Guide specifications – Carrier 19 Series User Manual
Page 46
Attention! The text in this document has been recognized automatically. To view the original document, you can use the "Original mode".
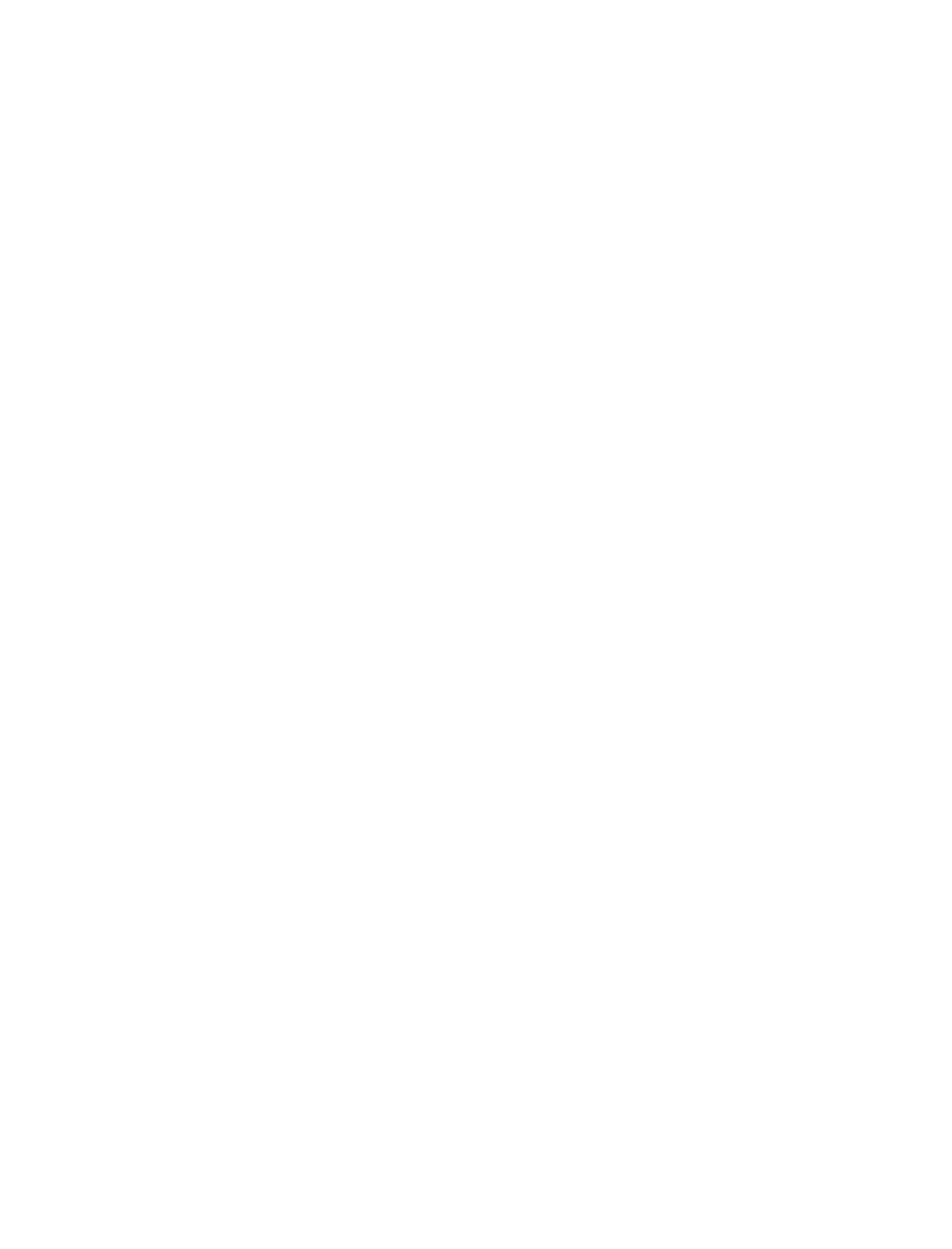
Guide specifications
Furnish and install — Hermetic centrifugal liquid chilling
package(s) suitable for chilling water as shown when sup
plied with condenser water and electric power as shown on
the plans.
Selection — Each unit shall allow for water side fouling
factor of .0005 in the cooler tubes and .0005 in the con
denser tubes. Cooler and condenser water pressure drops
shall not exceed those shown on plans. The kw power
draw shall not exceed that shown on plans. Machine shall
be rated in conformance with the most recent ARI Standard
550. Each unit shall conform to ANSI/ASHRAE 15-1978
Safety Codes.
Water chiller shall be complete with compressor and
motor, evaporator, condenser, lubrication system, capacity
control and controller, motor starter, instrument and
control panel mounted and factory wired on the machine,
purge system and other items as herein specified.
For capacities thru 1500 tons, the machine shall be
shipped completely factory assembled with all refrigerant
piping and control wiring factory installed. Models utilizing
R-12 and R-500 shall be shipped pre-charged. Machines
operating on R-11 and R-114 shall be charged at thejob site.
Compressor shall be of high performance single- or multi
stage hermetic design. Multi-stage designs shall include
interstage flash economizer for maximum cycle efficiency
and lowest operating cost. A thrust bearing of the Kingsbury
type with forced-feed lubrication shall axially position the
shaft under unidirectional thrust loading. To prevent
potential machine hazards, the impeller shall be designed so
that the thrust loading is positive and unidirectional under
all operating conditions.
Friction losses shall be maintained at a minimum by an
impeller design utilizing precision shaft placement. Impeller
shall be of an in-line design for even unloading and ease of
maintenance. Multi-stage compressors shall have dia
phragms between stages. Impellers shall be overspeed
tested a minimum of 20% above operating conditions.
Babbitt-lined journal bearings to be self-aligning type,
pressure lubricated. Compressor transmission gears must
be arranged for visual inspection without disassembly or
removal of compressor casing or impeller. The gears are to
be of the double-helical design, symmetrical and center
supported by a spherically seated, self-aligning bearing.
Compressor shall be capable of operation without surge,
cavitation or undue vibration from full load to 10% load
without hot gas bypass when supplied with design entering
water quantity.
Force-feed lubrication system with a hermetic motor
driven oil pump shall be furnished as part of the water
chiller. System shall be complete with oil pump, oil cooler,
pressure regulator, oil filters, thermostatically controlled
oil heater and necessary motor controls. Oil pumps shall
be energized prior to chiller motor energization. Oil pump
starter shall be factory supplied and mounted on the chiller
and factory wired with only field power leads required. (On
19DH and 19EB units only.) Should a substitute oil pump
[starter be offered that is not factory mounted, all required
extra field mounting and wiring is to be done at no cost to
the owner.
Oil
pump controls are to have delayed action so that oil
pressure is provided during machine coastdown. Oil pump
is to be provided with a separate 460-volt, 3-phase, 60-Hertz
power source. Oil pump shall have momentary switches to
permit only manual operation of pump when compressor is
not operating. When compressor is not operating, auto
matic operation modes are unacceptable since they are con
ducive to refrigerant absorption.
Motors shall be of the single-speed, non-reversing squirrel-
cage induction type, and shall be suitable for voltage as
shown on plans. The design speed shall be 3550 rpm. The
motor shall be suitable for operation in a refrigerant
atmosphere. Compressor motor to be cooled by atomized
subcooled refrigerant in contact with the motor windings.
Water jacket designs are not acceptable, as they produce
substantial temperature gradients throughout the motor
windings. Motor stator shall be arranged for service or
removal without complete compressor disassembly or
breaking of main refrigerant piping connections. Full-load
operation of the motor shall not exceed nameplate rating.
Motor shall be built for connection to Star Delta type
reduced voltage starter.
Evaporator and condenser shall be fabricated with
integrally-finned copper tubing rolled into the tube sheets
in both the evaporator and condenser as well as expanded
into the tube support sheets in the evaporator. Tubing shall
be finned except in the area adjacent to and in contact with
the tube and tube support sheets. Tube support sheets shall
be spaced at approximately 2-1/2 ft. intervals to maintain
proper tube spacing and to minimize tube vibration
and wear.
Tubes shall be removable from either end of the heat
exchanger without affecting strength and durability of
the tube sheet and without causing leakage at adjacent
tubes.
Water boxes are to be machine welded to the heat
exchanger tube sheet and to be equipped with tapped drain
and vent connections.
Machines using R-12 and R-500 shall be equipped with a
thermal economizer built into the condenser for increased
cycle efficiency.
Construction and materials for the heat exchangers shall
conform to ANSI B9.1 Safety Code for mechanical refrig
eration (which in turn requires conformance to the ASME
Code for Unfired Pressure Vessels where applicable).
Cooling tower bypass valve and associated piping are not
required for proper operation of the specified chiller at
design load. If a substitute chiller is supplied, it must be
capable of operating with condenser water temperatures
as low as 55 F without the need of cooling tower bypass.
Otherwise, a cooling tower bypass valve, bypass piping
and all associated controls must be supplied and installed
by the contractor at no cost to the owner. Working draw
ings pertaining to cooling tower bypass shall be prepared
by the contractor and submitted for approval.
Structural steel shipping skids shall be furnished with
each machine to facilitate transfer of machine from trans
porting conveyance to job site and to provide most effective
lifetime support for the machine. Substitute machines with
out these supports shall be properly supported by the
contractor at no cost to the owner. Vibration isolation
shall be provided in accordance with specifier’s
recommendations.
47