Impeller adjustment 5.3 – Flowserve VTP Wet Pit User Manual
Page 38
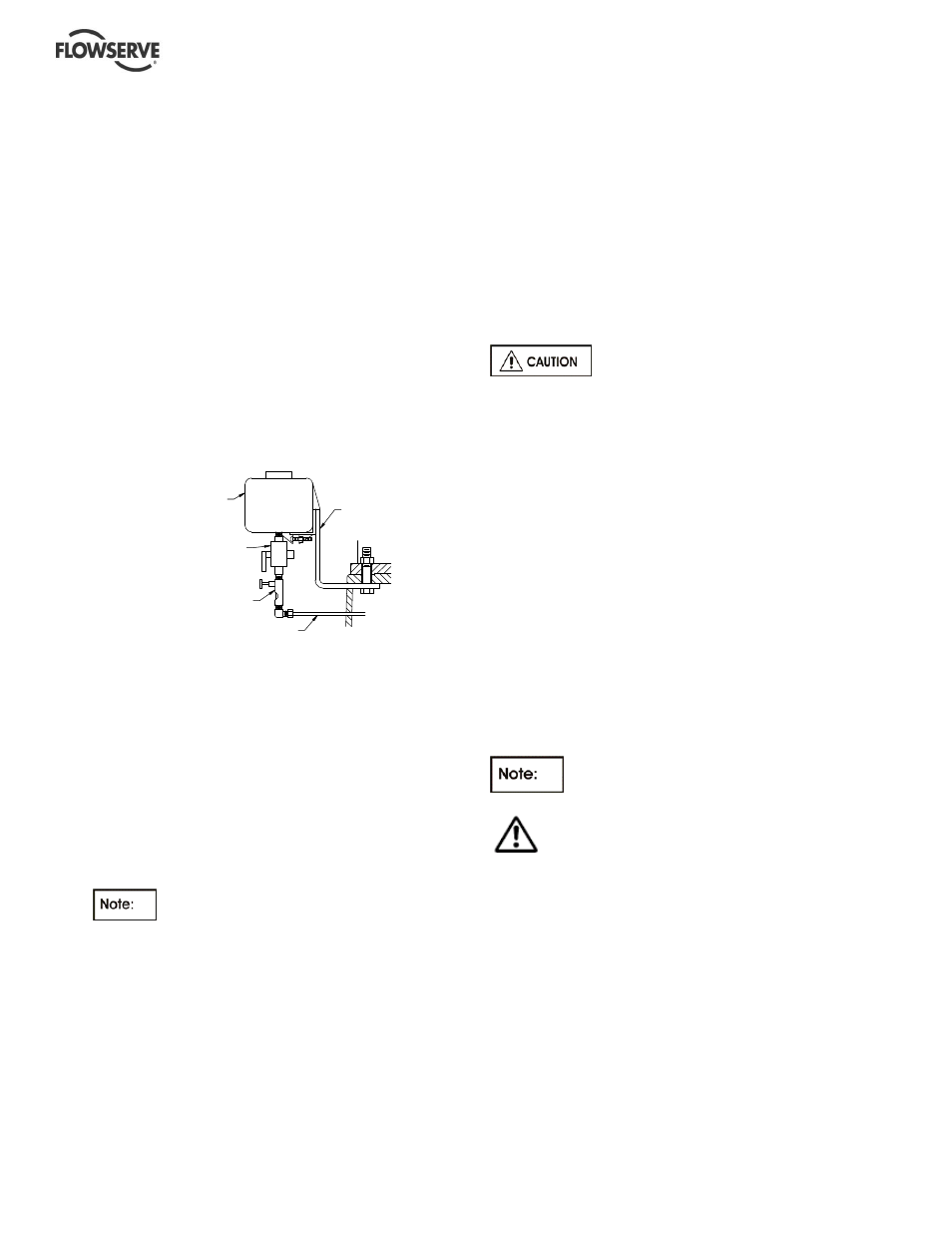
VERTICAL TURBINE PUMPS (VTPS) CENTRIFUGAL PUMPS ENGLISH 71569224
– 10-13
Page 38 of 76
flowserve.com
Enclosed shaft lubrication
5.2.2
VTPs with the enclosed shafting are lubricated by a
dedicated oil supply system or injection lubricated by
extraneous liquid; usually clean water to meet the
application requirements.
Oil lubricated pumps
5.2.2.1
The lubricating oil must be available and should be
allowed to run into the enclosing tube in sufficient
quantity to thoroughly lubricate all lineshaft bearings.
The gravity flow system is the most commonly
utilized system for oil.
The oil reservoir (example shown in detail below)
must be kept filled with a good quality light turbine oil
(about 30 cSt) at the operating temperature and
adjusted to feed a minimum of 3 drops per minute
per 30 m (100 ft) of column length, at never less than
5 drops per minute total.
Pre-lubrication of oil lubricated pumps
5.2.2.2
As a general rule, the oil must be allowed to flow by
gravity at least 45 minutes before the pump is started
for the first time or in case the pump was turned off
for a longer duration. Adequate care should be taken
to make sure that the flow is available and is
consistent for subsequent startups.
Injection lubricated pumps
5.2.2.3
Enclosed lineshaft bearings are lubricated by
extraneous liquid (usually clean water), which is fed
to the tension nut either by gravity flow, or by a
pressure injection system.
Injection systems are designed for each
installation. Injection pressure and quantity of liquid
will vary. Normally 0.45-0.90 m
3
/h (2-4 gpm) at 0.7-
1.4 bar (10-20 psi) over maximum pump discharge
pressure of clean liquid is required.
Pre-lubrication of injection lubricated
5.2.2.4
pumps
As a general rule, the liquid flow is to be started at
least 15~20 minutes before the pump is started for
the first time or in the event of pump not being in use
for longer duration.
The injected lubricant flow is never stopped for short
‘off ’ periods. Adequate care should be taken to
make sure that the flow is available and consistent
for subsequent startups and operation. Injection
pressure to be adjusted as recommended before the
startup.
Enclosed shaft lubricants
5.2.3
The following oils are recommended for enclosed
lineshaft bearing lubrication under normal operating
conditions. See tables 5.2.3.1 and 5.2.3.2.
It is recommended that detergent type
oils not be used.
Non-food/food grade lubricant oils
5.2.3.1
Equivalent turbine oil (food or non-food grades as
required) with the matching properties has to be
selected. Oils with a viscosity range of 30 cSt
(mm
2
/sec) to 37 cSt (mm
2
/sec) at 40
C (100 F) with a
minimum viscosity index of 90 are recommended.
The pour point of the oil must be in accordance with
the lowest expected temperature of the bearing
housing during a stop of the pump.
Oil level
5.2.4
The correct oil level is in the middle of the oil sight
glass and shall be checked when the pump is not in
operation. Periodically check if the lubricating oil is
mixed with any condensed water. Careful opening of
the oil drain during a stop of the pump will show any
water.
After the initial start the level will decrease
due to circulation of the oil through the bearings.
If the oil level is higher than specified, it could
result in higher bearing temperatures resulting in
poor lubrication.
Impeller Adjustment
5.3
Proper impeller adjustment positions the impeller
inside the bowl assembly for maximum performance.
The impellers must be raised slightly to prevent them
from dragging on the bowls, but not raised too high so
as to adversely affect hydraulic performance.
The impeller must be down against the bowl seat
when starting impeller adjustment. When pumps are
subjected to suction pressure, the pressure acting
against the shaft tends to raise it. Make sure the shaft
is down when starting to adjust the impellers.
(77) LUBRICANT TANK
(341) SHUT OFF VALVE
(79) TANK BRACKET
(342) FLOW REGULATION
VALVE
(344) LUBRICANT SUPPLY