Sealey TA090 User Manual
Page 11
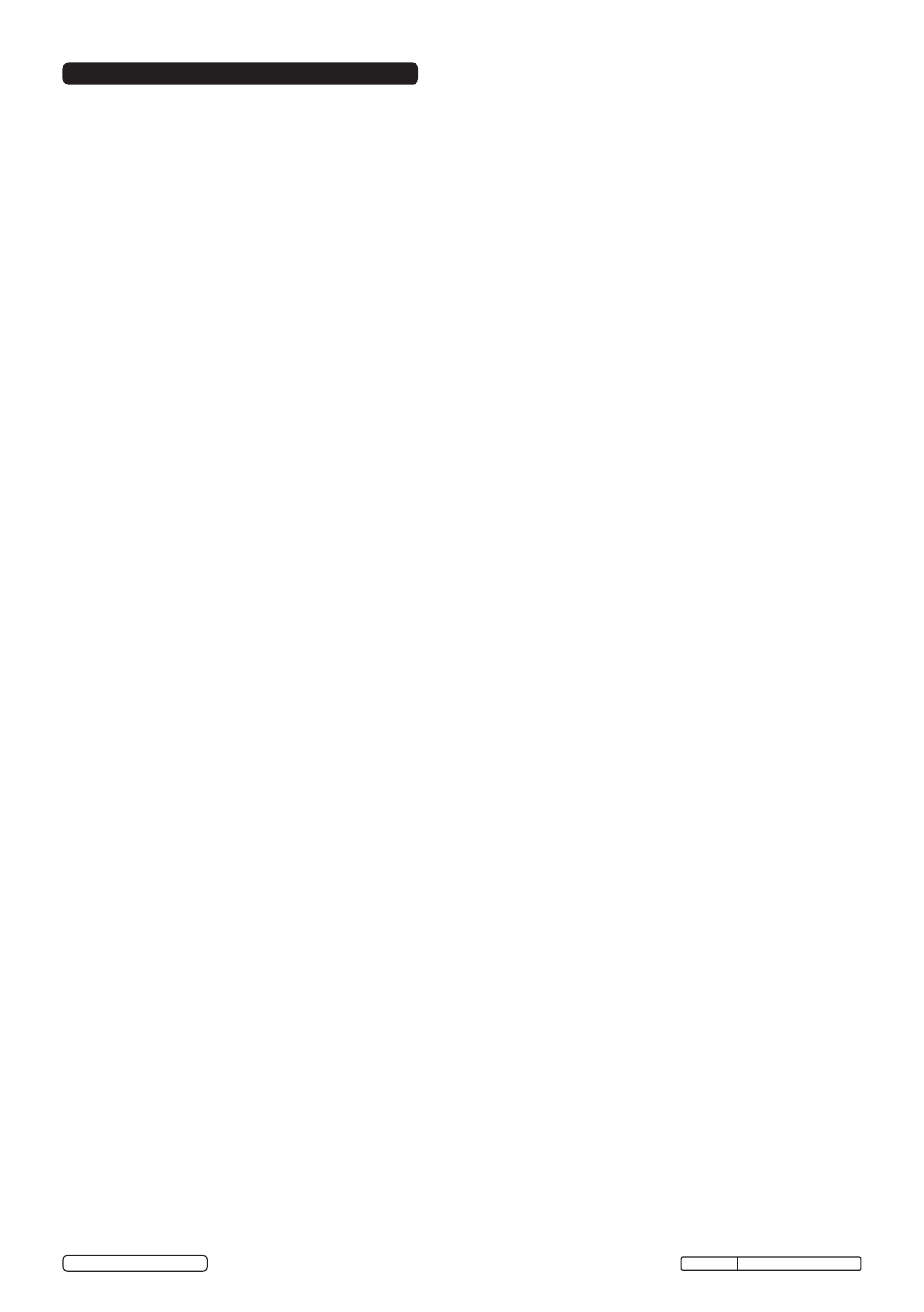
14.1 CALIBRATION METHODS (General Hints for Calibration).
There are four different methods available for calibration:
14.1.1
Basic calibration: recommended for measurement on even surfaces and if the measuring
object has the same material, size and curvature as the zero plate attached in the casing.
14.1.2
Zero-point calibration: recommended if measurment errors of up to ±3% of reading plus
constant error of probe, are permitted. (Example for constant of probe showing error: Fe 1um; no-Fe 1.5um)
14.1.3
One-point calibration (calibrating using a calibration foil): recommended if readings are
expected to be close to the calibration value and if the permitted error of the probe will be a maximum
of ±1%...3% of reading plus constant probe error.
14.1.4
Two-point calibration (using a set of two calibration foils):
a) Recommended for measurements on rough surfaces.
b) Recommended for precise measurements on smooth surfaces if the thickness to be expected lies
between that of the two calibration foils.
14.2 Storing Calibration Values
If the gauge is calibrated for a particular purpose, the calibration values will be stored in memory until
changed.
NOTE: The calibration procedure should be restarted from the beginning if
a) An incorrect reading has been taken.
b) An incorrect command has been entered.
c) The gauge has switched off.
14.3 Calibration Example
Calibration is the most important requirement for accurate measurement. The more closely the
calibration sample matches the product sample, the more accurate the calibration, and therefore the
more accurate the reading will be.
If for instance, a product is to be measured on a steel cylinder, quality ST37(mild steel), diameter 6mm,
the calibration of the uncoated sample must take place on a steel cylinder of similar quality with the
same diameter. The calibration sample must correspond to the product sample in the following ways:
a) Curvature radius
b) Substrate material properties
c) Substrate thickness
d) Size of measuring area
e) The point at which the calibration is made on the calibration sample must always be identical with
the point of measurement on the product itself, especially in the case of corners and edges of small
parts.
14.4 High-Accuracy Calibration
To achieve high-accuracy readings, it is advisable to log calibration values (both zero values and
calibration foil values) several times in succession. In this way, the gauge will automatically establish
a mean calibration value. For more details see 14.6 'Special hints for calibration'. The high-accuracy
calibration is an obvious advantage when calibrating on uneven, e.g. shot-blasted, surfaces.
14.5 Cleaning the Measuring Point
Before calibration of the measuring point, the probe tip must be free from grease, oil, scraps of metal,
etc. The slightest impurity will affect measurement and distort readings.
14.6 Special Hints for Calibration
The basic calibration stored in the gauge should only be used for measurements on even surfaces,
i.e. on steel components made of conventional steel (mild steel) or on aluminium components.
Firstly, enter into Calibration Mode via the following 'path' (Menu - Calibration - Enable). Then the
LCD display will show “Cal n(or 1~2) Zero n(or y)”. The “n” means “not any point calibration and Zero
calibration, and “y” means “there is Zero calibration”. “Cal 1~2” means” There is One or Two point
Calibration”. After finishing all Calibration tasks, we advise that you disable calibration via the MENU
system.
14. CALIBRATION & MEASUREMENT
Original Language Version
TA090 Issue No.1 25/10/12
© Jack Sealey Limited