Trial details – GE P&W FuelSolv - Opportunity Coal Slag Control at Lakeland McIntosh Unit #3 User Manual
Page 5
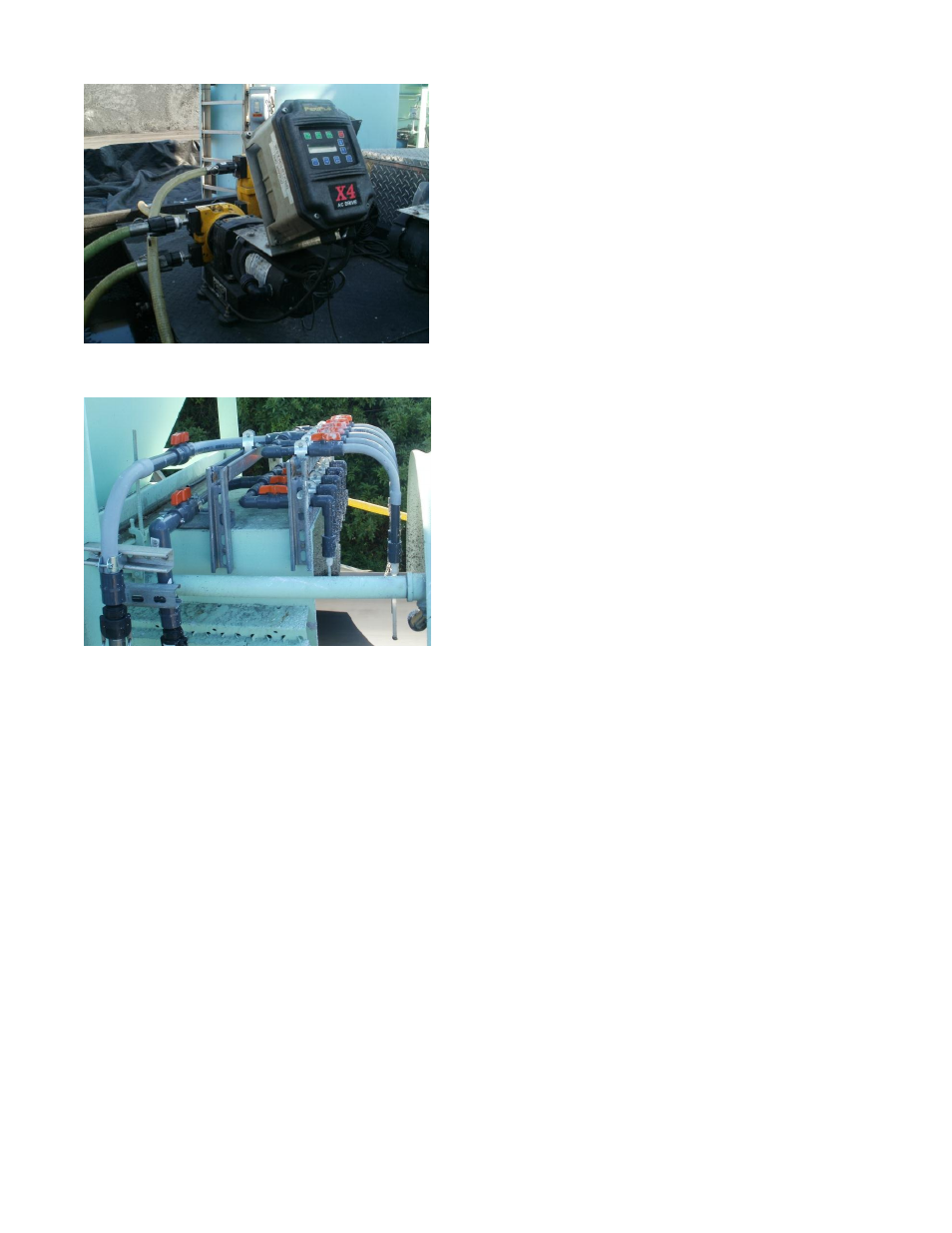
Technical Paper
Page 5
Figure 6: Variable Frequency Drive (VFD) on peristaltic
hose pumps for chemical dosage
Figure 7: Product Manifold at Coal Belt Conveyor
Dosing occurred when the coal belts conveyed a
blend of the CAPP / NAPP coal. Variable frequency
drives (VFD’s) were used to provide flexibility to dose
product across a range of coal belt bunkering rates.
The manifold was designed with valves to control
product flow onto the coal. Aqueous magnesium-
based slurry dosages were initiated at 1.5 lbs of
product per ton of NAPP coal, based on the predic-
tive model and experience with other NAPP coals.
(Tubio 2011)
Aqueous metal oxide slurry was co-fed at 0.25 lbs of
product per to on NAPP coal to synergistically miti-
gate slag accumulation. The metal oxide slurry was
fed in separate dedicated lines on the bunkering
conveyor belt.
Trial Details
To be considered successful, the trial’s main objec-
tive included determining the optimum product feed
rates of both chemical products for the CAPP/NAPP
blends while monitoring (with an infrared (IR) cam-
era) real-time slagging phenomena. Numerous
observation ports on 14 separate levels were
identified and labeled. Visual observations during
the trial focused on approximately four ports on
each of nine levels. Infrared and visual photog-
raphy records were included in the trial evalua-
tion.
Data was recorded during the “baseline” (100%
CAPP coal) and chemical treatment trial periods,
assuming equipment parameters such as tube
cleanliness, and sootblower availability were con-
stant over time. Lakeland’s fuel blends included
ranging from 12% NAPP to 75% NAPP.
During the chemical trial, the unit was kept at full
load as long as possible. Overnight load shedding
allows the slag to contract in the cooler flue gas,
and this uneven contraction in the matrix causes
cracks and gravity-assisted removal of the accu-
mulated slag. This beneficial procedure was not
conducted during most of the chemical trial so the
system could experience “worst case” stress.
The trial began on May 17 with 50% Ramsey
(NAPP) / 50% Blanton (CAPP) fed to one of 4 silos
(12% NAPP overall). The coal was dosed at 1.5
lbs/ton magnesium-based product and 0.25
lbs/ton metal oxide-based product, on the coal
belt en route to bunkering silos.
By May 23, two of 4 silos received 50% Ramsey /
50% Blanton (25% NAPP overall). The trial results
looked promising, and the trial resumed after
Memorial Day holiday. By June 3, the trial team
had ramped up to an aggressive 75% NAPP coal
blend, dosed with only 1.5 lbs magnesium-based
product per ton and 0.25 lbs metal oxide-based
product per ton. Although the low slagging level
remained acceptable, Lakeland began to experi-
ence increasing SO
3
emissions. McIntosh Unit #3
is equipped with a hydrated lime sorbent system
for SO
3
-related “blue plume” abatement. Howev-
er, it was decided that the sorbent system could
remain offline and instead Operations would trim
opportunity fuel to avoid potential SO
3
issues.
By June 7, the opportunity coal was exhausted,
and delayed train shipments resulted in the next
delivery in August. Infrequent coal shipments re-
sulted in the trial spanning several months, which
made it challenging to “optimize” dosage without
risking boiler slagging. Figure 8 summarizes the
trial dosing schedule.