Sealey TA303 User Manual
Page 4
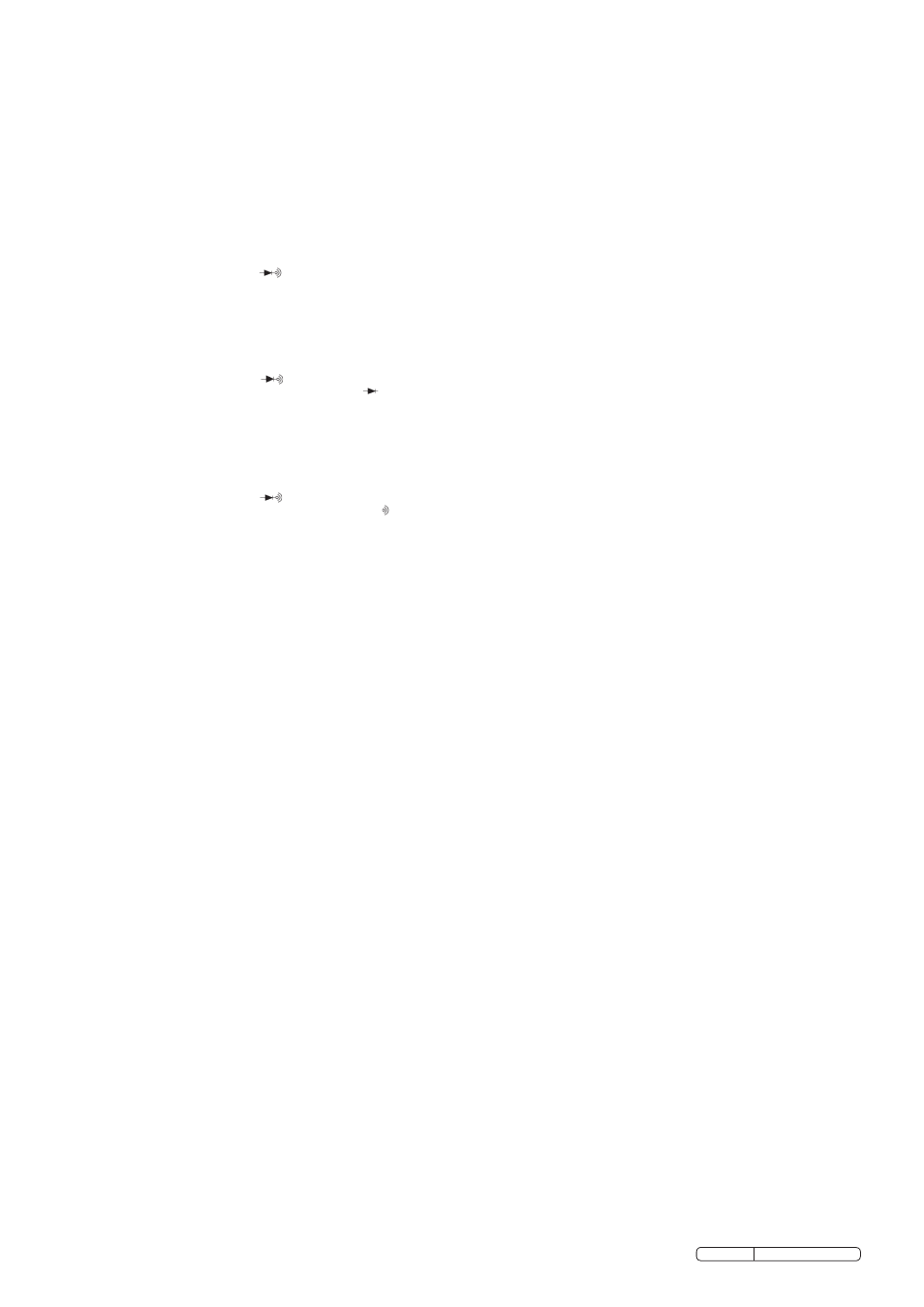
4.8.
AC and DC Current Measurement
WARNING! Do not make current measurements on the 400mA and 20A ranges for longer than 30 seconds. Allow 5 minutes for cool down
before commencing measurements again. Exceeding 30 seconds may cause damage to the meter and test leads.
4.8.1. Insert the black test lead into the negative “COM” jack and the red test lead into either the Positive 400mA jack for currents up to 400mA (fig.1.9) or
the Positive 20A jack for currents from 400mA to 20A (fig.1.8).
Note: If you are unsure of the current draw, select the 20A jack first.
4.8.2. Turn the rotary switch to the 20A or mA position.
4.8.3. Press the mode button to select AC or DC current.
WARNING! Be sure to disconnect the power supply from the circuit.
4.8.4. Touch the test probes
in series with the circuit under test. Turn the power on to the circuit, and read the current displayed.
4.9.
Resistance Measurement
WARNING! To avoid electric shock, disconnect power to unit under test and discharge all capacitors before taking any resistance
measurements. Accurate resistance measurement cannot be taken if voltage is present. Only measure in non-powered circuits.
4.9.1. Insert the black test lead into the negative “COM” jack and the red test lead into the positive
VΩHz% etc.
jack.
4.9.2. Turn the rotary switch to the position.
4.9.3. Press the Mode button (fig.1.12) to select the resistance Ω mode.
4.9.4. Connect the test probes to the two ends of the resistance circuit to be measured.
4.9.5. read the measured value on the display.
4.9.6. If greater accuracy is required, press the range button to select the desired range.
4.10.
Diode Test
IMPOrTAnT: Turn the power OFF to the test circuit
4.10.1. Insert the black test lead into the negative “COM” jack and the red test lead into the positive
VΩHz% etc.
jack.
4.10.2. Turn the rotary switch to the position.
4.10.3. Press the Mode button (fig.1.12) to select the Diode mode.
4.10.4. Connect the test probes to the two ends of the Diode to be tested, read the measured value on the display.
4.10.5. reverse the test probes on the two ends of the Diode to be tested, read the measured value on the display again.
4.10.6. When measuring the voltage across a good Diode, it will be high in one direction and low in the other, A defective diode will read the same in both
directions or read between 1.0 to 3.0 V. in both directions
4.11.
Continuity Test
WARNING! When checking continuity, be sure to disconnect the power supply from the circuit.
4.11.1. Insert the black test lead into the negative “COM” jack and the red test lead into the positive
VΩHz% etc.
jack.
4.11.2. Turn the rotary switch to the position.
4.11.3. Press the Mode button (fig.1.12) to select the continuity mode.
4.11.4. Connect the test probes to the two ends of the circuit to be tested.
4.11.5. If there is a complete circuit, the analyser will beep continuously. If the circuit is open, there will be no beep and the display will show OL (over limit)..
4.12.
Capacitance Measurement
WARNING! When checking in-circuit capacitance, be sure to disconnect the power supply from the circuit and that the capacitors are fully
discharged.
In order to obtain an accurate reading, a capacitor must be discharged before measurement begins. The meter has a built-in discharge mode to
automatically discharge the capacitor. In discharge mode, the LCD displays “DIS.C”. However discharging through the chip is quite slow. We recommend
that some other apparatue is used to discharge the capacitor.
4.12.1. Insert the black test lead into the negative “COM” jack and the red test lead into the positive
VΩHz% etc.
jack.
4.12.2. Turn the rotary switch to the CAP position.
4.12.3. Touch the test probes to the ends of the capacitor and read the capacitor value on the display.
Note: The bar graph is disabled in capacitance measurement mode. However, since the measurement time in the 4mF and 40mF ranges is quite long
(3.75s and 7.5s respectively), the bar graph is used to display the time taken to accomplish the measurement.
4.13.
Frequency Measurement
4.13.1. Insert the black test lead into the negative “COM” jack and the red test lead into the positive
VΩHz% etc.
jack.
4.13.2. Turn the rotary switch to the Hz position.
4.13.3. Connect the negative test probe to ground.
4.13.4. Connect the positive test probe to the “signal out” wire of the sensor to be tested.
4.14.
Duty Cycle Measurement
4.14.1. Insert the black test lead into the negative “COM” jack and the red test lead into the positive
VΩHz% etc.
jack.
4.14.2. Turn the rotary switch to the %DuTY position.
4.14.3. Connect the negative test probe to ground.
4.14.4. Connect the positive test probe to the signal wire circuit.
4.15.
Temperature Measurement
WARNING! To avoid heat damage, it is important to keep the analyser away from very high heat sources. The life of the probe is also reduced if
exposed to very high temperatures. Probe operating range is -58°F to 482°F.
4.15.1. Insert the type K thermocouple plug into the analyser using the negative “COM” jack and the positive
VΩHz% etc.
jack - ensuring the '+' symbol on the
plug is inserted into the positive
VΩHz% etc.
jack.
4.15.2. Turn the rotary switch to either the °C or °F position as required.
4.15.3. Place the end of the thermocouple's tip on the object to be measured.
4.15.4. read the temperature on the display.
4.16.
Pulse Width Measurement
4.16.1. Insert the black test lead into the negative “COM” jack and the red test lead into the positive
VΩHz% etc.
jack.
4.16.2. Turn the rotary switch to the ms-PuLSE position.
4.16.3. Press the range button until the negative (-) trigger slope is displayed on the right of the display.
Note: The applied time for most fuel injectors is displayed on the negative (-) slope.
4.16.4. Connect jumper wires between the fuel injector and the harness connector.
4.16.5. Connect negative test probe to a good ground at the fuel injector. or the negative (-) vehicle battery terminal.
4.16.6. Connect the red test probe to the fuel injector solenoid driver input on the jumper cable.
4.16.7. Start the vehicle's engine. A pulse width in milliseconds should be displayed.
Note: Initially the reading will be 'OL', then the reading will descend and stabilise to the actual pulse width. If 'OL' remains, re-check the connections.
This can also be used to measure other automotive applications such as fuel mixture control solenoids and Idle air control motors.
4.17.
RPM Measurement
4.17.1. Insert the inductive pick-up leads into the analyser. Plug the black lead into the negative “COM” jack and the red lead into the positive VΩHz% etc. jack.
4.17.2. Turn the rotary switch to either the rPM or x10 rPM position as required ( for the X10 rPM range, multiply the displayed reading times by 10 to get the
actual rPM).
4.17.3. Press the range button (fig.1.3) to select through rPM 4 for 4-stroke, or rPM 2 for 2-stroke and DIS systems.
Note: rPM 4 for rPM of 4-stroke engines which have 1 ignition on every 4 engine strokes.
rPM 2 for rPM of DIS (Distributerless Ignition System) & 2-Stroke engines which have 1 ignition on every 2 engine strokes.
4.17.4. Connect the inductive pick-up to a spark plug HT lead. If no reading is received, unhook the clamp, turn it over and connect again.
Note: Position the pick-up as far away from the distributor and exhaust manifold as possible.
Position the pick-up to within 15cm of the spark plug, or move it to another plug HT lead if no reading or an erratic reading is obtained.
The inductive pick-up has an adjustable sensitivity switch that may also be used to correct an unstable reading.
Keep the analyser away from the engine to ensure a stable reading is obtained.
TA303 Issue no: 2 - 20/12/11
Original Language Version
Ω
Ω
Ω