Guide specifications (cont), Guide specifications, Cont) – Carrier 19 Series User Manual
Page 47
Attention! The text in this document has been recognized automatically. To view the original document, you can use the "Original mode".
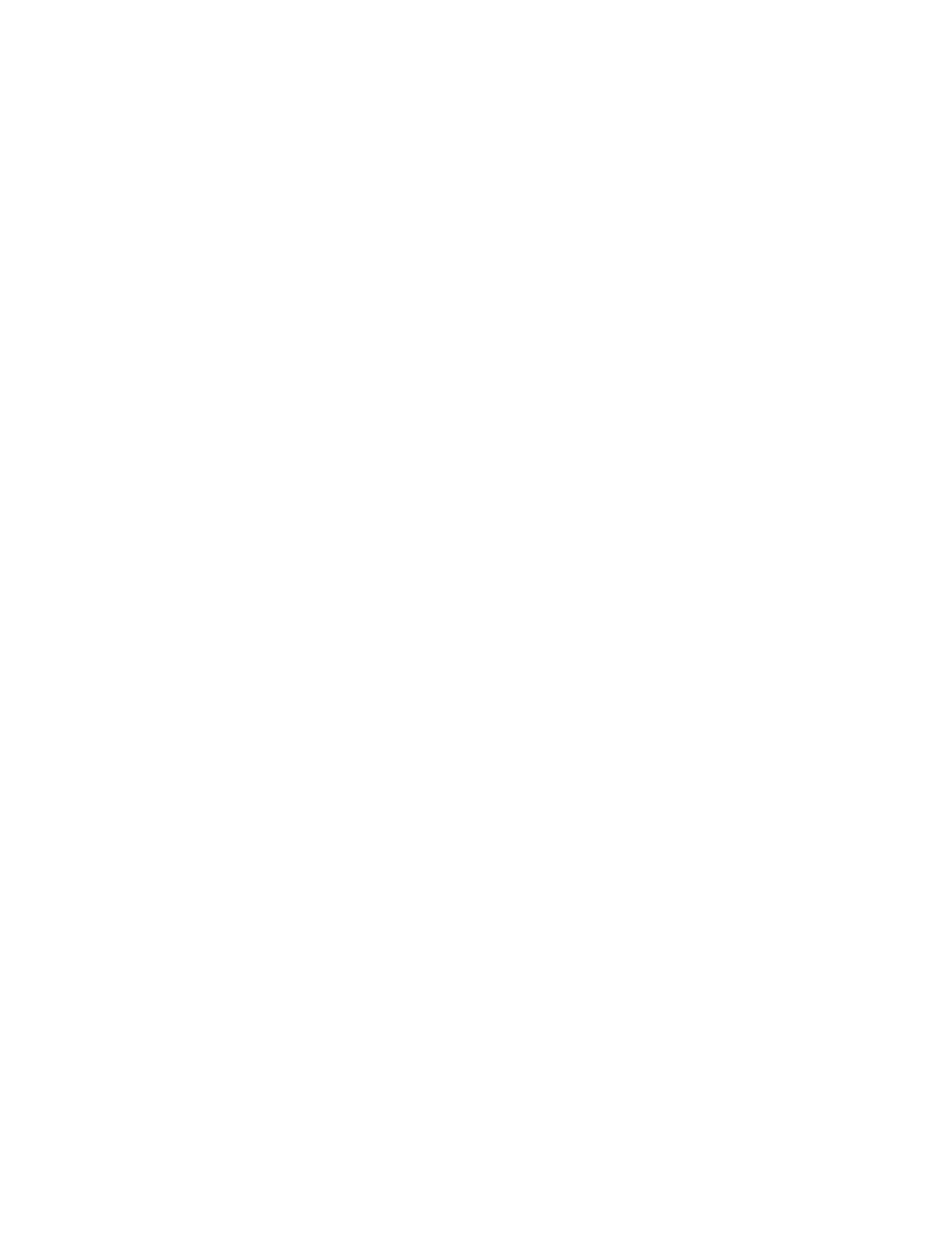
Guide specifications
(cont)
Controls shall be solid state, fully automatic and “fail-safe.”
Safety shutdown shall be provided for low refrigerant
temperature or pressure, bearing high temperature, high
refrigerant pressure, motor temperature and motor over
load. Each of the above controls shall have manual reset
flags. Recycle shutdown shall be provided for low oil
pressure and low chilled water temperature. These con
trols shall be automatic reset. Motor shall be protected
against drawing more than rated full load amperes. Motor-
driven elapsed running time meter shall be factory in
stalled on each machine. Solid state chilled water controller
shall be located within control panel and capable of
throttling range setting of 1.5 F. Pneumatic control with
automatic reset, which meets the 1.5 F throttling range
requirements, will be acceptable. If such pneumatic con
trol is used, the refrigeration machine manufacturer shall
furnish the chilled water controller and shall be responsible
for all required pneumatic work and any additional elec
trical work not shown on plans.
Each safety switch shall be wired across its own set of
terminals for easy isolation.
Demand limiter — Demand Limiter Device shall be pro
vided within the standard control panel so that maximum
current may be manually set to any fraction between 40%
and 100% of full load amperes. Limiters with 4-point settings
in the control panel are not acceptable.
Chiller shall be equipped with instrument gage and
control panel indicating condenser pressure, evaporator
pressure and oil pressure. Panel shall contain switches per
mitting manual or automatic operation of oil pump and
purge pump. In addition to gages, pilot lights and switches,
the panel shall contain evaporator low temperature or pres
sure cutout, condenser high pressure cutout, and differ
ential oil pressure controller interlocked so that compressor
will only operate if adequate oil pressure is maintained to
bearings. High pressure cutout and evaporator low tem
perature cutout shall be arranged in a lockout circuit
provided with reset buttons. Panel shall also operate the
capacity control mechanism to limit the load on compressor
motor to a safe maximum.
Purge system supplementing the instrument and control
panel shall be a self-contained purge system provided with
any necessary devices for evacuating air and water vapor
from the system and for condensing, separating and
returning refrigerant to the system. Compression type
purges are not acceptable as they are susceptible to leaks.
If city or other water piping is required for purge operation,
chiller manufacturer shall include same in his bid.
Refrigerant — If low-pressure (R-11) refrigerant is used,
machine shall be furnished with a factory-installed, wired
and piped purge unit suitable for removing noncondensible
gases and water which may enter the machine and for
reclaiming refrigerant. If high-pressure (R-12 or R-500)
refrigerant is used, machine shall come factory equipped
with a refrigerant storage vessel and pumpout compressor
(for multiple_____ may be used). Storage vessel shall be
external to the cooler and condenser and of sufficient
capacity that the entire charge may be transferred to the
vessel with 20% excess volume remaining in the vessel and
a pumpout compressor factory installed (for multiple
machine installations one pumpout may be used).
Refrigerant flow control shall be by means of a positive
metering device either float or pressure operated. The
chiller shall be capable of operating with entering con
densing water temperatures of 55 F. If a tower water
bypass valve is required to maintain a condensing pressure
head with 55 F entering water, the chiller manufacturer
shall include same in his bid.
Chiller manufacturer shall furnish magnetic motor
starters, Star-Delta closed transition type, with suitable
3-leg overloads. Starters shall be furnished with NEMA 1
enclosures for installation by the electrical contractor.
The disconnect, protection devices and control voltage
shall be provided by others.
Electrical — Electrical contractor shall furnish and install
all electrical lines, disconnect switches, circuit breakers,
auxiliary starters, and shall install the main starter and the
control wiring according to the diagram furnished by the
centrifugal refrigerating machine manufacturer.
Piping — Piping contractor shall make water connections
to the oil cooler, and such other water supply, drain and
vent connections as are required by the drawings and local
codes.
Initial refrigerant and oil charge shall be provided.
Water chiller unit performance data shall be submitted
for approval.
Nameplates — Chiller shall bear firmly attached metal
plates which state name of manufacturer, chiller unit
model number, compressor type and refrigerant used.
Operating and maintenance instructions prepared by
chiller manufacturer shall be included in Operating and
Maintenance Instructions herein before specified.
Start-up — Chillers shall be leak tested, refrigerant
pressure tested, evacuated, dehydrated, charged, started,
controls calibrated, and operating instructions given to
owner’s personnel by a factory trained service mechanic
employed by the chiller manufacturer. Start-up super
vision will not be acceptable.
The drawings are based on a Carrier machine. If another
manufacturer is substituted, that manufacturer shall be
responsible for all electrical, mechanical, structural or
architectural changes.
Equivalent material which qualifies to meet the above
specification will be acceptable. Manufacturers other than
Carrier, shall submit a 1/2-in. scale plan and section drawing
showing proper fit and clearance for tube pull, motor or
compressor removal, other maintenance clearances re
quired and rigging clearance needed within the mechanical
room.
Guarantee — All equipment furnished under this section
of the specifications shall be guaranteed against defective
workmanship and material for a period of one (1) year from
date of beneficial use to the owner or 18 months from time
of delivery whichever occurs first.
48