Bray 70 Series SERVO PRO User Manual
Page 18
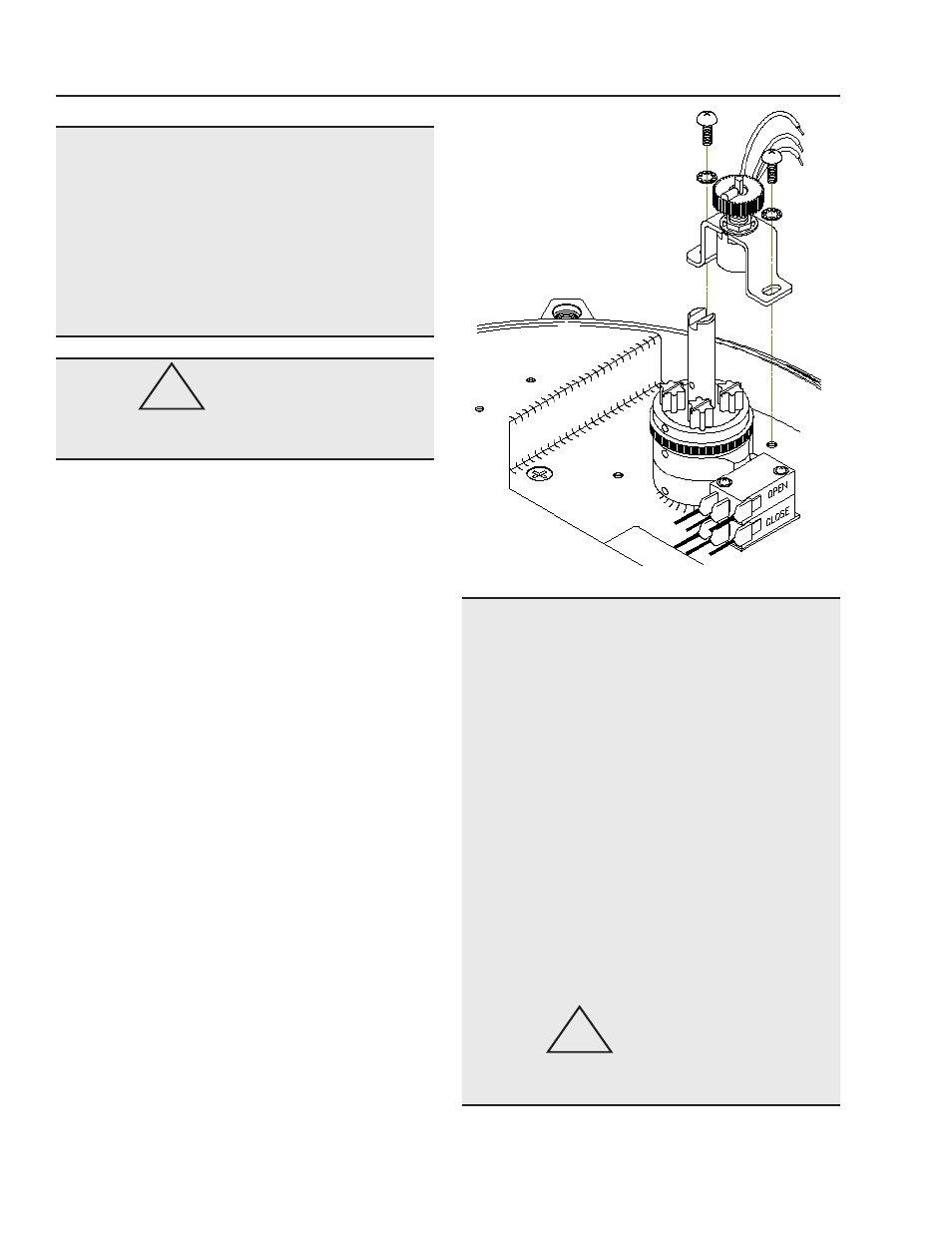
16
BRAY Series 70 Servo Pro
Operation and Maintenance Manual
notice
A torque switch that is broken, improperly wired,
or missing from the actuator can result in an open
contact which will be interpreted by the Servo Pro as
the actuator being at its max torque limit.
If the optional torque switches are not installed, select
Torque Switch Disable by setting Configuration switch
10 to ON.
caution
Do not connect any high voltage power to the torque
limit switch terminals as damage could result.
5.1.7 f
eedback
P
otentiometer
The Servo Pro uses the signal from the internal
feedback potentiometer to determine the current
actuator position.
The wiring to the feedback potentiometer is connected
at the factory and should not require any adjustment
by the customer. If a field repair is required, follow the
instructions below:
5.1.7.1 f
eedback
P
otentiometer
i
nstallation
and
c
alibration
1. Install the internal feedback potentiometer next to
the actuator indicator shaft using the two threaded
mounting holes provided.
2. The potentiometer assembly must be mounted in the
correct orientation in order to successfully calibrate
the Servo Pro.
3. Remove the indicator rotor from the indicator shaft
so that the drive slot on the top is visible.
4. Engage the handwheel (pulling it fully outward)
and manually move the actuator to the fully open
(counterclockwise) position.
5. Use the black feedback pot knob to rotate the black
feedback pot cam until the raised green rib on the
pot gear (see Figure 4 below) is directly in-line with
the slot on the top of the indicator shaft.
6. The actuator is now ready for the calibration procedure
described in Section 3.1.
notice
The wiring of the feedback pot is critical to proper
operation.
Connect the orange wire from the wiper pin of the pot
to the middle terminal.
Connect the gray wire from the fixed pin of the pot that
is closest to the wiper pin to the +5V terminal.
Connect the white wire from the fixed pin of the pot
that is farthest from the wiper pin to the COM terminal.
Connect a voltmeter between the middle terminal and
the COMMON terminal. Apply power to the Servo
Pro, move the actuator to the fully open position, and
the reading should be close to +5 VDC. Move the
actuator to the fully closed position, and the reading
should be close to 0 VDC.
caution
Do not connect any high voltage power to the feedback
pot terminals as damage could result.
f
igure
4: f
eedback
P
ot
m
ounting
and
P
ositioning
.
!
!