For example, A warning – Carrier WEATHERMAKER 8000 58WAV User Manual
Page 4
Attention! The text in this document has been recognized automatically. To view the original document, you can use the "Original mode".
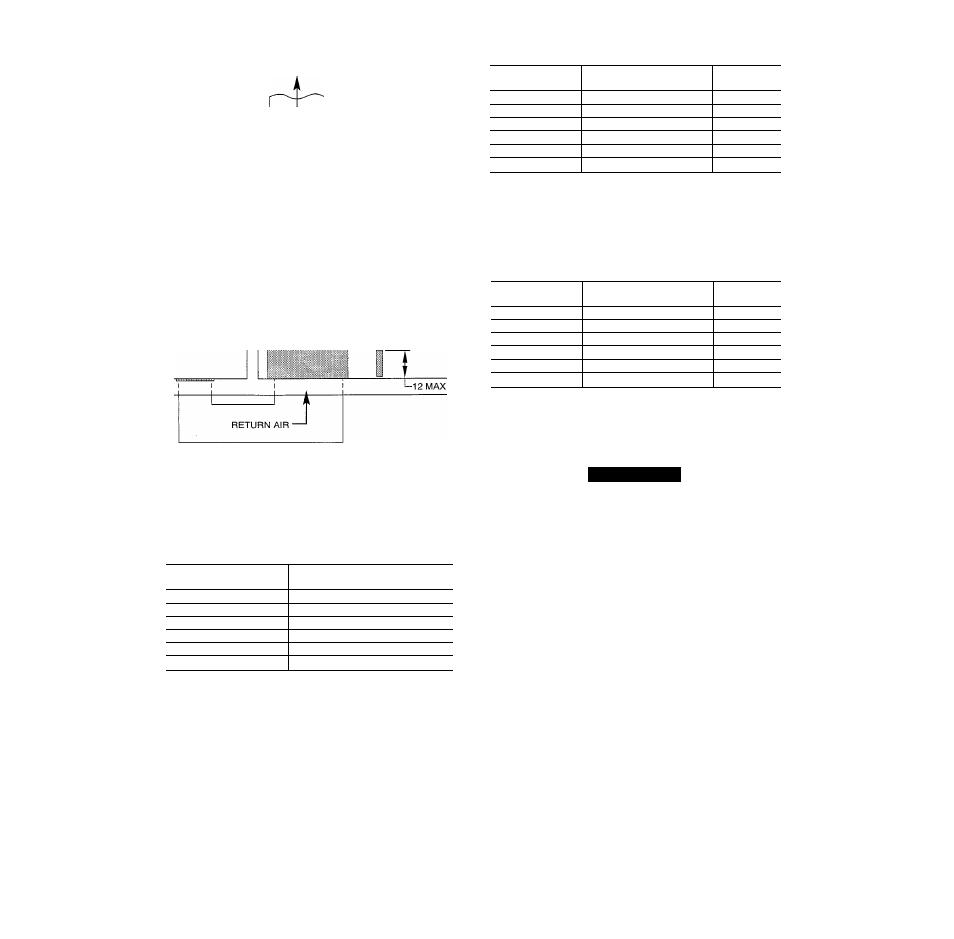
SUPPLY
AIR
For Example:
VENT THROUGH ROOF
(OATEGORY I) OR WALL
(CATEGORY III)
! I I
I I I
I
I I
_12 MAX
1 1 SO IN.
Ш
PER 1000
BTUH*
INTERIOR
HEATED
SPACE
6 IN. MIN
(FRONT) +
1 SO IN.
PER 1000
BTUH*
* Minimum opening size is 100 square in. with
minimum dimensions of 3 in.
+ Minimum of 3 in. when type-B vent is used.
A89012
Fig. 2—Air For Combustion and Ventilation
(Inside Air)
For Example:
58WAV FURNACE
INPUT BTUH
FREE AREA PER OPENING
(SQ IN.)
44,000
100
66,000
100
88,000
100
110,000
110
132,000
132
154,000
154
If the building is constructed unusually tight, a permanent opening
directly communicating with the outdoors should be provided.
This opening shall have a minimum free area of 1 sq in. per 5000
Btuh of total input rating for all equipment in the enclosure.
If the furnace is installed on a raised platform to provide a
return-air plenum, and return air is taken directly from the hallway
or space adjacent to the furnace, all air for combustion must come
from outdoors.
2. AJil air from outside the structure:
a. If combustion air is taken from outdoors through vertical
ducts, the openings and ducts MUST have at least 1 sq in.
of free area per 4000 Btuh of the total input for all
equipment within the confined space. (See Fig. 3.)
58WAV FURNACE
INPUT BTUH
FREE AREA PER OPENING
(SQ IN.)
ROUND PIPE
(IN. DIA)
44,000
11.0
4
66,000
16.5
5
88,000
22.0
6
110,000
27.5
6
132,000
33.0
7
154,000
38.5
7
b. If combustion air is taken from the outdoors through
horizontal ducts, the openings and ducts MUST have at
least 1 sq in. of free area per 2000 Btuh of the total input
for all equipment within the confined space.
For Example:
58WAV FURNACE
INPUT BTUH
FREE AREA PER OPENING
(SQ IN.)
ROUND PIPE
(IN. DIA)
44,000
22.0
6
66,000
33.0
7
88,000
44.0
8
110,000
55.0
9
132,000
66.0
10
154,000
77.0
10
When ducts are used, they must be of the same cross-sectional area
as the free area of the openings to which they connect. The
minimum dimension of rectangular ducts must not be less than 3
in. (See Fig. 3.)
A WARNING
Do not install the furnace on its back; safety control operation
will be adversely affected. Never connect return-air ducts to
the back of the furnace. A failure to follow this warning can
cause a fire, personal injury, or death.
Step 3—Filter Arrangement
The factory-supplied filter(s) is shipped in the blower compart
ment. Determine location for the filter and move filter retaining
hardware, if necessary, before attaching the return-air duct. After
the return-air duct has been connected to the furnace, install the
filter(s) inside the furnace blower compartment. See Fig. 4 for side
return application and Fig. 5 for bottom return application.
A bottom closure panel is factory installed in the bottom of the
furnace. When bottom return inlet is desired, remove and discard
the enclosure panel.
Filter retaining brackets, supports, and retainers are factory as
sembled and shipped installed for side return application, with 1
set of all required hardware on each of the furnace. (See Fig. 4.)
For bottom return applications, remove the brackets (front and
back) and supports from each side. The back bracket(s) are
installed in the rear of the furnace casing (dimples are provided to
mark mounting screw locations).
The front bracket(s) are installed on the bottom front plate as
shown in Fig. 5, once the bottom enclosure has been removed.
Rotate filter supports 180° so filter will rest on support, and
reinstall. (Do not reinstall in 17-1/2 in. casing.) Install the filter
retaining rod (small U-shaped end) in the rear bracket, and the
front of the filter retainer rod as shown in Fig. 5. Two sets of
hardware are needed for furnaces in 24-1/2 in. casings using 2
filters for bottom return. All hardware is provided for filter
installation.