Cashco DL User Manual
Models d and dl, Pressure reducing regulators, I. description and scope
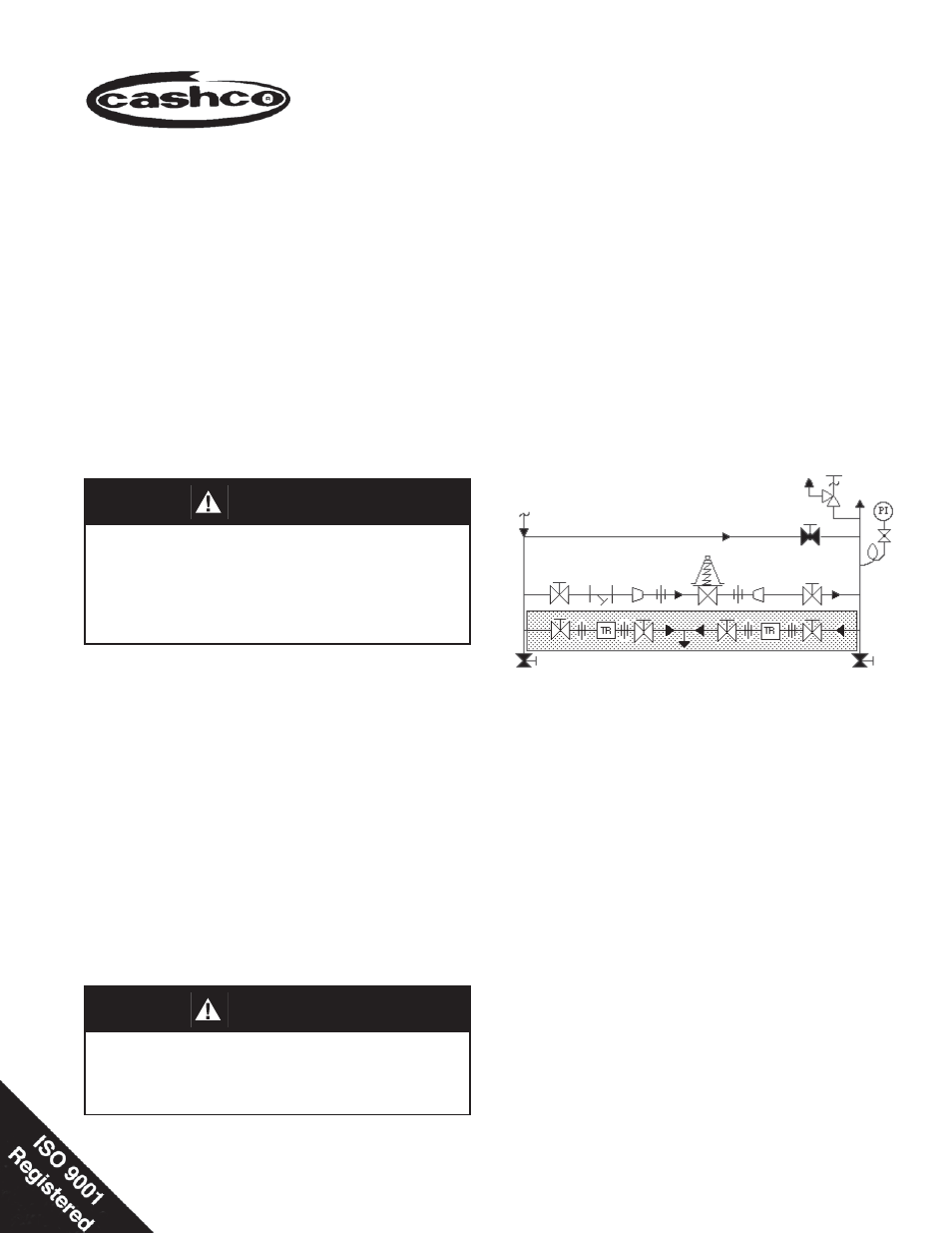
INSTALLATION, OPERATION & MAINTENANCE MANUAL (IOM)
IOM-D/DL
12-13
MODELS D and DL
PRESSURE REDUCING REGULATORS
SECTION I
I. DESCRIPTION AND SCOPE
The Model D is a pressure reducing regulator used to control downstream (outlet or P
2
) pressure. Sizes are 3/8" (DN10),
1/2" (DN15), 3/4" (DN20) and 1" (DN25). With proper trim utilization, the unit is suit able for liquid, gase ous, or steam
serv ice. Refer to Technical Bulletin D-TB for design conditions and se lec tion recommendations.
The Model DL is also a pressure reducing regulator similar to above Model D. Sizes are 1-1/2" (DN40) and 2" (DN50).
(Model DL was formerly a Cashco Model D). Refer to Technical Bulletin DL-TB for design conditions and selection recom-
mendations.
SECTION II
II. INSTALLATION
1. An inlet block valve should always be in stalled.
2. If service application is continuous such that shut-
down is not readily accomplished, it is rec ommended
that an inlet block valve, outlet block valve, and a
manual bypass valve be installed.
3. Pipe unions should be installed to allow re moval
from piping.
4. An outlet pressure gauge should be located ap prox i-
mate ly ten pipe diameters downstream and within
sight.
5. All installations should include a downstream re lief
device if the inlet pressure could exceed the pres-
sure rating of any downstream equip ment or the
maximum outlet pressure rating of the unit.
Recommended Piping Schematic
For Pressure Reducing Station
6. Clean the piping of all foreign material in clud ing
chips, welding scale, oil, grease and dirt be fore in-
stalling the regulator. Strainers are rec om mend ed.
7. In placing thread sealant on pipe ends prior to
en gage ment, ensure that excess material is re-
moved and not allowed to enter the regu la tor upon
startup.
8. Flow Direction: Install so the fl ow direction match es
the arrow cast on the body.
9. For best performance, install in well drained hori-
zon tal pipe, properly trapped, if a steam service
application.
10.A. Basic Regulator - (Refer to Figure 2): Regu la tor
may be rotated around the pipe axis 360
o
. Rec-
om mended position is with spring cham ber ver ti cal
upwards. Ori ent such that the spring cham ber vent
hole does not collect rainwater or debris.
CAUTION
For welded installations, all internal trim parts, seals
and diaphragm(s) must be removed from regula-
tor body prior to welding into pipelne. The heat
of fusion welding will damage non-metallic parts if
not removed. NOTE: This does not apply to units
equipped with extended pipe nipples.
CAUTION
Installation of adequate overpressure pro tec tion is
recommended to pro tect the reg u la tor from overpres-
sure and all down stream equip ment from damage
in the event of regulator failure.
Supply
@ P1
Outlet
@ P2
SRV
Model D or DL
Reducing
Regulator
Bypass
Blowdown-Drain
Blowdown-Drain
(Shaded portion for steam/condensate systems)