Flowserve VTP Wet Pit User Manual
Page 21
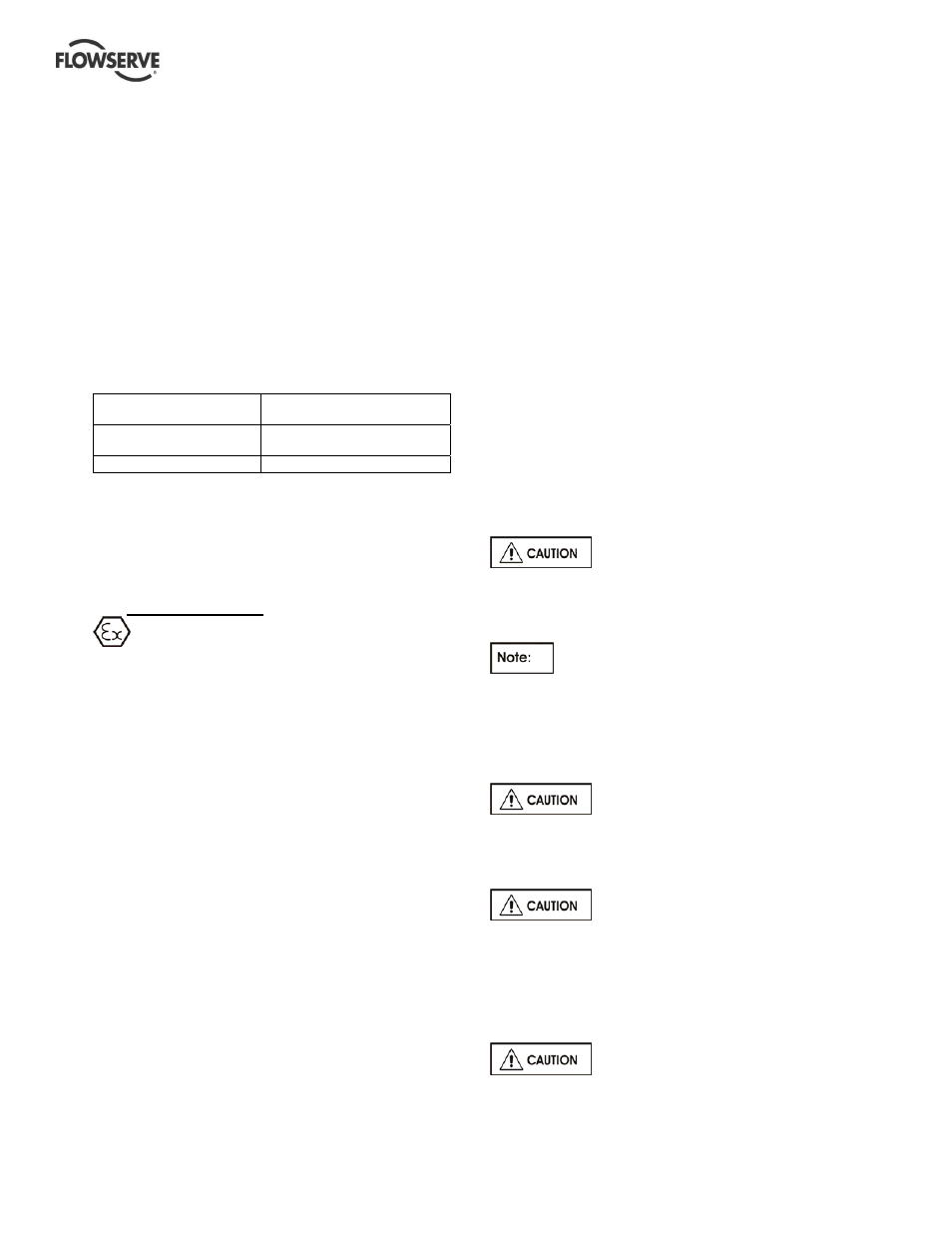
VERTICAL TURBINE PUMPS (VTPS) CENTRIFUGAL PUMPS ENGLISH 71569224
– 10-13
Page 21 of 76
flowserve.com
Accessories
3.3.8
Accessories may be fitted when specified by the
customer.
Performance and Operation Limits
3.4
This product has been selected to meet the
specifications of the purchase order. See section 1.5.
The following data is included as additional information to
help with the installation. It is typical and factors such as
temperature, materials and seal type may influence this
data. If required, a definitive statement for your particular
application can be obtained from Flowserve.
Operating limits
3.4.1
Pumped liquid temperature
limits*
5 ºC (40 ºF) to +80 ºC (176 ºF)
Maximum ambient
temperature*
Up to +40 ºC (104 ºF)
Maximum pump speed
refer to the nameplate
*Subject to written agreement from Flowserve.
Special designs and materials may be available for
pumps operating above and below these specified
limits. Contact Flowserve for upgrade options
available for your specific application.
4 INSTALLATION
Equipment operated in hazardous locations
must comply with the relevant explosion protection
regulations. See section 1.6.4, Products used in
potentially explosive atmospheres.
Location
4.1
When equipment has been in storage for greater than 6
months, a complete inspection should be conducted in
accordance with section 2.4.3. The pump should be
located to allow room for access, ventilation,
maintenance and inspection with ample headroom for
lifting and should be as close as practicable to the
supply of liquid to be pumped. Refer to the general
arrangement drawing for the pump set.
Inspection prior to installation
4.1.1
Six months prior to the scheduled installation date, a
Flowserve Pump Division representative is to be
employed to conduct an inspection of the equipment
and the facility. If any deterioration of equipment is
noticed, the Flowserve Pump Division representative
may require a partial or complete dismantling of the
equipment including restoration and replacement of
some components.
Preparation
4.2
The pump should be located to allow room for access,
ventilation, maintenance and inspection with ample
headroom for lifting and should be as close as
practicable to the supply of liquid to be pumped.
Refer to the general arrangement drawing for the pump
dimensions and details.
General installation check-list
4.2.1
The following checks should be made before starting
actual installation.
a) Make sure that motor nameplate ratings and the
power supply system match correctly.
b) Check the sump depth and pump length match-
up.
c) Check the liquid level in the sump.
d) Check the installation equipment to be sure that it
will safely handle the pump weight and size.
e) Check all pump connections (bolts, nuts etc) for
any shipping and handling related problems.
Always support shafting in at least
three places when lifting or installing. No installation
should be attempted without adequate equipment
necessary for a successful installation.
On hollow shaft drivers, check the clutch size
against the shaft size, which must go through the
clutch
On solid shaft drivers, check the motor shaft size
against the coupling bore size
Apply thread lubricant sparingly to
male shaft threads only at the time of making up
shaft connection. Excess lubricant should be
avoided.
Always check motor rotation before
connecting driver to pump. Reserve rotation due to
improper motor direction can cause extensive damage
to the pump.
Foundation/Anchor Bolts
4.3
There are many methods of installing
pump units to their foundations. The correct method
depends on the size of the pump unit, its location and
vibration limitations. Non-compliance with the