Vortab field kit (vfk) installation – Fluid Components International VORTAB User Manual
Page 12
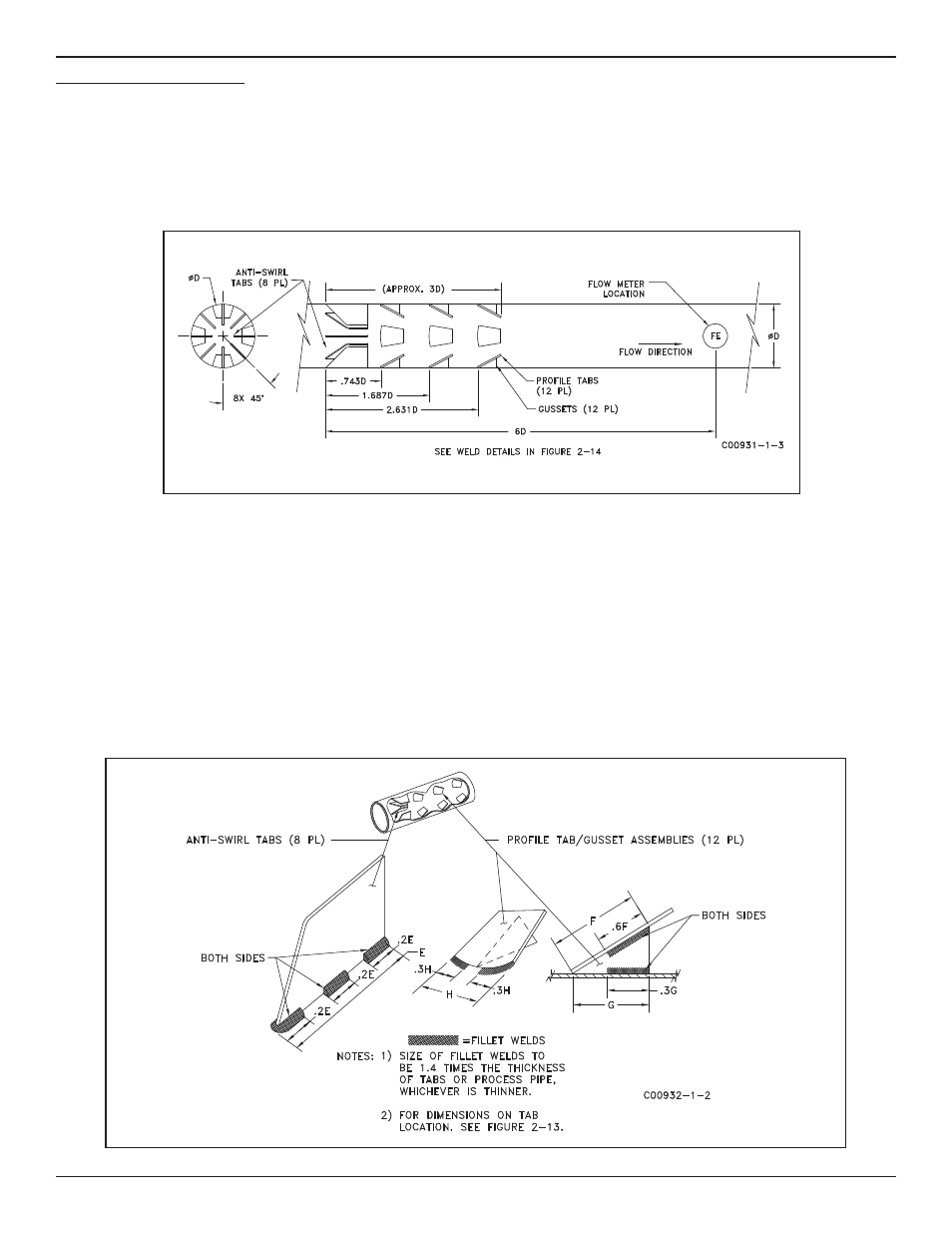
VORTAB
®
Company
VORTAB Flow Conditioner
This page is subject to the proprietary rights statement on the last page
12
Doc. No. 06EN003269 Rev. D
Vortab Field Kit (VFK) Installation
Process Pipe Preparation
The length of the flow conditioning section is three pipe diameters (3D). The inlet consists of eight symmetrically arranged anti-swirl tabs followed
by three sets of four symmetrically arranged profile tab/gusset assemblies. See Figure 2-13. Flow meters to be installed three pipe diameters (3D)
downstream from the exit of the flow conditioning section. The flow meter’s downstream requirements should adhere to the flow meter manufac-
turer’s installation recommendations. Orientation of the tabs is not critical although symmetry with the downstream flow metering device is recom-
mended. Position the Vortab flow conditioning internals and respective flow meter per recommendations shown in Figure 2-13.
Figure 2-13. Tab Location
Weld Procedures
The easiest way to install the VFK is to have access to the VFK assembly location from both ends for welding. However, if only one end is accessible,
then start with the tabs the farthest from the access end. This could either be the anti-swirl tabs located at the flow conditioning inlet or it will be
the last set of downstream profile tab/gusset assemblies.
Welding surfaces should be free of moisture and contaminants.
It is highly recommended to mark the tab locations and then spray the inside of the process pipe with anti-spatter prior to any welding.
Before welding into process pipe, fabricate the profile tab/gusset assemblies by welding the twelve profile tabs to their respective gussets. Refer to
Figure 2-14.
Weld Vortab flow conditioning internals into process pipe. Thoroughly clean all weld spatter and slag from process pipe. Sandblast if possible.
Figure 2-14. Weld Detail