Trial design – GE P&W FuelSolv - Opportunity Coal Slag Control at Lakeland McIntosh Unit #3 User Manual
Page 4
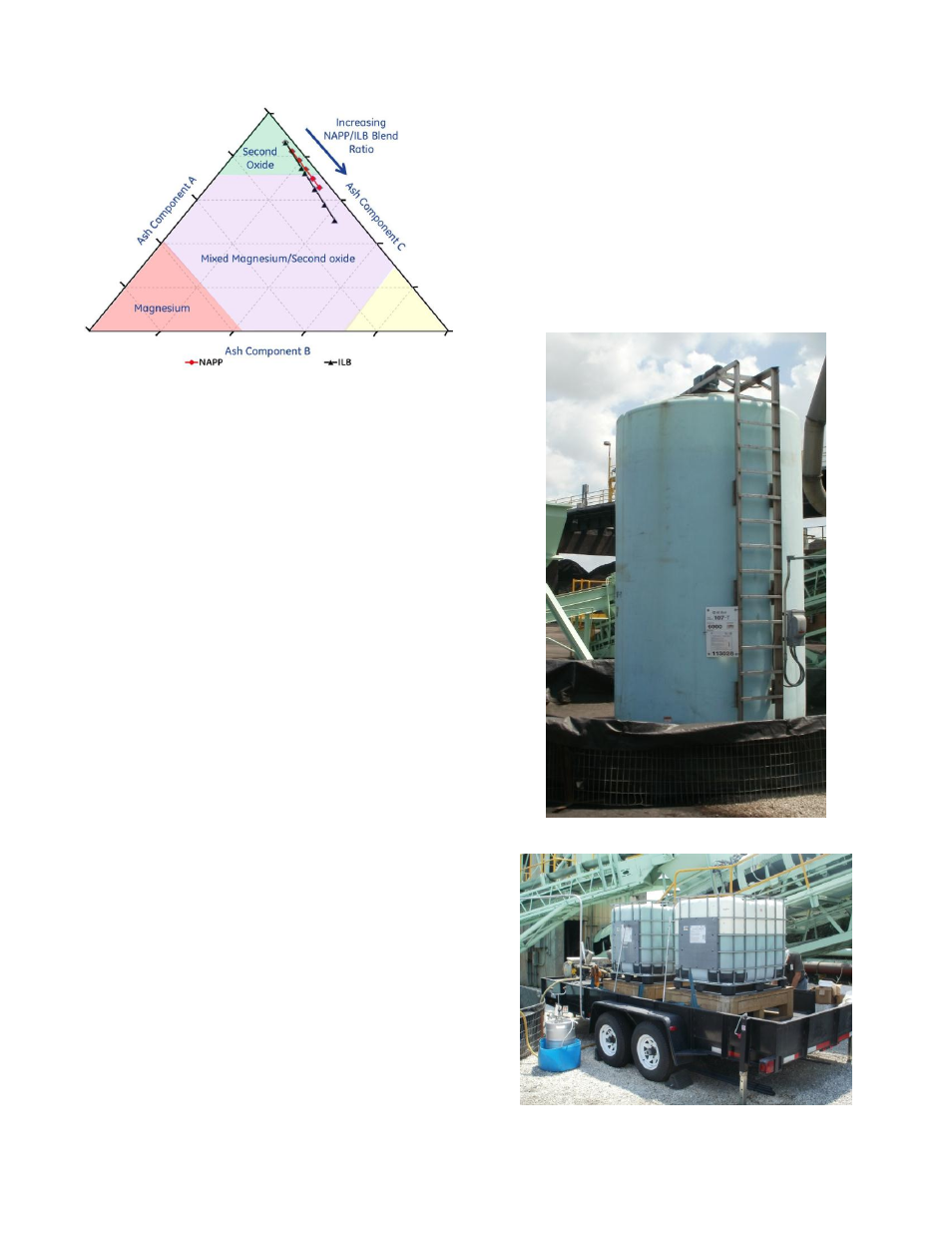
Page 4
Technical Paper
Figure 3: Predictive Model Output
The proprietary mix of additives selected for this trial
included a magnesium-based compound and a
metal oxide-based slurry. The magnesium is known
in the industry to elevate ash fusion temperatures
due to the high melting point of magnesium oxide.
This treatment keeps the slag in a solid state instead
of liquid-phase deposit.
The metal oxide-based slurry contains copper which
has been used in the industry as a combustion cata-
lyst. Less well known is that copper can reduce the
cohesive strength of the ash via a nucleating effect
with iron species. Gradual thermal decomposition
of the metal oxide product also makes the slag po-
rous and, therefore, weaker. These mechanisms
complement the magnesium’s effect for certain
types of coals or coal blends, depending on the ratio
of minerals and other non-combustible species. To-
gether, the proprietary additives create fracture
planes in the solidified slag, weakening the deposits
so that they can be more easily removed by soot-
blowers.
Trial Design
Utility experience indicates boiler conditions can
deteriorate within days of introducing an opportuni-
ty fuel. (Tubio 2011, Gabriel 2011) To minimize the
risks of forced boiler outage during trial, Lakeland
blended its typical CAPP fuel with a small proportion
of opportunity NAPP fuel. The coal blend was treat-
ed with a mix of proprietary chemical additives to
reduce severity of fireside slagging. Product dosag-
es were optimized as the percentage of opportunity
coal was increased until it reached the target level
of 50 percent.
The chemical additives were transferred from agi-
tated bulk tank and trailer-mounted base tote to
the coal belts via peristaltic pumps, where the
chemicals were the dosed at predetermined
amounts via a manifold mounted above the coal
conveyor (Figures 4 through 7). The magnesium
slurry was stored in an 8,000 gallon tank, sized to
receive a full bulk tanker truck of product, and
equipped with secondary containment. The prod-
uct requires agitation to avoid suspended solids
settling out. The metal oxide slurry was provided
in convenient 270-gallon totes.
Figure 4: Agitated Bulk Storage Tank
Figure 5: trailer-mounted base totes