Torque-angle tutorial, Torque vs load, Torque-angle vs load – Snap-On Motorized Loader User Manual
Page 2
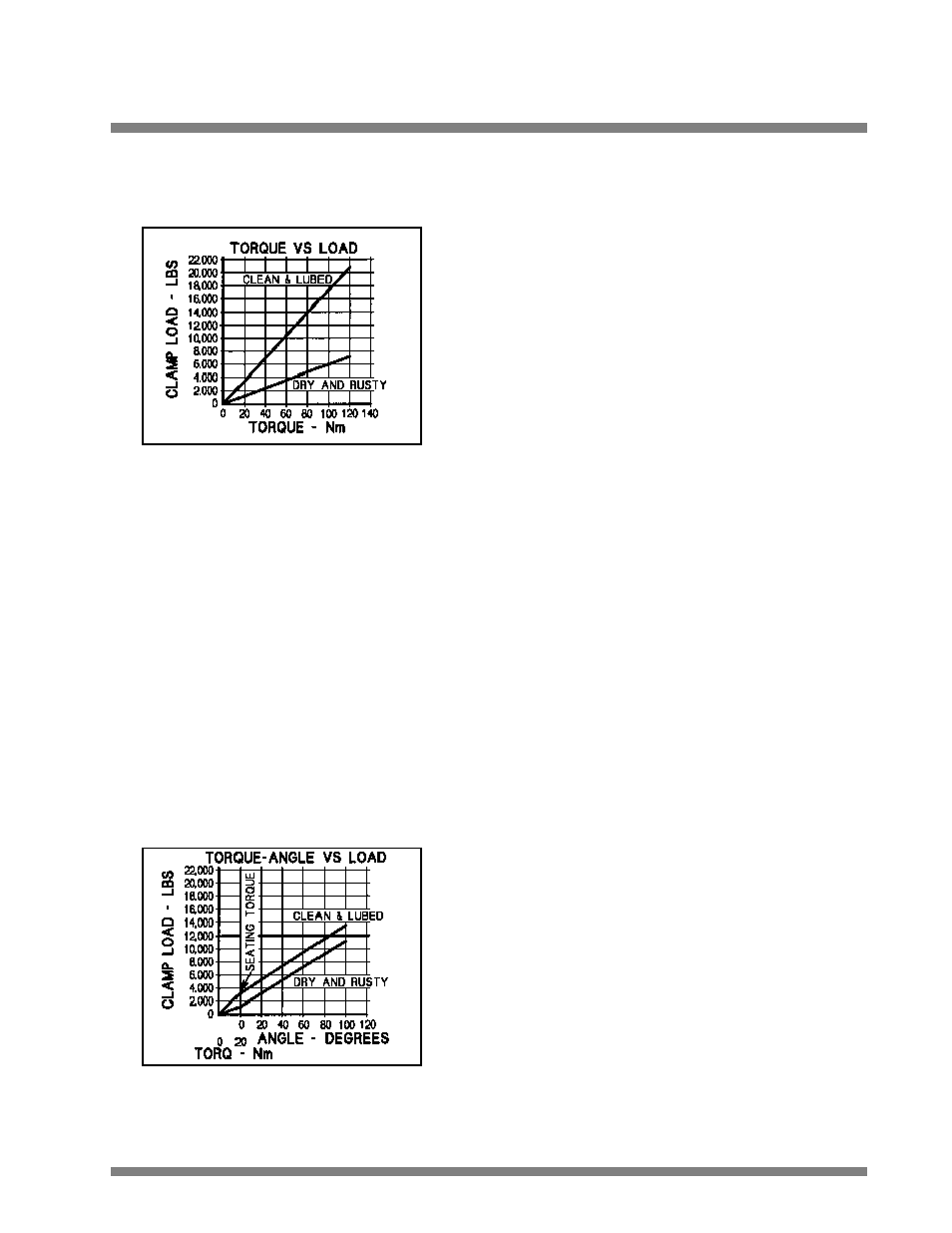
Torque-Angle Tutorial
Torque vs Load
Today’s torque wrenches are very accurate.
Unfortunately, torque can be a poor
parameter to measure when you’re really
interested in controlling load. As shown in
the
Torque vs Load graph at left, 120
Newton-meters of torque applied to a dry
and corroded bolt only produces 7,000
pounds of clamping load in a sample joint.
This same bolt, cleaned and lubricated,
results in nearly 21,000 pounds of load for
the same 120 Nm applied. That’s 14,000
lbs of uncertainty.
The torque applied to a fastener (bolt or
screw) is absorbed in three main areas.
Over half of the total torque is lost to
underhead friction. About a third of the
torque is absorbed by the fastener threads.
This leaves about 10 percent of the applied
torque that actually develops into clamping
load which holds a bolted assembly
together. Unless the frictional forces have
been carefully predetermined and controlled
in some way, such as with special lubricants
or expensive joint preparation, torque will
never consistently relate to tightness.
Torque-Angle vs Load
When a fastener is installed, it stretches.
This stretch (bolt tension) can be calculated
very accurately by using the bolt length,
slope of the threads (threads per inch) and
fastener turns (degrees of rotation). As
shown in the
Torque-Angle vs Load graph at
left, once seated, rotation is directly related
to load regardless of bolt condition. In this
case, a small torque is used to seat the
fastener and 100 degrees of rotation
produces the required 12,000 lbs of load
with less than 2,000 lbs of uncertainty.