Flowserve VTP Wet Pit User Manual
Page 44
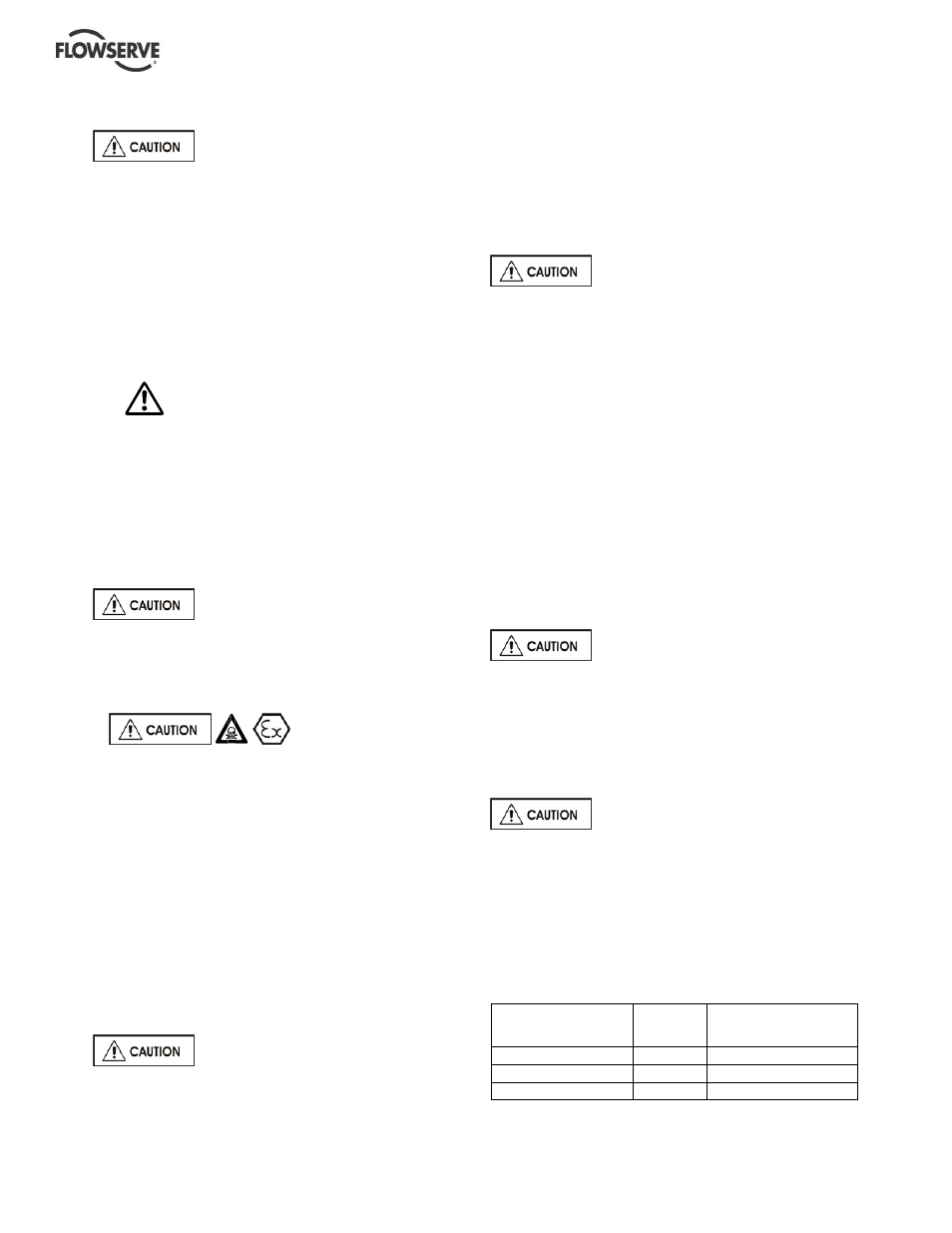
VERTICAL TURBINE PUMPS (VTPS) CENTRIFUGAL PUMPS ENGLISH 71569224
– 10-13
Page 44 of 76
flowserve.com
Initial Starting
5.7.5
Ensure flushing and/or cooling/
heating liquid supplies are turned ON before
starting the pump.
a) If the discharge line has a valve in it, partially
open the discharge valve closest to the pump.
The discharge valve is intended to add sufficient
system resistance to the pump. Failure to
maintain pump flow rates within the limits of the
pump and motor could result in severe damage.
b) OPEN all inlet valves.
c) Prime the pump & check lubrication system in
operation (check the liquid level).
d)
Ensure all vent connections are closed
before starting.
e) Check the motor connections.
f) Start pre-lubrication liquid flow on pump if
required.
g) Start the pump and observe the operation. If
there is any difficulty, excess noise or vibration,
stop the pump immediately and refer to the
Trouble Shooting Chart (section 7.0) to
determine the probable cause.
Do not run the pump with the outlet
valve closed for a period longer than 30 seconds.
h) Open vent connections and ensure that the unit
is vented of all trapped vapor before closing the
vents.
Observe
extreme
caution when venting and or draining hazardous
liquids. Wear protective clothing in the presence of
caustic, corrosive, volatile, flammable or hot liquids.
Do not breathe toxic vapors. Do not allow sparking,
flames or hot surfaces in the vicinity of the equipment.
i) Open the discharge valve as desired to operate
the unit at its design conditions.
j) Check complete pump and driver for leaks, loose
connections, or improper operation.
If possible, the pump should be left running for
approximately one half hour on the initial startup, this
will allow the bearings, packing or seals, and other
parts to "run-in" and reduce the possibility of trouble
on future starts.
If abrasives or debris are present,
upon startup, the pump should be allowed to run until
the pumpage is clean. Stopping the pump when
handling large amounts of abrasives (as is
sometimes present on initial starting) may lock the
pump and cause more damage than the pump is
allowed to continue operation.
Every effort should be made to keep abrasives out of
lines, sump, etc. so that abrasives will not enter the
pump.
In the case of product lubricated
bearings the source of product supply should be
checked against the order. There may be
requirements for an external clean supply, particular
supply pressure or the commencement of lubrication
supply before pump start-up.
Frequency of lubrication
5.7.6
The characteristics of the installation and severity of
service will determine the frequency of lubrication.
Lubricant and pump/motor bearing temperature
analysis is useful in optimizing lubricant change
intervals.
The motor bearing temperature limitations should be
considered for its lubrication requirements. Refer to
the driver manufacturer’s user instructions supplied
with the pump. If documents are not found contact
Flowserve.
Never mix greases containing different
bases, thickeners or additives.
Normal vibration levels, alarm and trip
5.7.7
Pumps generally fall under classification of rigid
support machines within the International Rotating
Machinery standard and maximum vibration levels
are based on those standards
Alarm and trip values for installed
pumps should be based on the actual measurements
(N) taken on the pump in a fully commissioned (new)
condition. Measuring vibration at regular intervals
and recording will help to track any deterioration in
pump or operating conditions. Measurements shall
be taken at the pump/motor interface.
Typical allowable field vibration values
5.7.7.1
for vertical turbines- sump or wet pit
types
Motor rating kW (hp)
Vibration
velocity-
unfiltered
Vibration
mm/sec (in./sec) rms
0.75-to 7.5 (1-10)
N
6.1 (0.24)
7.5 to 75 (10 -100)
N
6.1 (0.24)
75 to 750 (100 -1000)
N
6.1 (0.24)-7.1 (0.28)
N = Normal; Alarm = N X1.25; TRIP = N X 2.0.