Flowserve VTP Wet Pit User Manual
Page 52
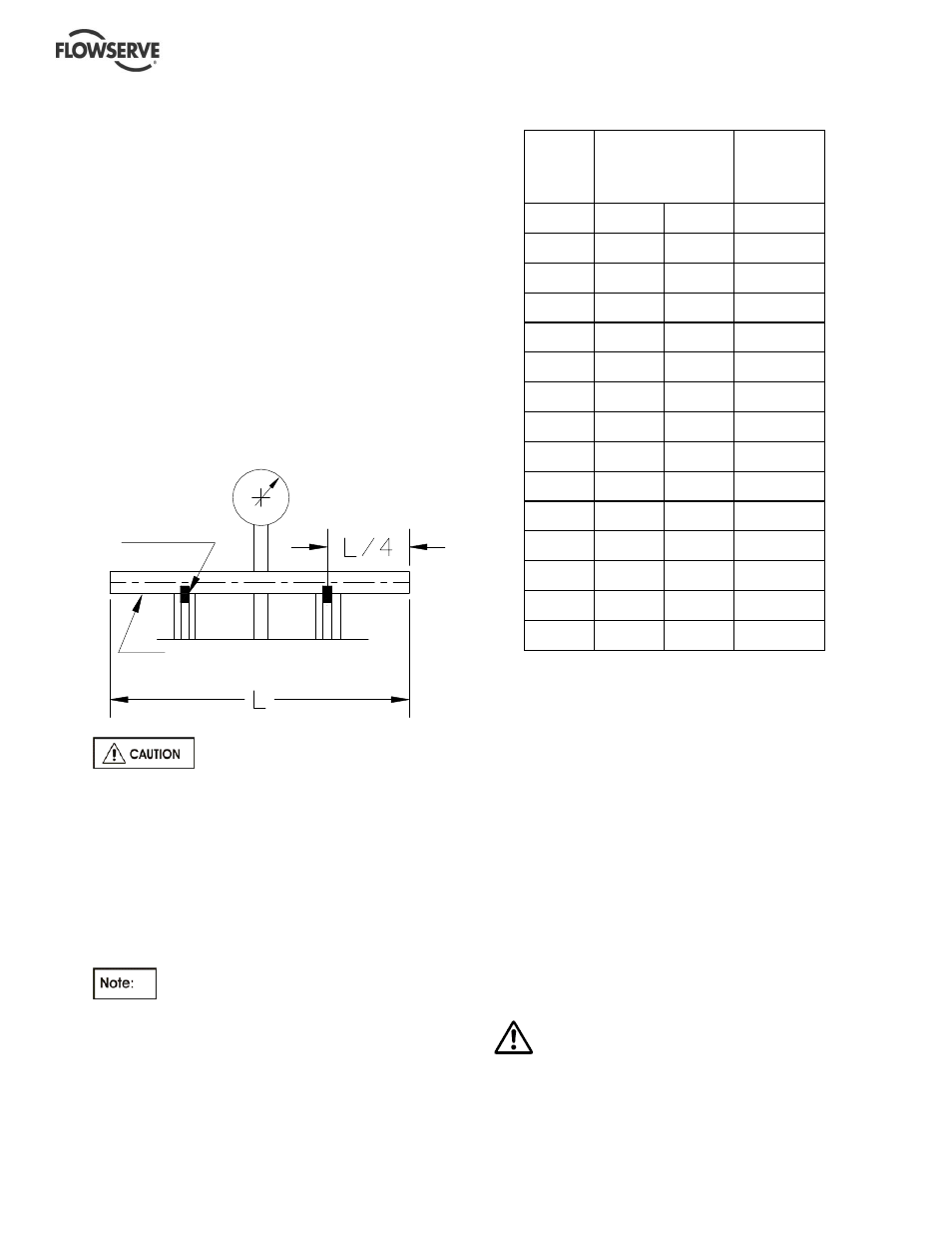
VERTICAL TURBINE PUMPS (VTPS) CENTRIFUGAL PUMPS ENGLISH 71569224
– 10-13
Page 52 of 76
flowserve.com
Examination of shaft/s
6.9.1
Check the shafts for straightness, pitting and wear.
Remove all burrs or nicks. Shaft damage is usually
best corrected by replacing the shaft.
The shaft must be straight to within 0.127 mm
(0.005 in.) total indicator reading. The detail below
shows the recommended method for checking shaft
straightness. If the shaft is not straight, it must be
straightened or replaced. If the deflection is gradual
over a considerable length, the shaft can usually be
straightened by supporting on two blocks straddling
the crooked section and applying pressure to the high
side to deflect the shaft in the opposite direction. If the
shaft has a sharp crook (dog-leg), it is recommended
that the shaft be replaced since the shaft will not
always remain straight, even if satisfactorily
straightened.
Even if the shaft is new or has been
previously straightened, it is recommended that the
shaft be re-checked at this point to ensure damage
has not occurred in transit or handling.
Examination of bearings
6.9.2
Check all bearings for total clearance over the shaft.
It is recommended that all bearings indicating visual
wear be replaced. In addition, any bearings whose
running clearance exceeds "As New" tolerances by
more than 50% should be replaced (see table 6.8.2.1).
Rubber bearings should always be replaced
when servicing a pump.
Shaft/bearing clearance
6.9.2.1
Shaft
Size
mm
(in.)
Shaft
Diameter/Tolerance
Min Dia- Max Dia
mm
(in.)
Bearing
Clearance
(Max/Min)
mm
(in.)
25.40
(1.000)
25.35
(0.998)
25.40
(1.000)
0.28/0.13
(0.011/0.005)
31.75
(1.250)
31.70
(1.248)
31.75
(1.250)
0.35/0.15
(0.012/0.006)
38.10
(1.500)
38.05
(1.498)
38.10
(1.500)
0.33/0.18
(0.013/0.007)
42.86
(1.690)
42.81
(1.685)
42.86
(1.687)
0.36/0.18
(0.014/0.007)
49.21
(1.940)
49.16
(1.935)
49.21
(1.937)
0.38/0.23
(0.015/0.008)
55.56
(2.190)
55.51
(2.185)
55.56
(2.187)
0.41/0.23
(0.016/0.009)
61.91
(2.440)
61.86
(2.435)
61.91
(2.437)
0.41/0.23
(0.016/0.009)
68.26
(2.690)
68.21
(2.685)
68.26
(2.687)
0.43/0.23
(0.017/0.009)
74.61
(2.940)
74.56
(2.935)
74.61
(2.937)
0.43/0.23
(0.017/0.009)
82.55
(3.250)
82.47
(3.247)
82.55
(3.250)
0.46/0.25
(0.018/0.010)
88.90
(3.500)
88.82
(3.497)
88.90
(3.500)
0.48/0.28
(0.019/0.011)
95.25
(3.750)
95.17
(3.747)
95.25
(3.750)
0.53/0.35
(0.021/0.012)
101.60
(4.000)
101.58
(3.997)
101.60
(4.000)
0.56/0.33
(0.022/0.013)
114.30
(4.500)
114.22
(4.497)
114.30
(4.500)
0.58/0.35
(0.023/0.014)
127.00
(5.000)
126.92
(4.997)
127.00
(5.000)
0.61/0.38
(0.024/0.015)
Bronze, epoxy, carbon and hard-backed rubber
bearings are pressed into their respective bores. They
can either be pressed out or machined on the inside
diameter until the wall is thin enough to collapse.
Some rubber bearings are the snap-in or glue-in type.
These can be removed by prying inward on the
outside of the bearing to collapse it.
If the bearing bore of the housing is heavily scarred or
corroded, the part should be replaced or reworked to
provide a true bore for the bearing.
Replacement bearings are designed to be pressed
into housings so bores will shrink to "as new"
tolerances. Measure the bore of bearings after
pressing and ream as necessary to assure "as new"
tolerances.
Inspection of bowl assembly
6.9.3
When repairing a bowl assembly that has
been in service for several years, the physical
condition or strength of all parts such as cap screws,
bowls and bowl threads must be carefully checked.
ROLLERS
DIAL INDICATOR
SHAFT