Bray 70 Series SERVO PRO User Manual
Page 11
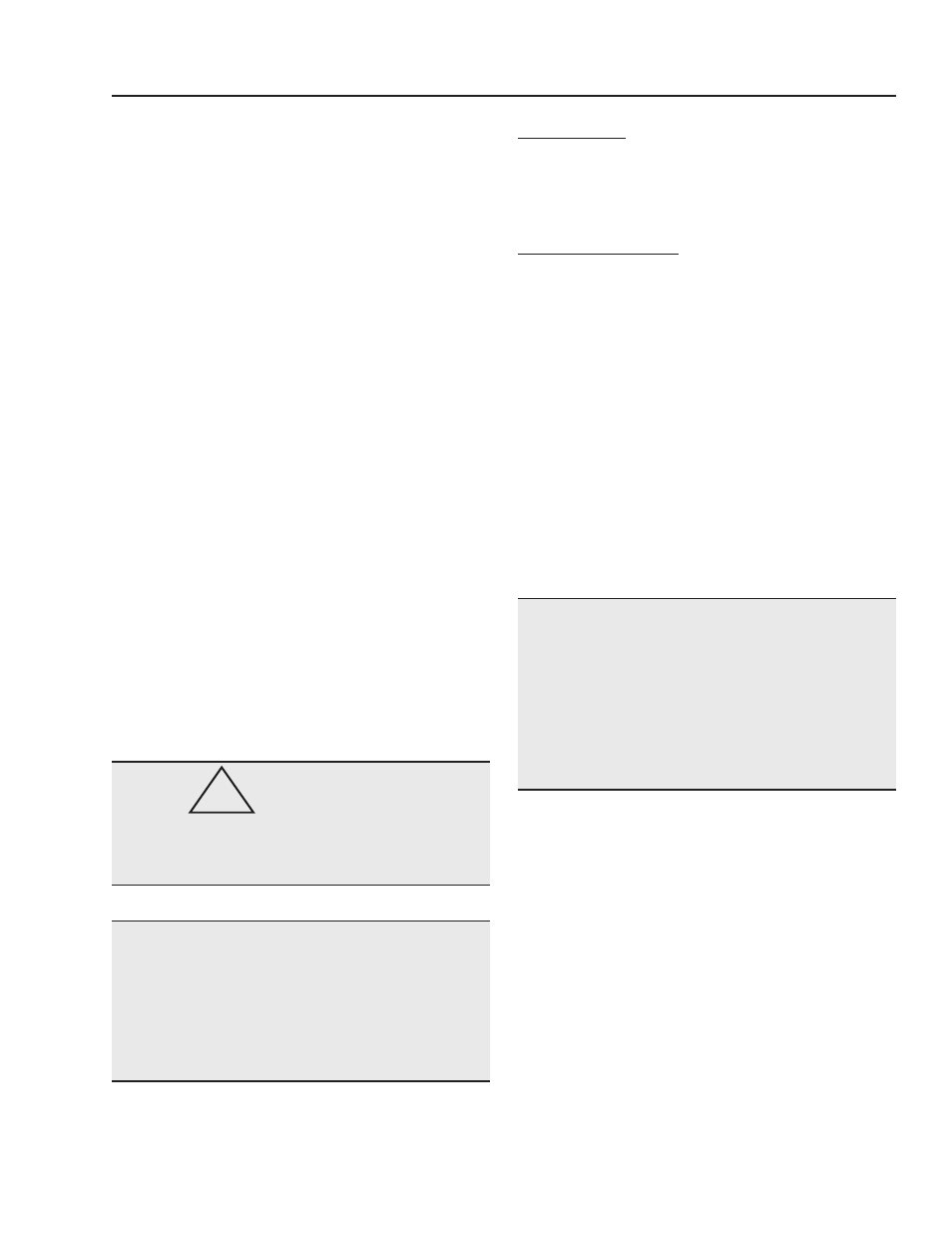
9
BRAY Series 70 Servo Pro
Operation and Maintenance Manual
E. Verify (or adjust) the travel stop limits in the actuator
a. Bray actuators are shipped with the travel switches
in the factory default position - close travel limit
set at 0 degrees and the open travel limit set at
90 degrees
b. Bray actuators equipped with Servo Pro have
the internal feedback potentiometer set in the
proper position to match the travel switch factory
default (fully close at 0 degrees and fully open at
90 degrees)
c. If the travel switch settings are moved from the
factory default position, the internal feedback
potentiometer must be adjusted to match the new
travel switch setting. This is done by performing
a calibration routine.
d. For more details on setting the travel switch
settings, refer to the S70 Operation and
Maintenance Manual.
F. Select the Torque Switch Enable or Disable
a. If optional torque switches are installed in the
actuator, select Torque Switch Enable. The
optional torque switches must be properly set and
wired to the Servo Pro. Refer to the S70 Operation
and Maintenance Manual for more information.
b. If optional torque switches are not installed in the
actuator, select Torque Switch Disable.
Warning
Before applying the appropriate electrical supply
voltage, verify that the actuator and Servo Pro have been
properly wired to the factory supplied wiring diagram.
NOTICE
To prevent noise coupling between conductors, power
lines and signal/communication lines should not be
routed together in the same conduit or cable tray. If
they must cross each other, then it should only be done
at right angles
Recommended distances below should be maintained
between power and signal/communication conduit:
Metal Conduit:
Conductor carrying less than 20A = At least 4 in.
Conductor carrying more than 20A up to 100kVA = At
least 8 in.
Conductor carrying more than 100kVA =At least 1.5 ft
Non-Metallic Conduit:
Conductor carrying less than 20A = At least 8 in
Conductor carrying more than 20A up to 100kVA = At
least 2 ft
Conductor carrying more than 100kVA = At least 3 ft.
Please refer to NEC guidelines for proper wiring
techniques in USA. Other countries must follow all local
codes for safety requirements.
Shielding
Signal/communication lines should be shielded. Shield
must be grounded at one end only, preferably at the
controller. Grounding the shield at more than one location
can introduce noise in the circuitry by forming ground
loops.
G. Apply the command signal input
notice
Ensure that your controller is able to provide the
proper command signal range given the following
input impedance values:
4-20 mA
200 Ohm
0-5 VDC
>10 MOhm
0-10 VDC
>10 MOhm
a. The command signal must be connected to the
proper terminals. Refer to the wiring diagram.
b. The command signal input must match the range
selected with the configuration switches.
c. The command signal must be a valid value (i.e.,
if 4-20 mA DC is selected, the value must be no
less than 4 mA and no greater than 20 mA.)
d. Note: a good value to select for Calibration would
be mid-travel (i.e. 12 mA DC)
Isolation Transformers
For circuits that are located in the proximity of
excessive electrical noise generators, isolation
transformers should be used to filter and prevent
noise from entering into the circuitry.
!