8 installation – Burkert Type 2105 User Manual
Page 10
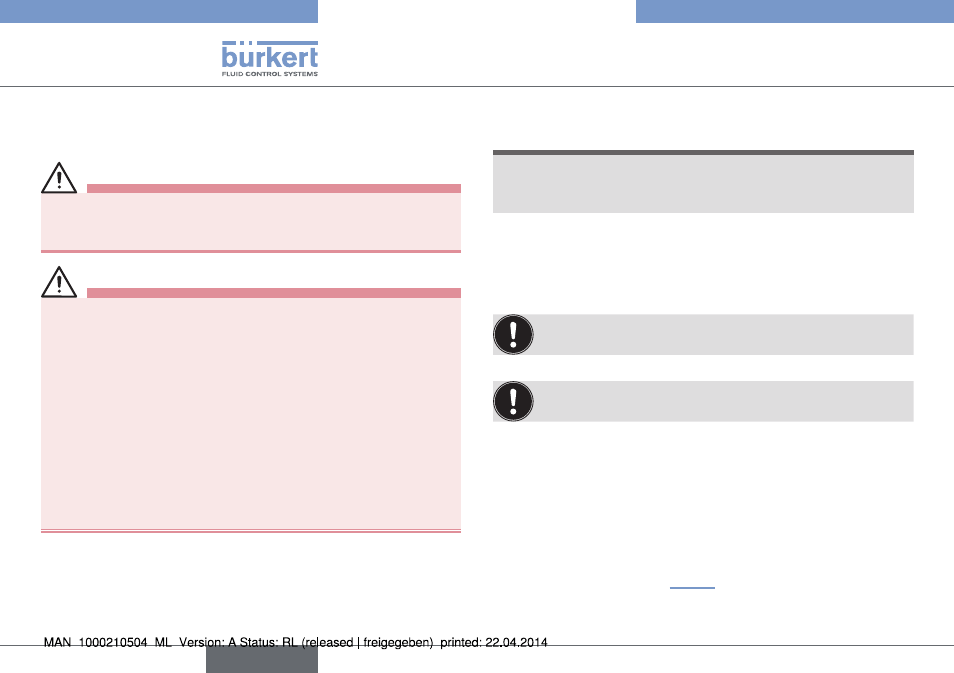
10
Installation
8
insTallaTion
8.1 safety instructions
Danger!
risk of injury from high pressure in the equipment/product!
▶ Before working on equipment or product, switch off the pressure
and vent the lines.
Warning!
risk of injury from improper installation!
▶ Installation may be carried out by authorised technicians only
and with the appropriate tools!
risk of injury from unintentional activation of the system and
an uncontrolled restart!
▶ Secure system from unintentional activation.
▶ Following assembly, ensure a controlled restart.
for control function I – danger if pilot pressure fails!
For control function I control and resetting occur pneumatically. If
the pressure fails, no defined position is reached.
▶ To ensure a controlled restart, first pressurize the product with
pilot pressure, then switch on the medium.
8.2 Before installation
note!
damage to the diaphragm or the actuator!
▶ Products with VG/VS welded body: Before welding in the body,
remove the actuator.
• Before connecting the valve, ensure the pipelines are flush.
• The flow direction is optional.
8.2.1
installation position general
Installation for self-drainage of the body
It is the responsibility of the installer and operator to ensure
self-drainage.
Installation for leakage detection
One of the bores (in the actuator base) for monitoring
leakage must be at the lowest point.
8.2.2
installation position type 2103
• The piston-controlled diaphragm valve can be installed in any
installation position, preferably with the actuator face up.
To ensure self-drainage:
→
Install body inclined by an angle α = 10° – 40° to the horizontal.
→
Observe an inclination angle of 1° – 5° to the line axis.
Forged and cast body: Mark on the body must point upwards
(12 o’clock position, see “Fig. 6”).
→
One of the bores (in the actuator base) for monitoring leakage
must be at the lowest point.
english
Type 2103, 2104, 2105