. A qualified technician may troubleshoot with the aid of the
troubleshooting guide in this appendix. If it is necessary to call a distributor for assistance, be sure to
have your model and serial number ready. Other helpful information would include the name of the job,
approximate date of installation, and the service record of the operator, especially any work that has
been done recently.
How to Adjust the Pressure Relief Valve: To check your relief valve setting, first loosen a limit switch
cam so that the operator will not shut off in one direction. Run the operator to either open or closed (the
gate will not move with the hose disconnected. The relief valve is found on the rear of the hydraulic
power unit. It has an adjusting head and lock nut. To adjust, loosen the lock nut and screw the threaded
bolt clockwise for increased pressure, counterclockwise to decrease pressure.
MODEL
FACTORY RELIEF SETTING
StrongArm (HTG 320-2)
700 PSI
StrongArm (HTG 320-3, -6, -8)
1000 PSI