Great Planes Extra 300S 40 Kit - GPMA0235 User Manual
Page 46
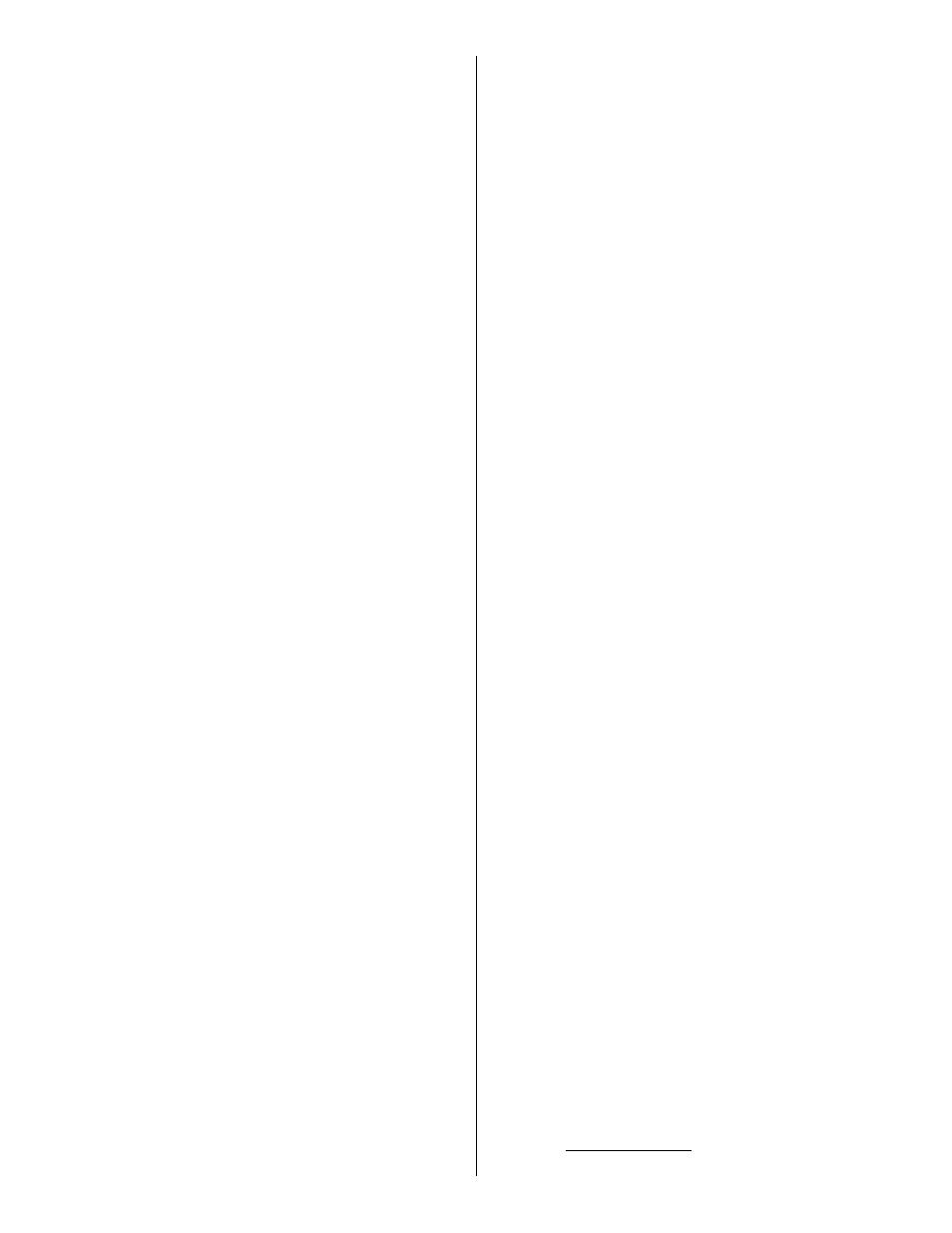
Let’s commence with the “engine thrust angle” on the chart. Note
that the observations you make can also be caused by the C.G., so
be prepared to change both to see which gives the desired result.
Set up a straight-and-level pass. The model should be almost
hands-off. Without touching any other control on the transmitter,
suddenly chop the throttle. Did the nose drop? When you add
power again, did the nose pitch up a bit? If so, you need some
downthrust, or nose weight. When the thrust is correct, the model
should continue along the same flight path for at least a dozen
plane lengths before gravity starts to naturally bring it down.
Do each maneuver several times, to make sure that you are
getting a proper diagnosis. Often, a gust, an accidental nudge on
the controls, or just a poor maneuver entry can mislead you. The
thrust adjustments are a real pain to make. On most models, it
means taking the engine out, adding shims, then reassembling
the whole thing. Don’t take shortcuts. Don’t try to proceed with
the other trim adjustments until you have the thrust line and/or
C.G. correct. They are the basis upon which all other trim setting
are made.
Also, while you have landed, take the time to crank the clevises until
the transmitter trims are at neutral. Don’t leave the airplane so that
the transmitter has some odd-ball combination of trim settings. One
bump of the transmitter and you have lost everything. The trim must
be repeatable, and the only sure way to do this is to always start
with the transmitter control trims at the middle.
The next maneuver is somewhat more tricky than it looks. To
verify the C.G., we roll the model up to a 45-degree bank, then
take our hands off the controls. The model should go a
reasonable distance with the fuse at an even keel. If the nose
pitches down, remove some nose weight, and the opposite if the
nose pitches up. The trick is to use only the ailerons to get the
model up at a 45-degree bank. We almost automatically start
feeding in elevator, but that’s a no-no. Do the bank in both
directions, just to make sure that you are getting an accurate
reading of the longitudinal balance.
We now want to test the correct alignment of both sides of the
elevator (even if they aren’t split, like a Pattern ship’s, they can still
be warped or twisted). Yaw and lateral balance will also come into
play here, so be patient and eliminate the variables, one-by-one.
The maneuver is a simple loop, but it must be entered with the
wings perfectly level. Position the maneuver so that your assistant
can observe it end-on. Always loop into the wind. Do several
loops, and see if the same symptom persists. Note if the model
loses heading on the front or back side of the loop. If you lose it
on the way up, it’s probably an aileron problem, while a loss of
heading on the way back down is most likely a rudder situation.
After you get the inside loops going correctly, do the same
maneuver to the outside, entering from an inverted position.
Before you make too many dramatic changes, glance at the
remainder of the chart and note the myriad combination of things
we can do just with the ailerons. Each change you make will affect
all other variables!
Note that the Yaw test is the same looping sequences. Here,
however, we are altering rudder and ailerons, instead of the
elevator halves. We must repeat that many airplanes just will not
achieve adequate lateral trim without sealing the hinge gaps shut.
The larger you make the loops (to a point), the more discernable
the errors will be.
The Lateral Balance test has us pulling those loops very tightly.
Actually, we prefer the Hammerhead as a better test for a heavy
wing. Pull straight up into a vertical and watch which wing drops.
A true vertical is hard to do, so make sure that your assistant is
observing from another vantage point. Note that the engine
torque will affect the vertical fall off, as will rudder errors. Even
though we balance the wing statically before leaving for the field,
we are now trimming it dynamically.
The Aileron Coupling (or rigging) is also tested by doing
Hammerheads. This time, however, we want to observe the side
view of the model. Does the plane want to tuck under a bit? If so,
then try trimming the ailerons down a small bit, so that they will
act as flaps. If the model tends to want to go over into a loop, then
rig both ailerons up a few turns on the clevises. Note that
drooping the ailerons will tend to cancel any washout you have in
the wing. On some models, the lack of washout can lead to some
nasty characteristics at low speeds.
The effects noted with the Aileron Coupling tests can also be
caused by an improperly set wing incidence. The better test for
this is knife-edge flight . . . If the model tends to pull upward, i.e., it
swings toward a nose up direction, then reduce the wing
incidence. If the model tries to go off heading toward the bottom
side of the plane, then increase incidence.
Again, we reiterate that all of these controls are interactive. When
you change the wing incidence, it will influence the way the
elevator trim is at a given C.G. Re-trimming the wing will also
change the rigging on the ailerons, in effect, and they may have to
be readjusted accordingly.
The whole process isn’t hard. As a matter of fact it’s rather fun —
but very time consuming. It’s amazing what you will learn about
why a plane flies the way it does, and you’ll be a better pilot for it.
One thing we almost guarantee, is that your planes will be more
reliable and predictable when they are properly trimmed out. They
will fly more efficiently, and be less prone to doing radical and
surprising things. Your contest scores should improve, too.
We wish to acknowledge the Orlando, Florida, club newsletter,
from which the basics of the chart presented here were gleaned.
Reprinted in part by Great Planes Model Manufacturing Company,
courtesy of Scale R/C Modeler magazine, Pat Potega, Editor,
August 1983 issue.
46