7 coor dinat e t ransf or mation cy cles – HEIDENHAIN TNC 620 (340 56x-01) User Manual
Page 356
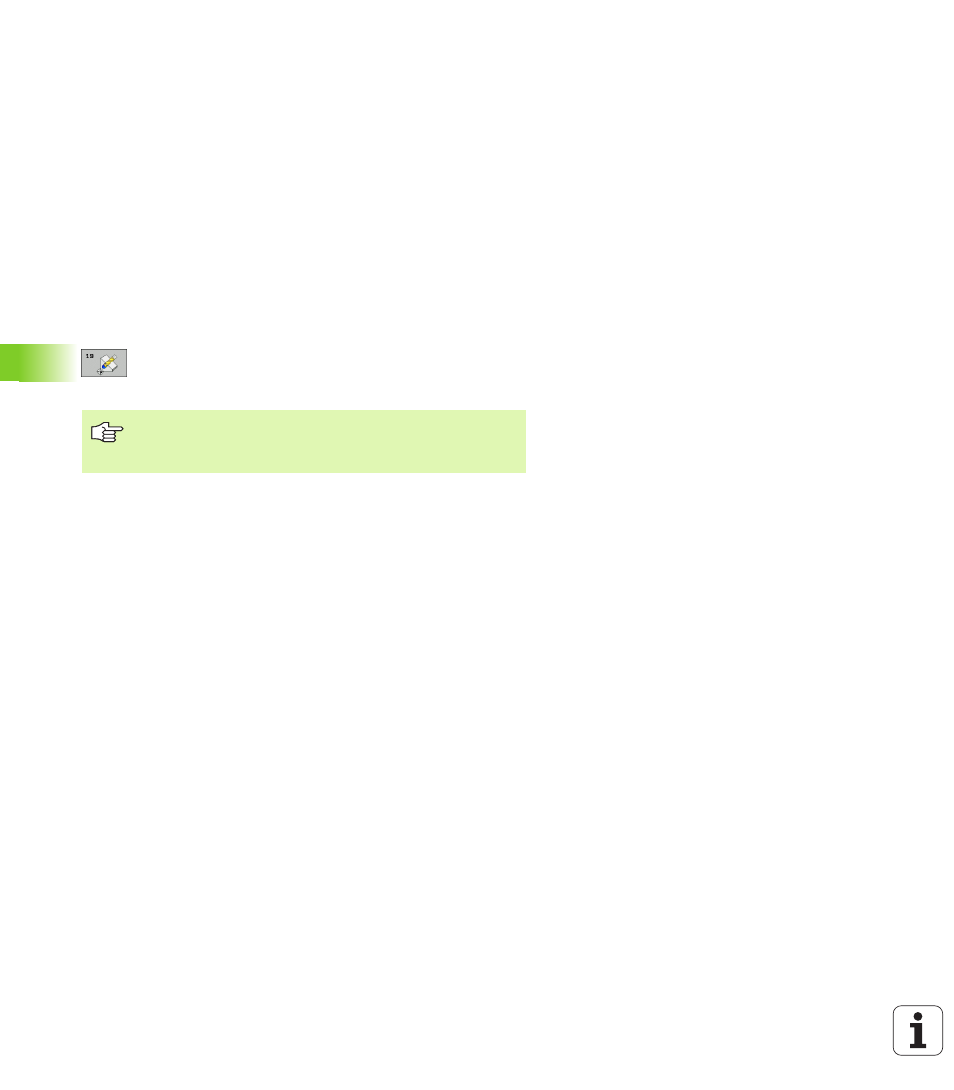
356
8.7 Coor
dinat
e
T
ransf
or
mation Cy
cles
If you program the position of the working plane via spatial angles, the
TNC will calculate the required angle positions of the tilted axes
automatically and will store these in the parameters Q120 (A axis) to
Q122 (C axis). If two solutions are possible, the TNC will choose the
shorter path from the zero position of the rotary axes.
The axes are always rotated in the same sequence for calculating the
tilt of the plane: The TNC first rotates the A axis, then the B axis, and
finally the C axis.
Cycle 19 becomes effective as soon as it is defined in the program. As
soon as you move an axis in the tilted system, the compensation for
this specific axis is activated. You must move all axes to activate
compensation for all axes.
If you set the function Tilting program run to Active in the Manual
Operation mode (see “Tilting the Working Plane (Software Option 1),”
page 62), the angular value entered in this menu is overwritten by
Cycle 19 WORKING PLANE.
Tilt axis and tilt angle?:
Enter the axes of rotation
together with the associated tilt angles. The rotary
axes A, B and C are programmed using soft keys.
If the TNC automatically positions the rotary axes, you can enter the
following parameters:
Feed rate ? F=:
Traverse speed of the rotary axis
during automatic positioning.
Set-up clearance?
(incremental value): The TNC
positions the tilting head so that the position that
results from the extension of the tool by the set-up
clearance does not change relative to the workpiece.
Because nonprogrammed rotary axis values are
interpreted as unchanged, you should always define all
three spatial angles, even if one or more angles are at zero.