Brooks, Model 5851 i – Brooks Instrument 5851i User Manual
Page 39
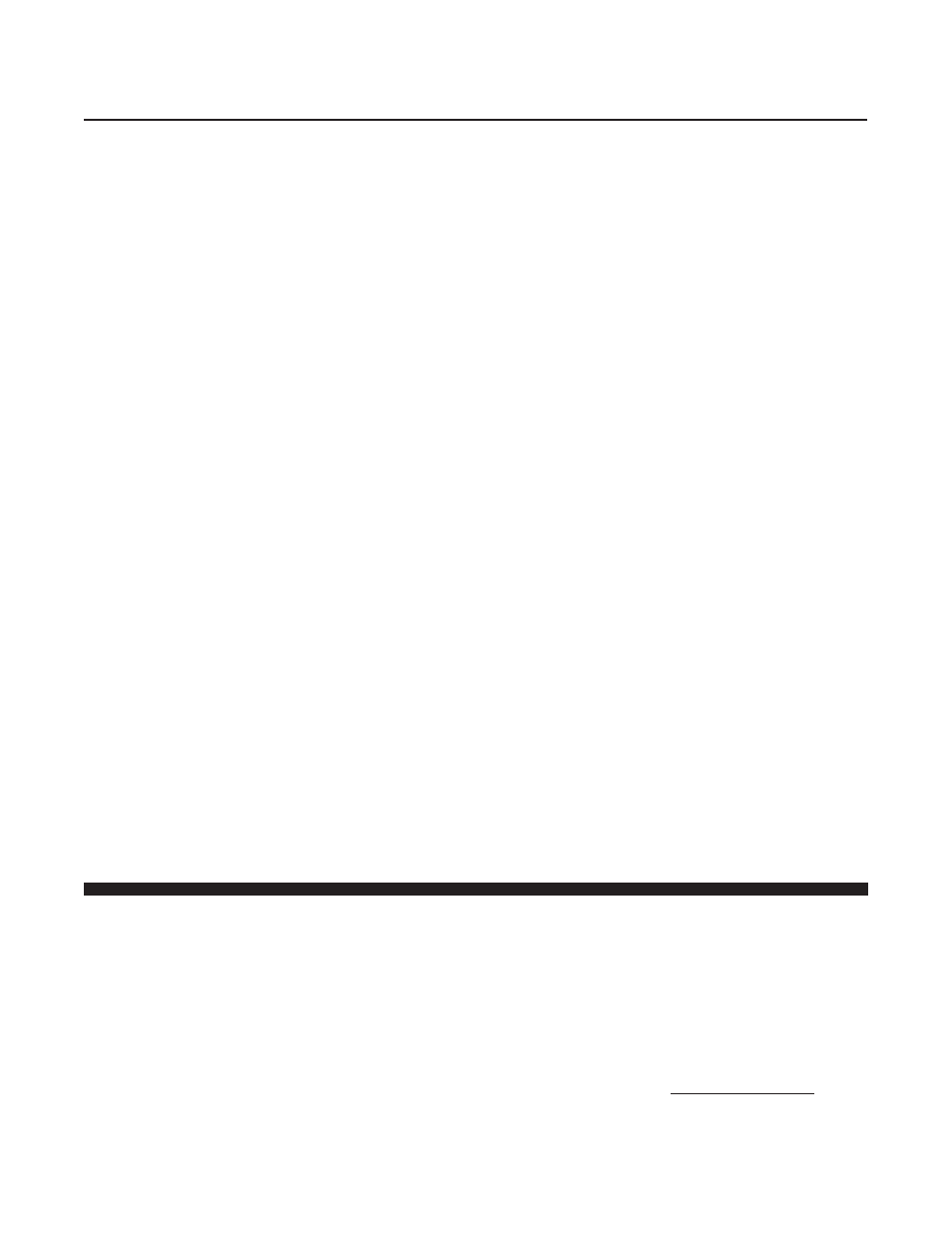
4-11
Installation and Operation Manual
X-TMF-5851i-MFC-eng
Part Number: 541B109AAG
September, 2009
Brooks
®
Model 5851
i
Section 4 Maintenance
& Troubleshooting
c. Disassemble the control valve following the procedure given in Section
4-4A above. Note the number, locations and thicknesses of all spacers
(9 and 10).
d. Decrease the preload of the valve by 0.005 inches by either removing a
0.005-inch small preload spacer or by adding a 0.005-inch large
preload spacer. Refer to Figure 4-2.
e. Reassemble the valve following the assembly procedure in Section 4-4a.
f. Adjust setpoint for zero percent flow, apply normal operating pressure
and check for valve leak-through by observing the output signal.
g. If the valve leaks through, increase the preload by 0.005" and go to
Step h. If the valve does not leak through, repeat Steps d, e, f and g.
h. Apply normal operating gas pressure and adjust setpoint for 100% flow
(5.000 Volts on terminal A, Pin 2).
Note: Due to possible heat capacity and density differences between the
test gas and actual process gas for which the MFC was sized, it may be
necessary to increase the inlet pressure to obtain proper control at 100% flow.
i. Measure the valve voltage by connecting a voltmeter between test point
3 (TP3) and test point 4 (TP4). Refer to Figure 4-3.
j1. If the flow controller output signal is 100% and the valve voltage is less
than 11.5 V, the valve adjustment is complete.
j2. If the flow controller output signal is 100% and the valve voltage is
greater than 11.5 V, decrease the air gap with a small 0.005 inch air
gap spacer. Refer to Figure 4-2. Repeat Steps h and i.
j3. If the flow controller output signal is less than 100% and the valve
voltage is greater than 11.5 V, this condition indicates that the inlet
pressure is too low and/or the orifice size is too small. First check
Section 4-6 to insure that the orifice size is correct.
k. Proceed to Section 3 and perform “3-4 Calibration Procedure,” if
required.
4-5 Use of the Conversion Tables
If a mass flow controller is operated on a gas other than the gas it was
calibrated with, a scale shift will occur in the relation between the output
signal and the mass flow rate. This is due to the difference in heat
capacities between the two gases. This scale shift can be approximated by
using the ratio of the molar specific heat of the two gases or by sensor
conversion factor. Table 4-3 has a list of sensor conversion factors. To
change to a new gas, multiply the output reading by the ratio of the gas
factor for the desired gas by the gas factor for the calibration gas used.
Actual gas
=
Output
x
factor of the new gas
flow rate
reading
factor of the calibrated gas