Fluid Components International VORTAB User Manual
Page 13
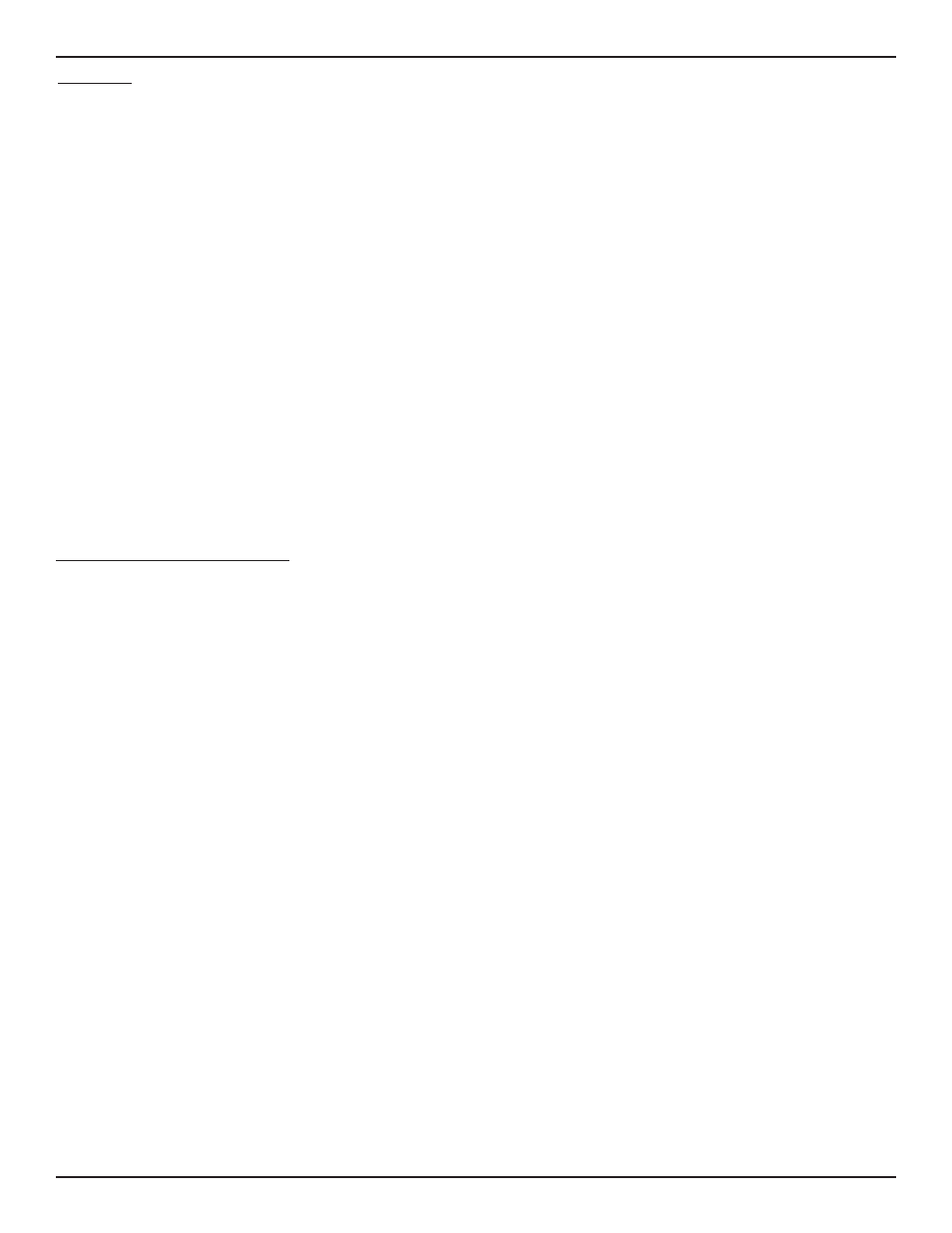
VORTAB Flow Conditioner
VORTAB
®
Company
Doc. No. 06EN003269 Rev. D
13
This page is subject to the proprietary rights statement on the last page
Maintenance
General
Without detailed knowledge of the environmental parameters of the application surroundings and process media, Vortab cannot make specific
recommendations for periodic inspection or cleaning procedures. However, some suggested general guidelines for maintenance steps are offered
below. Use operating experience to establish the frequency of each type of maintenance.
VIS, VMR, VSR VEL and VFK Maintenance
Periodically check the flow conditioner based on historical evidence of debris and foreign matter in the process pipe. The tapered design of Vortabs
make them self cleaning and inherently immune to fouling and clogging. The exception could be large items such as buckets, palm branches, hard
hats and other items that could become lodged if their size is larger than the through core diameter of the installed anti-swirl tabs. Due to the pres-
sure differential between the upstream and downstream sides of the profile conditioning tabs, a vacuum effect constantly pulls media and debris
from the backsides of the tabs.
Build up of sticky substances such as paraffin (wax) could cause decreased effectiveness of the flow conditioner. Clean the flow conditioner accord-
ing to process pipe cleaning schedules and procedures.
VIP Maintenance
Unlike the standard Vortab products, the Vortab Insertion Panel (model VIP) is not an open core flow conditioner and therefore, more likely suscep-
tible to clogging from debris and foreign matter, which can lead to flow meter anomalies. Build up of sticky substances such as wax (paraffin) can
also contribute to flow meter discrepancies. Periodic checks are recommended especially after start up of new installations or when a flow meter’s
readings are questionable. Always re-install the VIP in the orientation in which it was removed, as they are orientation sensitive. Refer to VIP instal-
lation guidelines covered in previous sections.
Customer Service and Technical Support
Vortab provides full in-house technical support for our products 7 a.m. to 5 p.m. PST, Monday through Friday (except holidays and an annual plant
closure between Christmas and New Year’s day). Also, additional technical representation is provided by Vortab field representatives.
By Mail
Vortab
1755 La Costa Meadows Dr.
San Marcos, CA 92078-5115 USA
Attn: Customer Service Department
By Phone
Contact the area Vortab regional representative. If a field representative is unable to be contacted or if a situation is unable to be
resolved, contact the Vortab Customer Service Department toll free at 1 (800) 854-9959 or 1 (760) 736-6114.
By Fax
To describe problems in a graphical or pictorial manner, send a fax including a phone or fax n@umber to the regional representative.
Again, Vortab is available by facsimile if all possibilities have been exhausted with the authorized factory representative. Our Fax
number is 1 (760) 736-6250; it is available 7 days a week, 24 hours a day.
By E-Mail
Vortab Customer Service can be contacted by e-mail at: [email protected]. or [email protected].
Describe the problem in detail making sure a telephone number and best time to be contacted is stated in the e-mail.
International Support
For product information or product support outside the contiguous United States, Alaska, or Hawaii, contact your country’s Vortab
International Representative or the one nearest to you.