Bottom view, Thermal considerations – GE Industrial Solutions ATL010A0X43-SR User Manual
Page 15
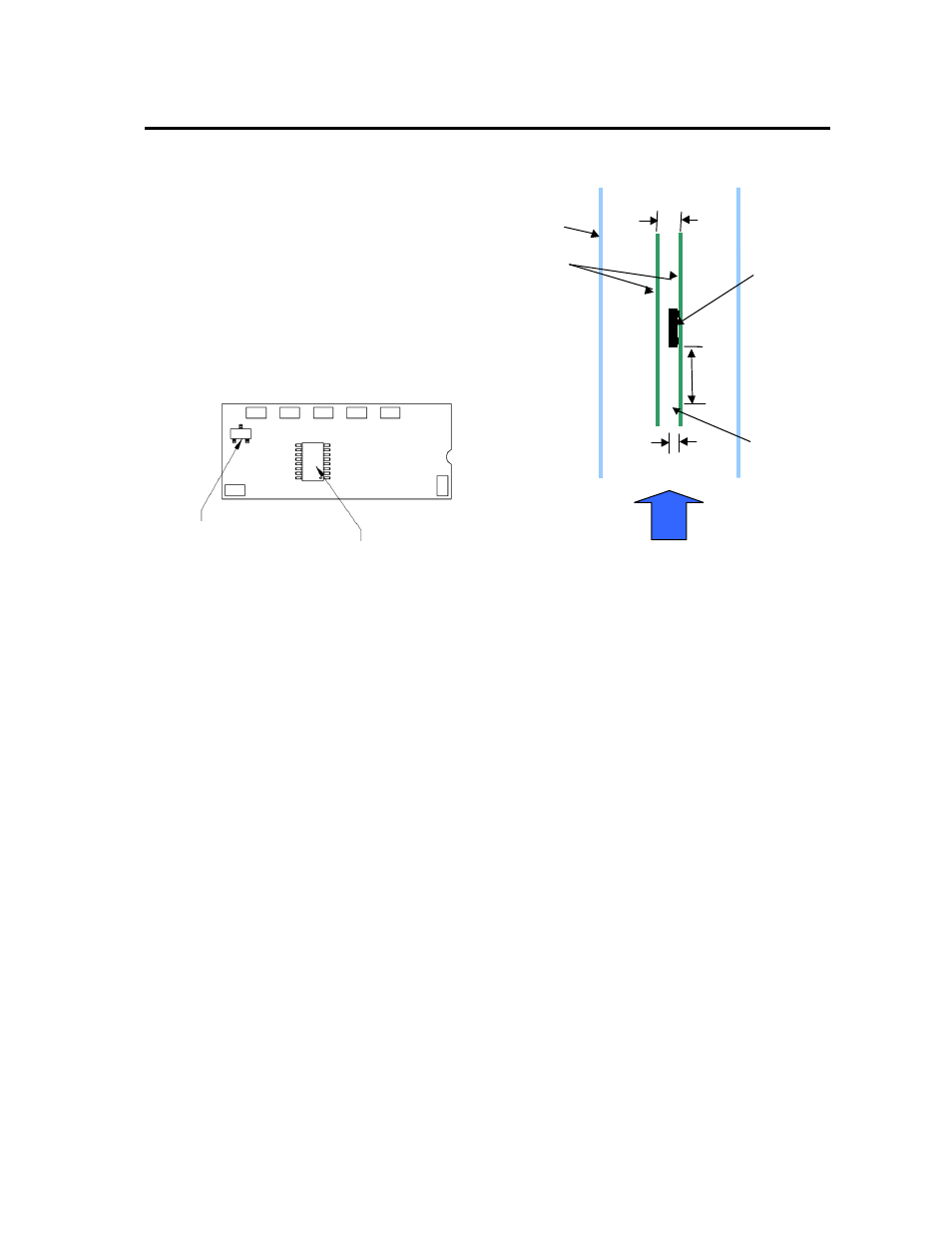
Data Sheet
September 10, 2013
ATL010A0X43-SR Non Isolated Module 12Vdc, Programmable:
9 – 18Vdc input; 0.75Vdc to 5.5Vdc Output; 10A output current
LINEAGE
POWER
15
Thermal Considerations
Power modules operate in a variety of thermal
environments; however sufficient cooling should always
be provided to help ensure reliable operation.
Considerations include ambient temperature, airflow,
module power dissipation, and the need for increased
reliability. A reduction in the operating temperature of the
module will result in an increase in reliability. The thermal
data presented here is based on physical measurements
taken in a wind tunnel. The test set-up is shown in Figure
32. Note that the airflow is parallel to the short axis of the
module as shown in figure 31. The derating data applies
to airflow in either direction of the module’s short axis.
T
ref2
T
ref1
Bottom View
Figure 31. Temperature measurement locations T
ref1
and T
ref2
.
The thermal reference points, T
ref1
and T
ref2
used in the
specifications are shown in Figure 31. For reliable
operation these temperatures should not exceed 115
o
C.
The output power of the module should not exceed the
rated power of the module (Vo,set x Io,max).
Please refer to the Application Note “Thermal
Characterization Process For Open-Frame Board-
Mounted Power Modules” for a detailed discussion of
thermal aspects including maximum device temperatures.
Figure 32. Thermal Test Set-up.
Heat Transfer via Convection
Increased airflow over the module enhances the heat
transfer via convection. Thermal derating curves showing
the maximum output current that can be delivered at
different local ambient temperatures (T
A
) for airflow
conditions ranging from natural convection and up to
2m/s (400 ft./min) are shown in the Characteristics
Curves section.
Layout Considerations
Copper paths must not be routed beneath the power
module. For additional layout guide-lines, refer to the
FLTR100V10 application note.
Air
flow
x
Power Module
Wind Tunnel
PWBs
8.3_
(0.325)
76.2_
(3.0)
Probe Location
for measuring
airflow and
ambient
temperature
25.4_
(1.0)