Cashco 1000 HP Differential User Manual
Page 11
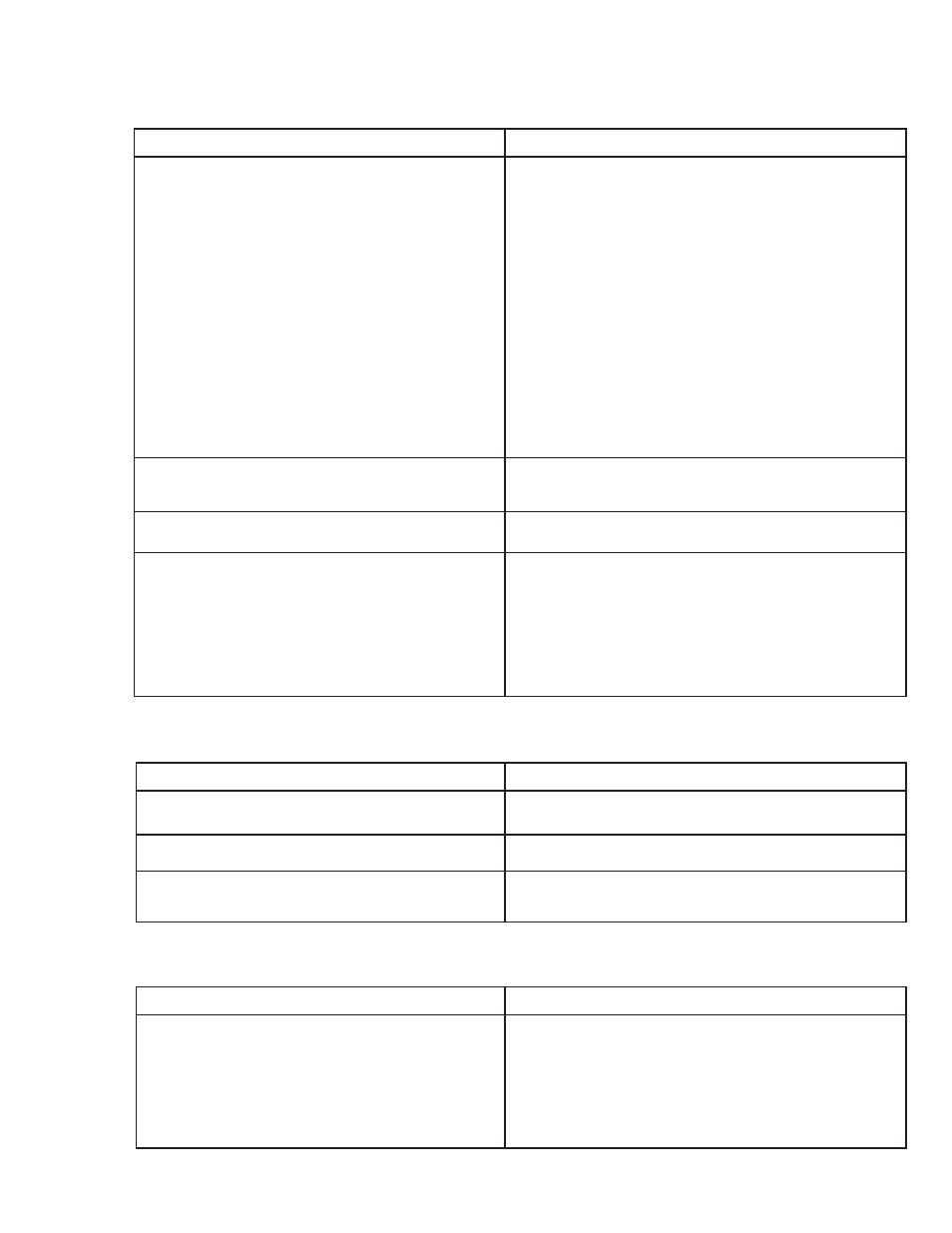
11
IOM-1000HP-Dif fer en tial
4. Excessive pressure downstream.
Possible
Causes
Remedies
A. Regulator not closing tightly.
A1. Overly compressed range spring; i.e. approaching
solid height. Use next higher range spring.
A2. Inspect the seating. Clean and lap metal seat
surfaces; replace if lapping does not remedy. If
composition seats are depressed, nicked or
embedded with debris, replace seat disk.
A3. Diaphragm setting too high; check setting.
A4. Inlet pressure too high for orifi ce size; check
permissible inlet (P
1
) pressure level for a given
outlet. Change to reduced port if required.
A5. Leakage past pressed in seat ring; consider
integral
seat.
A6. When diaphragm subassembly was put into place,
the rocker arm got between the stud collar and the
stud nut rather than on top of the stud collar.
B. Downstream block.
B. Check system; isolate (block) fl ow at regulator
inlet, not outlet. Relocate regulator if necessary.
C. No pressure relief protection.
C. Install safety relief valve, or rupture disc.
D. Restricted diaphragm movement.
D1. Diaphragm setting too high; check and lower
as
required.
D2. Ensure no moisture in spacer ring at temperatures
below freeze point. Ensure no dust or debris
entering vent opening. If rainwater or debris can
enter, reorient spring chamber. (Not possible on
-1+6.)
5.
Sluggish
operation.
Possible
Causes
Remedies
A. Plugged piston or jet zone.
A. Remove trim and clean.
B.
Fluid
too
viscous.
B. Heat
fl uid.
C. Improper (undersized) jet.
C. Replace existing piston with new piston for
viscous
service;
i.e.
Opt-27.
6. Frequent resetting of setpoint.
Possible
Causes
Remedies
A. Overpressurization downstream resulting in:
A1. Replace diaphragms. Correct potential source of
1. Bent metal diaphragm(s)
downstream overpressure.
2. Sprung rocker arm
A2. Check measurements of rocker arm. Replace if
3.
Range
spring
overstressed/fatigued.
necessary.
A3. Replace range spring; consider next higher range
spring.