Bray 70 Series SERVO PRO User Manual
Page 12
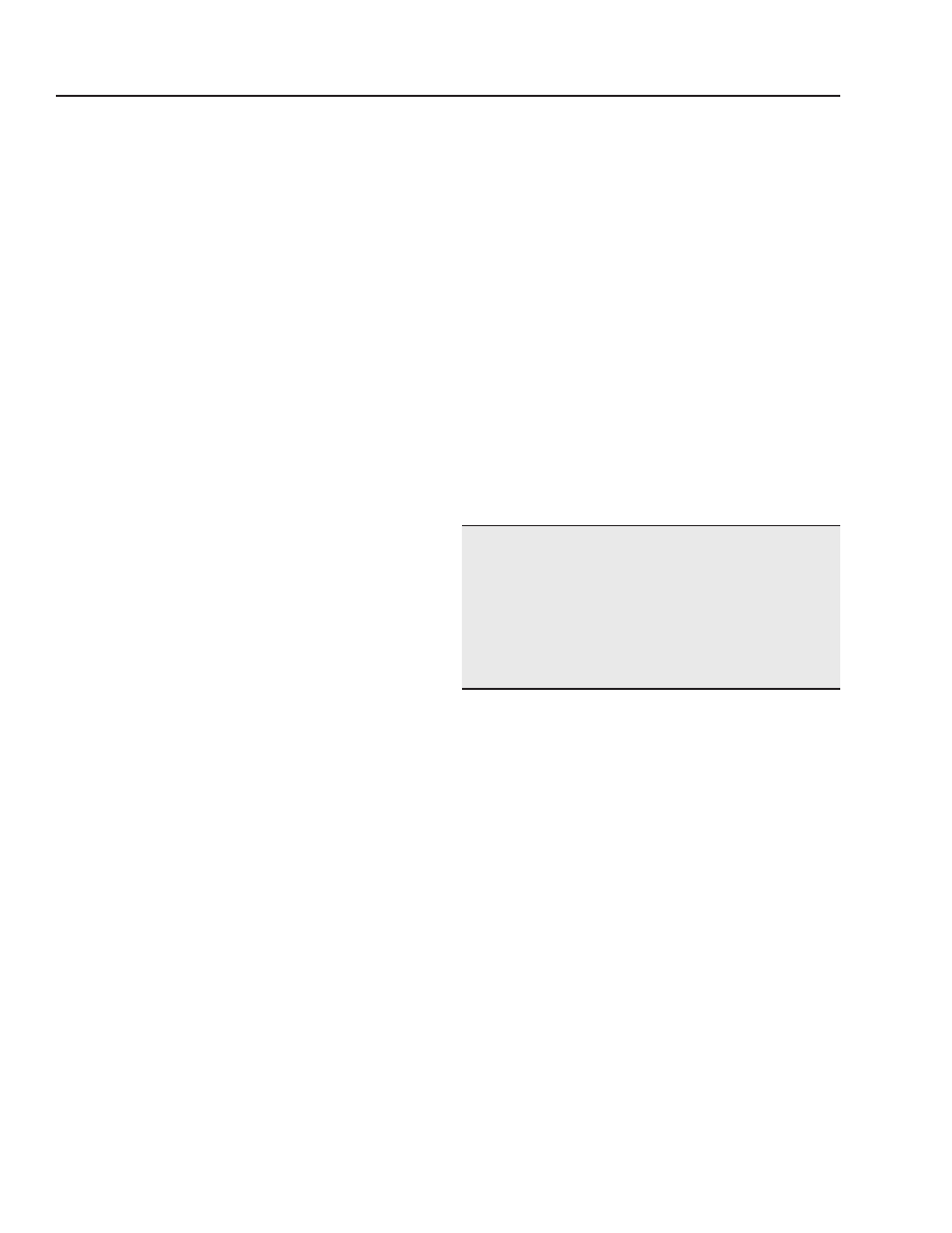
10
BRAY Series 70 Servo Pro
Operation and Maintenance Manual
Transient Suppression
Electromagnetic Interference (EMI) can result from
inductive loads, which can adversely affect electronic
circuits.
Appropriately sized surge suppressors should
be installed whenever inductive loads such as
transformers, relays, solenoids, motors, etc. are
operated. This will help prevent transient EMI surges
from damaging the sensitive electronic circuits.
H. Apply the appropriate supply voltage to the power
input terminals.
a. Verify the Status LED is flashing normal operation
– a green “heartbeat” consisting of a repeating
pattern one second on and one second off.
b. If the Status LED is flashing red, the problem must
be resolved before Calibration can begin. Refer
to the Troubleshooting section of this manual and
the Status Code Flash Table for more information.
I. Accept or Adjust the Deadband - Optional
a. The factory default is midrange – the deadband
potentiometer is midway between fully clockwise
and fully counter-clockwise. If this is acceptable,
no further adjustment is necessary.
b. Rotate the deadband potentiometer clockwise to
increase the deadband.
c. Increasing the deadband reduces the potential
for the actuator to oscillate around the desired
setpoint. This oscillation is often called “hunting.”
An actuator responding to a moving setpoint is
not hunting, but is operating properly.
d. Decreasing the deadband allows the actuator to
reach a position closer to the desired position,
as long as the actuator does not oscillate (hunt)
around the setpoint.
J. Accept or Adjust the Open Speed - Optional
a. The factory default is full speed – the open speed
potentiometer is in the fully counter-clockwise
position. If this is acceptable, no further adjustment
is necessary.
b. The full speed (fastest speed) of the actuator is
listed on the label.
c. Rotate the open speed potentiometer clockwise
to reduce the opening speed of the actuator.
d. Reducing the opening speed of the actuator can
allow more precise positioning of the actuator.
K. Accept or Adjust the Close Speed - Optional
a. The factory default is full speed – the close speed
potentiometer is in the fully counter-clockwise
position. If this is acceptable, no further adjustment
is necessary.
b. The full speed (fastest speed) of the actuator is
listed on the label.
c. Rotate the close speed potentiometer clockwise
to reduce the closing speed of the actuator.
d. Reducing the closing speed of the actuator can
allow more precise positioning of the actuator.
notice
Reducing the closing speed of the actuator can also
reduce the potential of water hammer damage. Electric
actuators are usually slow enough to avoid water
hammer even at the full speed setting – but the user
should verify this setting.
Shielding
Signal/communication lines should be shielded.
Shield must be grounded at one end only, preferably
at the controller. Grounding the shield at more than
one location can introduce noise in the circuitry by
forming ground loops.
L. Connect the Output Signal to the process controller
- Optional
a. Wire the positive conductor to the OUTPUT (+)
terminal.
b. Wire the negative conductor to the OUTPUT (-)
terminal.
c. Select the desired output signal range using the
Configuration switches 4, 5 and 6.
M. Connect the Anti-Condensation Heater – Optional
a. Connect the wires from the Anti-Condensation
Heater to the HEATER terminals
b. The Heater rating must match the voltage rating
of the Servo Pro