Altera Multiaxis Motor Control Board User Manual
Multiaxis motor control board, Features
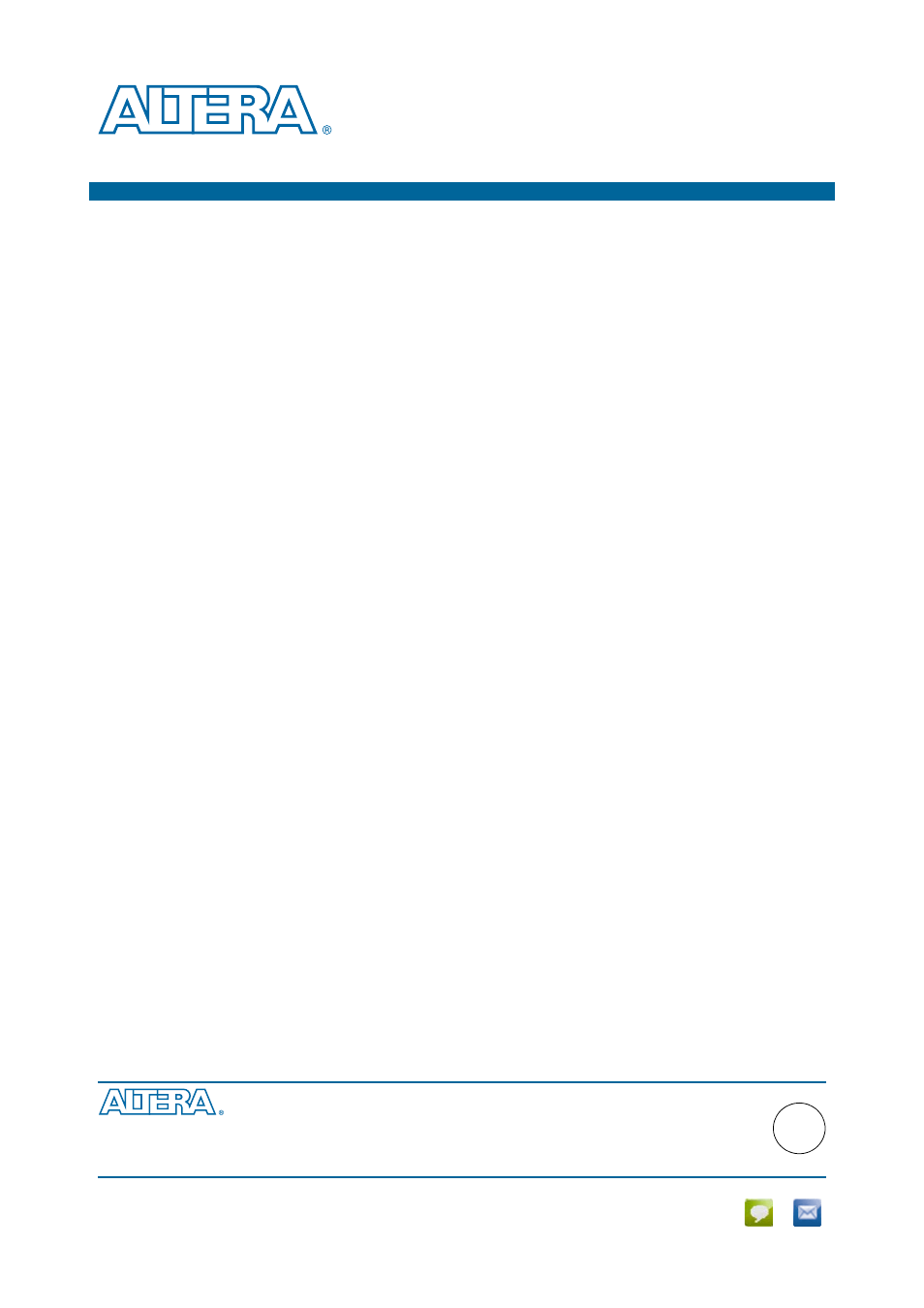
February 2014
Altera Corporation
MNL-1073
Reference Manual
© 2014 Altera Corporation. All rights reserved. ALTERA, ARRIA, CYCLONE, HARDCOPY, MAX, MEGACORE, NIOS,
QUARTUS and STRATIX words and logos are trademarks of Altera Corporation and registered in the U.S. Patent and Trademark
Office and in other countries. All other words and logos identified as trademarks or service marks are the property of their
respective holders as
products to current specifications in accordance with Altera's standard warranty, but reserves the right to make changes to any
products and services at any time without notice. Altera assumes no responsibility or liability arising out of the application or use
of any information, product, or service described herein except as expressly agreed to in writing by Altera. Altera customers are
advised to obtain the latest version of device specifications before relying on any published information and before placing orders
for products or services.
101 Innovation Drive
San Jose, CA 95134
Multiaxis Motor Control Board
This reference manual describes the Altera
®
Multiaxis Motor Control Board.
Efficient control of torque and speed of AC motors requires corresponding control of
voltage and frequency that you supply to the motor. Typically, you filter the AC input
voltage for electromagnetic interference (EMI), correct it to achieve unity power
factor, then rectify it to yield a DC voltage. You then invert the rectifier output again
through switching of power electronics, such as insulated-gate bipolar transistors
(IGBTs) to create the appropriate variable AC voltages and frequency for the motor.
Control algorithms such as Field Oriented Control (FOC) of PMSMs require you to
measure and analog to digitally A/D convert motor current and voltages, to provide
the required feedback to the controller. In addition, you use analog-to-digital
converters (ADCs ) to monitor the DC link voltage and current. Multiaxis drives
achieve either a high degree of coordination of control across motors or, in some
applications, integrate control of multiple independent motors to reduce overall
system cost. In closed-loop control systems, modern drive requirements continue to
evolve the need for higher precision position and velocity encoder feedback devices.
Standard encoder interfaces, 7such as EnDat, BiSS, and HiperFace, are based on
traditional sin and cosine encoder techniques. These encoder interfaces incorporate
communication controllers that can transmit information back to the drive digitally,
which enhances their performance in noisy environments. Encoder interfaces support
features, such as online inspection of motor parameters and line delay measurement,
which you can incorporate into the motor control algorithm.
The Multiaxis Motor Control Board contains all the power electronics, current and
voltage sensing, and connections for motor position feedback. You can use the motor
Control Board to develop a motor control system that supports permanent magnet
synchronous motors (PMSMs) or brushless DC (BLDC) motors. The Multiaxis Motor
Control Board is suitable for single-axis and multiaxis motor control applications and
supports multiple position feedback interfaces..
Features
The Multiaxis Motor Control Board has the following features:
■
Power factor correction (PFC) and EMI filter
■
DC link power supply of 400 V
■
Switch mode power supplies for logic
■
IGBT power stages
■
Sigma-delta ADCs for sensing voltages and currents
■
Brake (chopper) switch
Document Outline
- Multiaxis Motor Control Board
- Features
- Setting Up the Multiaxis Motor Control Board
- Functional Description
- References
- Document Revision History