0 filling the xdf with coolant-water or glycol, 1 preparing the system for filling, 1 xdf water/glycol cooled unit volume – Emerson Liebert XDF User Manual
Page 36: Table 6 volume in standard type “l” copper piping, 2 filling the system with water or glycol, Illing, With, Oolant, Ater, Lycol
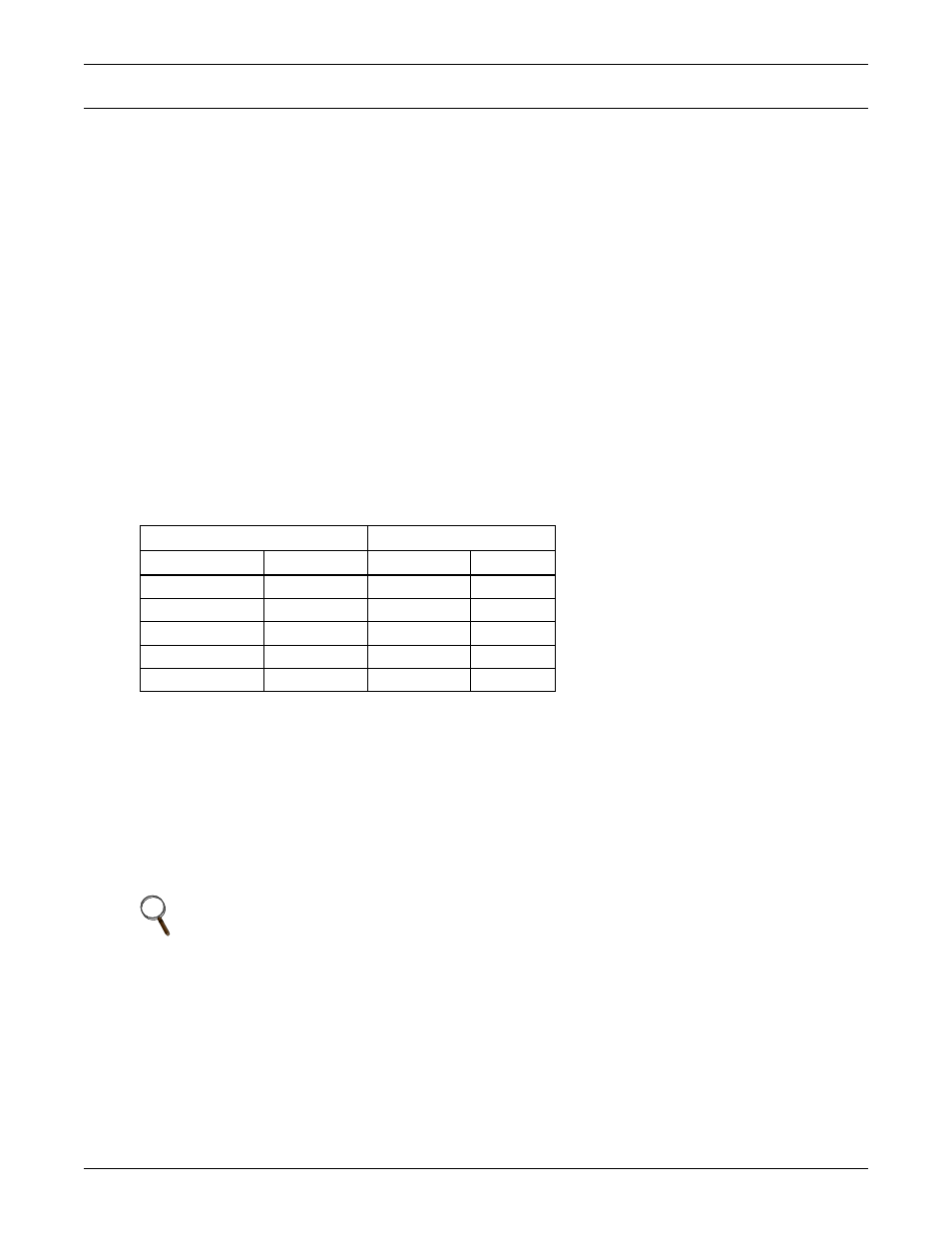
Filling the XDF with Coolant—Water or Glycol
30
6.0
F
ILLING
THE
XDF
WITH
C
OOLANT
—W
ATER
OR
G
LYCOL
6.1
Preparing the System for Filling
It is important to remove any dirt, oil or metal filings that may contaminate the cooling system piping
in order to prevent contamination of the coolant and fouling of the drycooler piping (IF USED). The
system should be flushed thoroughly using a mild cleaning solution or high-quality water and then
completely drained before charging with coolant.
Cleaning new systems is just as important as cleaning old ones. New systems might be coated with oil
or a protective film; dirt and scale are also common. Any residual contaminants could adversely affect
the heat transfer stability and performance of your system. In many cases, in both old and new sys-
tems, special cleaners are needed to remove scale, rust and hydrocarbon foulants from pipes, mani-
folds and passages. Clean heat transfer surfaces are important in maintaining the integrity of the
cooling system. For more information on cleaners and degreasers, contact your sales representative.
Calculate the internal volume of the system as closely as possible. See Table 6 and Table 3 for unit
volumes. Use volume in Table 6 for glycol piping volumes.
6.1.1 XDF Water/Glycol Cooled Unit Volume
The water/glycol cooled XDF’s coolant capacity is 0.56 of a gallon (2.1 liters). In closed systems, addi-
tional coolant will be required for the piping. Refer to Table 6 for required amounts for various piping
sizes.
6.1.2 Filling the System with Water or Glycol
When filling the XDF with either water or glycol, keep air to a minimum. Air in glycol turns to foam
and is difficult and time-consuming to remove. (Anti-foam additives are available and may be consid-
ered.)
1. Open all operating systems to the loop.
2. With the top vent(s) open, fill the system from the bottom of the loop. This will allow the coolant to
push the air out of the top of the system, minimizing trapped air.
3. Fill to approximately 80% of calculated capacity.
Fill slowly from this point, checking fluid levels until the system is full.
Table 6
Volume in standard Type “L” copper piping
Diameter (in.)
Volume
Outside
Inside
Gal/Ft
L/M
1/2 0.123
0.008
0.01
5/8 0.555
0.012
0.15
3/4 0.666
0.018
0.22
7/8 0.785
0.025
0.31
1-1/8 1.025
0.043
0.53
NOTE
For glycol solution preparation and periodic testing, follow manufacturer's recommendations.
Do not mix products of different manufacturers.