Lubrication – Carrier 50DL User Manual
Page 18
Attention! The text in this document has been recognized automatically. To view the original document, you can use the "Original mode".
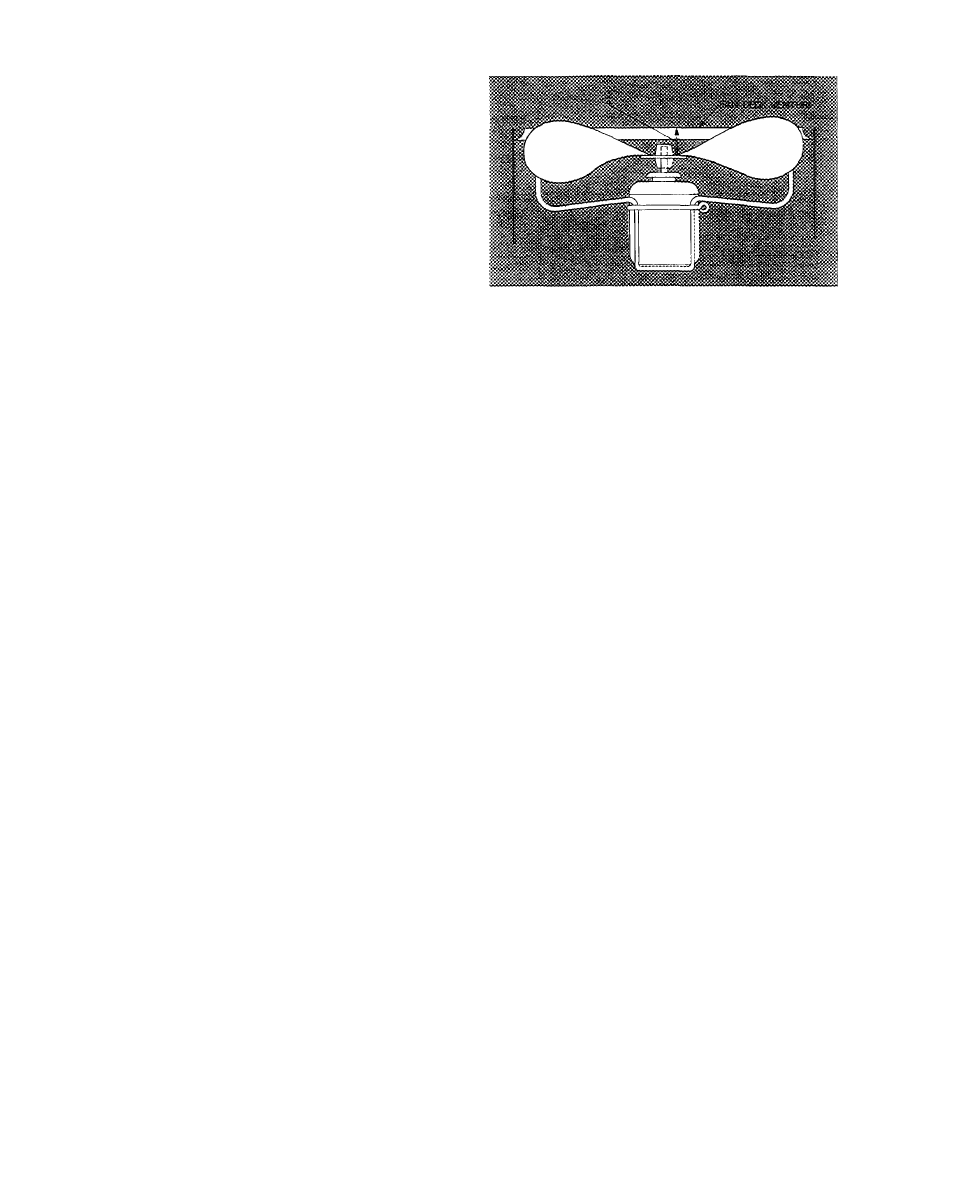
standard filters or 2-in. high-efficiency filters in bag
filter tracks.
OUTDOOR AIR INLET SCREEN(S) -- Clean
screens with steam or hot water and mild detergent.
Do not use throwaway filter in place of these
screens. Loosen fastening-bracket screws and slide
out screens.
Lubrication
COMPRESSORS — Each compressor is charged
with correct amount of oil at the factory. Oil level
should be between bottom and mid-level of sight
glass when compressor is warm. Refer to 06D or
06E Compressor Service Manual if additional infor
mation regarding compressor lubrication system
is required.
FAN SHAFT BEARINGS — Charge each grease
fitting with a suitable bearing grease at least once a
year. Do not overlubricate.
FAN MOTOR BEARINGS — No relubrication of
outdoor air fan motors is necessary for first 2 to 5
years of use, depending on operating conditions.
Annually thereafter, open, clean and repack each
bearing with a suitable bearing grease.
Indoor air fan motor bearings should be cleaned
and repacked with a suitable bearing grease
annually after initial unit installation.
Power Exhaust Air Fan Adjustment
(if fitted) —
Adjust belt tension so that 1/8-in. deflection at 5-to
8-pounds pressure between pulley centers can be
obtained. To change tension, loosen motor mount
ing bolts, reposition motor and tighten mounting
bolts. Tighten locknut and bolt under motor
mounting plate to secure in fixed position.
Outdoor (Condenser) Air Fan Adjustment
(Fig. 24) — Shut off unit power supply. Remove fan
guard and loosen fan hub setscrews. Adjust fan
height using a straight edge laid across venturi.
Tighten setscrews and replace rubber hubcap to
prevent hub from rusting to motor shaft. Fill hub
‘recess with permagum if hub has no rubber hubcap.
Damper Vent Position Setting
1. On constant volume units, adjust thermostat or
transmitter so there is no call for cooling. On
variable volume units, adjust set point knob on
microprocessor so there is no call for cooling.
The economizer dampers go to minimum
position.
2. Remove cap from vent adjustment screw on top
of damper motor terminal box cover.
3. Turn adjustment screw slowly until dampers
assume desired vent position. Do not manually
operate damper motor. Damage to motor will
result.
POWER FAILURE — Dampers have a spring re
turn. In the event of a loss of power, dampers close
until power is restored. Do not manually operate
damper motor. Damage to motor will result.
Fig. 24 — Outdoor Air Fan Adjustment
Refrigerant Charge
— Amount of refrigerant
charge is shown on unit nameplate and in Table 1.
When charging refrigerant system, refer to Carrier
Standard Service Techniques Manual, Chapter 1,
Refrigerants. When adding a complete charge,
evacuate the system using standard evacuating pro
cedures and weigh in specified amount of refrig
erant. A charging chart (Fig. 25, 26, and 27) is pro
vided on unit control box door above compressor
and may be used (use of sight glass not required).
When using refrigerant liquid line sight glass to
charge system:
1. Install a jumper on the low-pressure switch if
required.
2. Operate unit with restricted condenser airflow
to achieve an operating discharge pressure of
about 375 psig.
3. Slowly add refrigerant until sight glass clears.
4. Remove jumper from low-pressure switch and
remove condenser air restriction.
Indoor Air Fan Adjustment
— Fixed fan speeds
are set as shown in Table 1. If other than available
fan speeds are required, select field-supplied motor
or pulleys, using data from Tables 5 and 6, and
Fig. 28 and 29.
PULLEY REMOVAL — Pulleys are of the fixed
type and have taper-lock bushings. To remove, shut
off unit power. Loosen fan motor mounting plate
and remove belt. Relocate taper-lock bushing bolts
in removal holes to loosen bushing. Remove pulley
from shaft.
After reinstalling pulley and belt, check pulley
alignment and belt tension as described below.
PULLEY ALIGNMENT — Loosen fan shaft pulley
bushing and slide pulley along shaft. Make angular
adjustment by loosening motor mounting plate and
repositioning it as required.
BELT TENSION — Adjust belt tension by moving
motor back until only a slight bow appears in the
belts on the slack side of the drive while running
under full load. Secure motor. Recheck belt tension
after 24 hours of operation, adjust as necessary.
18