Controls, Control system – Carrier 19 Series User Manual
Page 43
Attention! The text in this document has been recognized automatically. To view the original document, you can use the "Original mode".
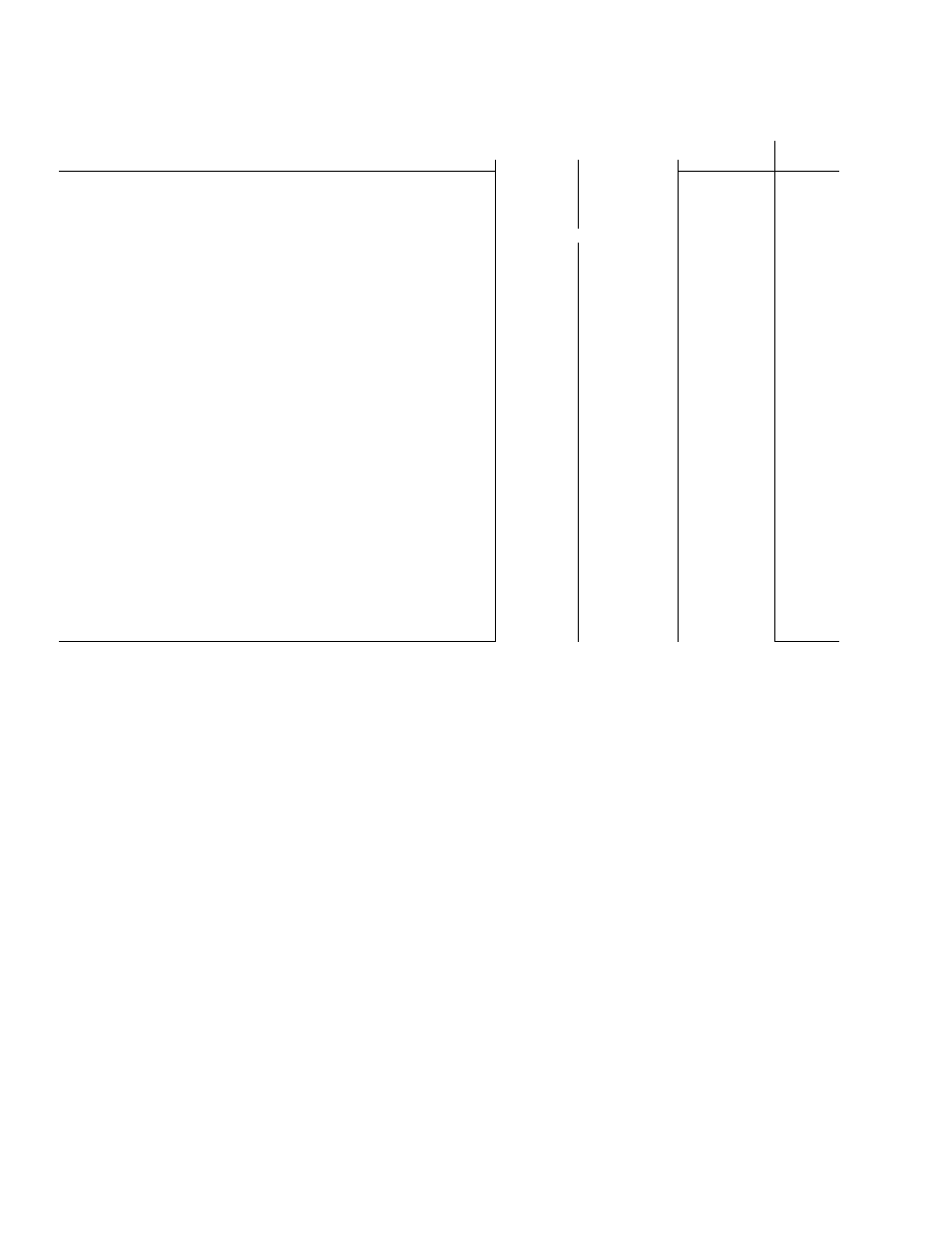
Controls
SAFETY AND CONTROL COMPONENT FEATURES
FEATURE
APPLIES TO THE
19DH
19EB
19FA
19CB
SAFETY CUTOUTS:
Bearing High Temperature
.
*
*
*
Motor High Temperature
*
*
*
♦
Gas Discharge High Temperature
—
*
*
—
Refrigerant High Pressure (Condenser)
*
*
*
*
Refrigerant Low Pressure (Cooler)
—
*
—
—
Refrigerant Low Temperature (Cooler)
*
—
*
y
Oil Pump Motor Overload
*
\/
Lube Oil Low Pressure
*
*•
*
*
Impeller Displacement Limit
—
*
*
Cooler and Condenser Water Flow Switches
/
y
\/
Y
INTERLOCKS:
Unloaded (Vanes Closed) Start
*
*
*
Pre-Lube and Post-Lube (via Program Timer)
*
*
*
*
Starting Sequence (via Program Timer)
*
*
*
*
Low Chilled Water Temp/Recycle Sequence (via Program Timer)
*
*
*
*
Oil Cooler Water Flow (Solenoid)
*
*
*
*
Machine Manual Reset after Safety Cutout
*
*
*
CAPACITY CONTROL:
Guide Vane Actuator
*
*
*
*
Solid State Leaving Chilled Water Control
*
*
*
*
Motor Current (demand) Limit — Adjustable 40-100%
*
*
*
*
Manual Leaving Chilled Water Reset
*
*
*
*
OTHERS:
Elapsed Time Indicator
*
*
*
*
Start Counter
*
*
*
—
Manual (Local) Start
*
*
*
Auto. (Remote) Start
#
#
#
#
Pneumatic Leaving Chilled Water Control
—
—
#
#
Pneumatic LCW Control Transducer
#
n
—
—
Safety Indicator panel
#
#
#
tl
Lead-Lag Panel
#
#
#
n
Mounted Oil Pump Starter
*
*
/
y
^Factory supplied and installed
/ Required — Field- and/or Factory-Option Supplied
#Optional
— Not applicable to this unit
Control system
The safety controls of each Carrier centrifugal chiller are
factory wired and mounted to ensure machine protection
against condenser high pressure, cooler low temperature,
bearing or motor overtemperature, motor overload and oil
low pressure. Other safety controls ensure no-load starting
of compressor and prevent compressor restart until a safe,
preset interval has elapsed.
The capacity control system is a fully automatic, modular,
solid state system for precise control of machine capacity
at all loads. When it is desirable to use pneumatic controls
to interface with a complete pneumatic system, control
interface devices or complete pneumatic control systems
are available.
The operating capacity of each chiller is matched directly
with the need for cooling. As cooling needs change, guide
vanes in the refrigerant vapor stream entering the com
pressor change position to maintain the selected chilled
water (brine) temperature.
The changes in vane position are initiated by a solid state
thermistor in the chilled water line. This probe constantly
relays any variations in water temperature to a solid state
capacity control module in the chiller control center. The
control module, in turn, amplifies and modulates the probe
signals. The amplified signals cause a guide vane actuator
motor to adjust the guide vane position as required.
If chilled water temperature drops below the selected
design temperature, the actuator moves the guide vanes
towards a closed position; the rate of refrigerant evap
oration slows and chiller capacity decreases. A rise in
chilled water temperature above the set point causes the
actuator to move the vanes towards a more open position.
Refrigerant begins to evaporate at a more rapid rate and
chiller capacity increases.
Built-in safeguards in the capacity control system
prevent motor overload. When motor full load current is
reached, the guide vanes stop opening immediately If
motor current continues to increase, the guide vanes begin
to close until motor current is reduced. To minimize start
up current demand, capacity control interlocks keep the
guide vanes in a closed (minimum capacity) position until
the compressor motor reaches run condition.
44