Theatre Solution Jury Base Seating User Manual
Page 24
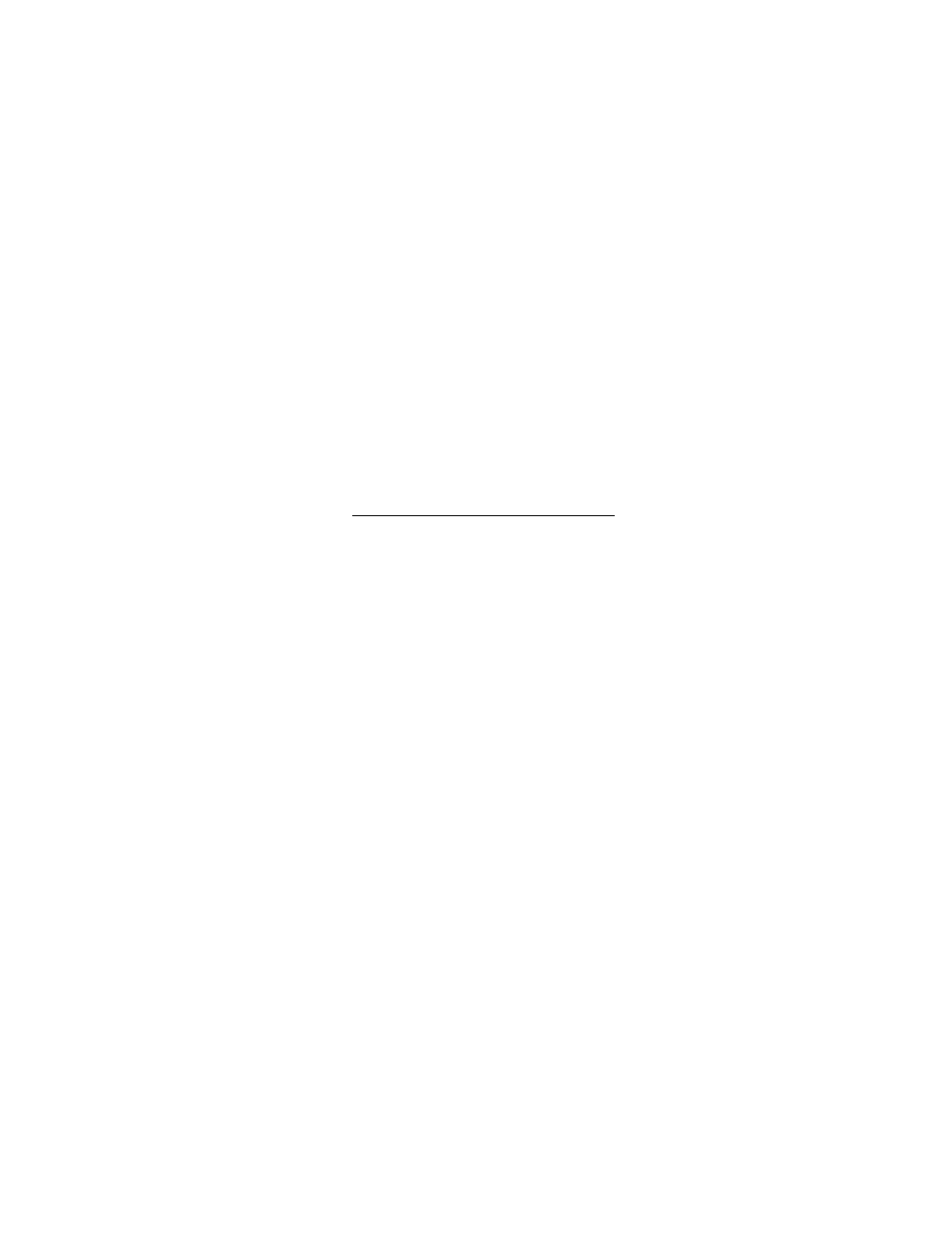
Lecture Seating Specifications
23
the need of excessive force which may cause leg fatigue in the seated occupant. Open and closed stop
positions shall be cushioned with urethane rubber to insure silent operation. Single chair assemblies are to
include fitted blank cover in the place of the second swing arm location.
2.6 CHAIRS
A. Chair shall be Herman Miller model Equa 2
®
.
B.
Chairs shall have a one piece seat and back shell constructed of injection molded, glass reinforced
thermoplastic polyester.
C.
Fully-upholstered chairs shall have a shell fully encapsulated by injection molded cold-cured polyurethane
foam. The foam shall be a nominal 1-1/2” thick on the seat and back and shall have waterfall edges. The
foamed shell shall be fully upholstered from among a variety of fabrics that shall be bonded to the foam in
contoured areas of the seat and back.
D.
The split-pad upholstered chair shall have separate seat and back cushions of injection molded, cold-cured
polyurethane foam over a polypropylene inner shell. The foam shall be a nominal 1-1/2” thick on the seat
and back and shall have waterfall edges. The cushions shall be upholstered from among a variety of
fabrics that shall be bonded to the foam in contoured areas of the seat and back. The cushions shall be
held in place with injection molded polycarbonate fasteners spin welded to the outer shell and shall snap on
and off for replacement.
E. Chair shall include a knee-tilt mechanism with a tilt tension adjustment.
F. Chair shall conform to CAL 117 requirements.
2.7 WORKSURFACES
A. Tables are to be a 3-ply warp resistant construction with a core of 1-1/8” thick 45-50 lb. density particle
board, a 0.020” Kraft backer sheet, and a face material of 0.030” high-pressure laminate.
B. The edge detail is to be (select one edge detail from the list below)
1.
3mm PVC – 3mm x 1-1/4” PVC on all table edges that would be exposed after installation, with a 1/8”
radius on the top and bottom edges. The table corners are square with an overlap joint.
2.
3mm Hardwood – 3mm x 1-1/4” hardwood on all table edges that would be exposed after installation,
with 1/8” radius on the top and bottom edges, finished to match the architect’s sample. The table
corners are square with an overlap joint.
3.
Bevel – 3/4” x 1-1/4” solid hardwood on all table edges that would be exposed after installation, with a
3/8” x 45 degree bevel detail along the top edge, finished to match the architect’s sample. The table
corners are mitered.
4.
Chamfer – 3/4” x 1-1/4” solid hardwood on all table edges that would be exposed after installation, with
a 1/4” radius on the top edge blending into a 60 degree backcut chamfer edge detail, finished to match
the architect’s sample. The table corners are mitered.
5.
Bullnose – 3/4” x 1-1/4” solid hardwood on all table edges that would be exposed after installation, with
a full 5/8” radius bullnose edge detail, finished to match the architect’s sample. The table corners are
mitered.