Slag and fouling mechanisms, Chemical additives – GE P&W FuelSolv - Opportunity Coal Slag Control at Lakeland McIntosh Unit #3 User Manual
Page 3
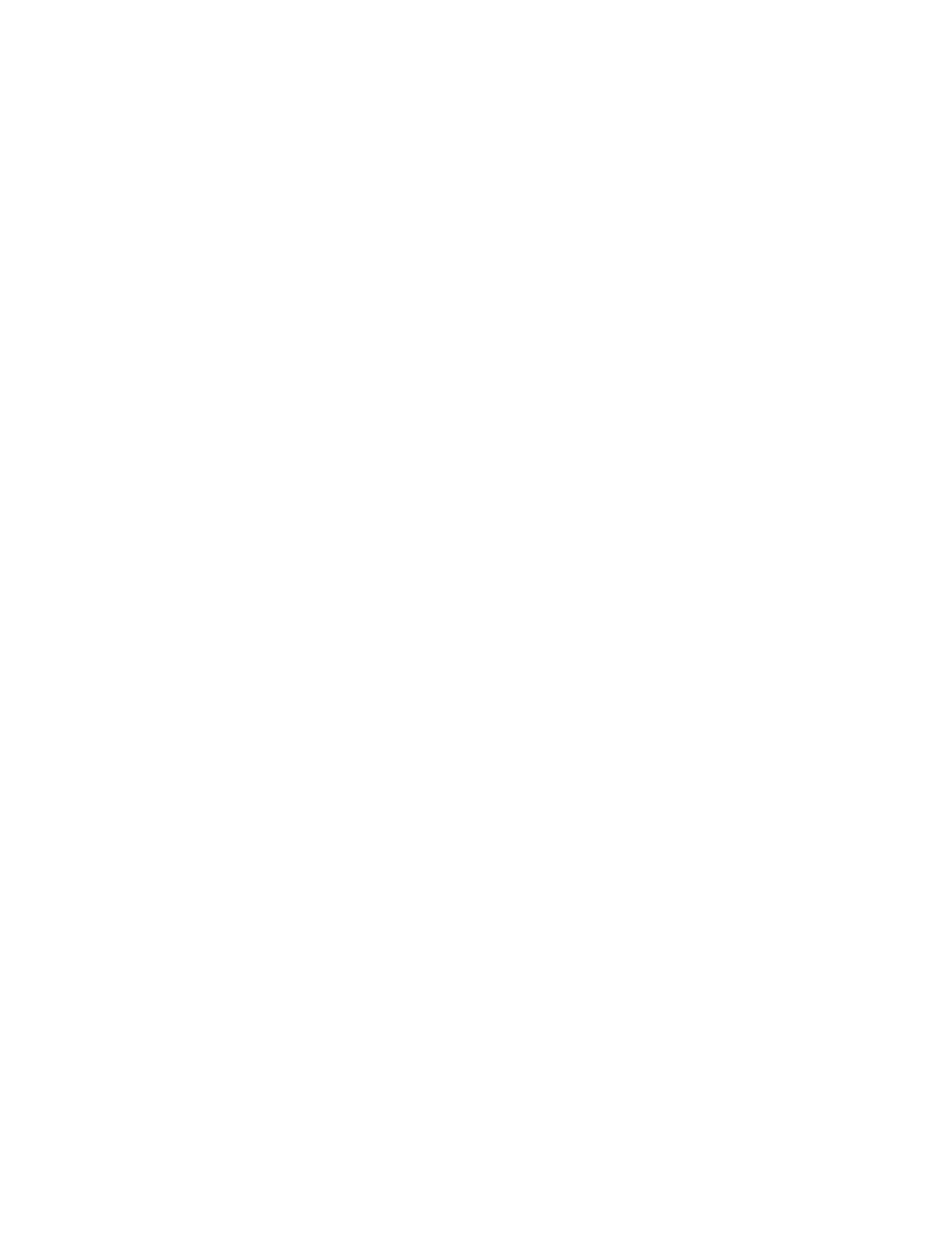
Technical Paper
Page 3
Slag and Fouling Mechanisms
In addition to carbon, coal contains numerous non-
combustible inorganic impurities such as minerals
and metals, as shown in Figure 2. Depending on the
concentrations and ratios of these minerals and
metals, slagging and convective pass fouling can
occur in boilers. Slag formation accelerates when
the furnace exit gas temperature (FEGT) is greater
than the ash fusion temperature of the ash, because
the slag is then in a more liquid state.
Slag density increases with time and temperature,
and hard sintered deposits are difficult to remove
with sootblowing. Similarly, sticky deposits which
attract flyash and exhibit “pseudo-plastic” proper-
ties cannot easily be removed by sootblowing be-
cause they deform under pressure, instead of being
removed from the tubes.
Fouling is closely related to slagging and usually oc-
curs in the boiler’s cooler convective back-pass sec-
tion. Vapors such as sodium and potassium
condense onto the cooler tubes in the reheater and
primary superheater areas. Fouling deposits can
“bridge” across tubes and restrict gas flow. That
increases induced fan horsepower, increasing the
plant heat rate and, therefore, lowers plant efficien-
cy.
Slagging and fouling can result in derating (shed-
ding load) and costly unscheduled outages and re-
pairs from damaging slag falls. But these problems
can be eased by combining chemical additives for
fireside applications with operational and mechani-
cal changes, including sootblower placement and
operation.
Chemical Additives
The three important aspects for every fireside pro-
gram are mechanical, operational, and chemical
parameters. Mechanical aspects include details like
tube spacing and sootblower locations. Operational
aspects include load shedding and sootblowing fre-
quency. When those two categories have been
thoroughly explored and persistent slagging issues
remain, it is time to consider the third parameter:
chemical treatment.
Chemical additives have exhibited interesting prop-
erties including increasing ash fusion temperature,
increasing deposit friability and even changing the
crystal structure in the slag to create microscopic
cracks. These chemical and physical changes
weaken the deposits and allow them to be more
easily removed by sootblowers.
The selection and dosing of chemical additives is
typically accomplished by a thorough analysis of
coal including ash composition. The mineral con-
tent is input into one of the common slagging in-
dex calculators such as basicity ratio. Based on
the result, the treatment is selected that can move
the index in the desired direction. In cases where
the application is focused on a single type of coal,
this approach can lead to good results in many
cases, considering primarily bulk phase effects.
When opportunity coals are blended, additional
complications develop beyond those seen with
single coal analyses. Blended coals not only have
mixed ash chemistries but the blending ratios can
change based on coal availability, operations, or
economics. The overall effect of anti-slagging ad-
ditives needs to be considered across the range of
potential ash chemistries.
At Lakeland, GE Water used a prototype predictive
model to look at coal chemistry and identify the
proper treatment approach. While standard
models generally look at bulk chemical effects, the
model used at Lakeland utilizes a complex analyt-
ical process to account for effects of formation of
microscopic crystal structures and other physical
parameters that can affect slag density and re-
moval. A range of chemical additives were con-
sidered before a two products approach was
selected based on thorough analyses of the fuels.
The ash composition for a series of blends ranging
from 100% CAPP to 100% NAPP or ILB was input
into the model. Across all blend ratios for both
opportunity coals the model clearly indicated that
the addition of a copper based metal oxide com-
pound would be the most effective anti-slagging
agent. The model indicated the use of magnesi-
um based chemistries would be effective at higher
blend ratios of lower rank coals – particularly with
ILB coal.
Overall, the model suggested that a combination
of products would be the most successful ap-
proach to provide flexibility and optimization for
each blend, (Figure 3). When using lower blend
ratios of opportunity coal, the magnesium dosage
may decrease and total treatment cost will be re-
duced.