9. circuit analysis, 11. digital section, 16. analog section – Fluke 2180A User Manual
Page 26: Circuit analysis -2, Digital section -2, Analog section -2
Attention! The text in this document has been recognized automatically. To view the original document, you can use the "Original mode".
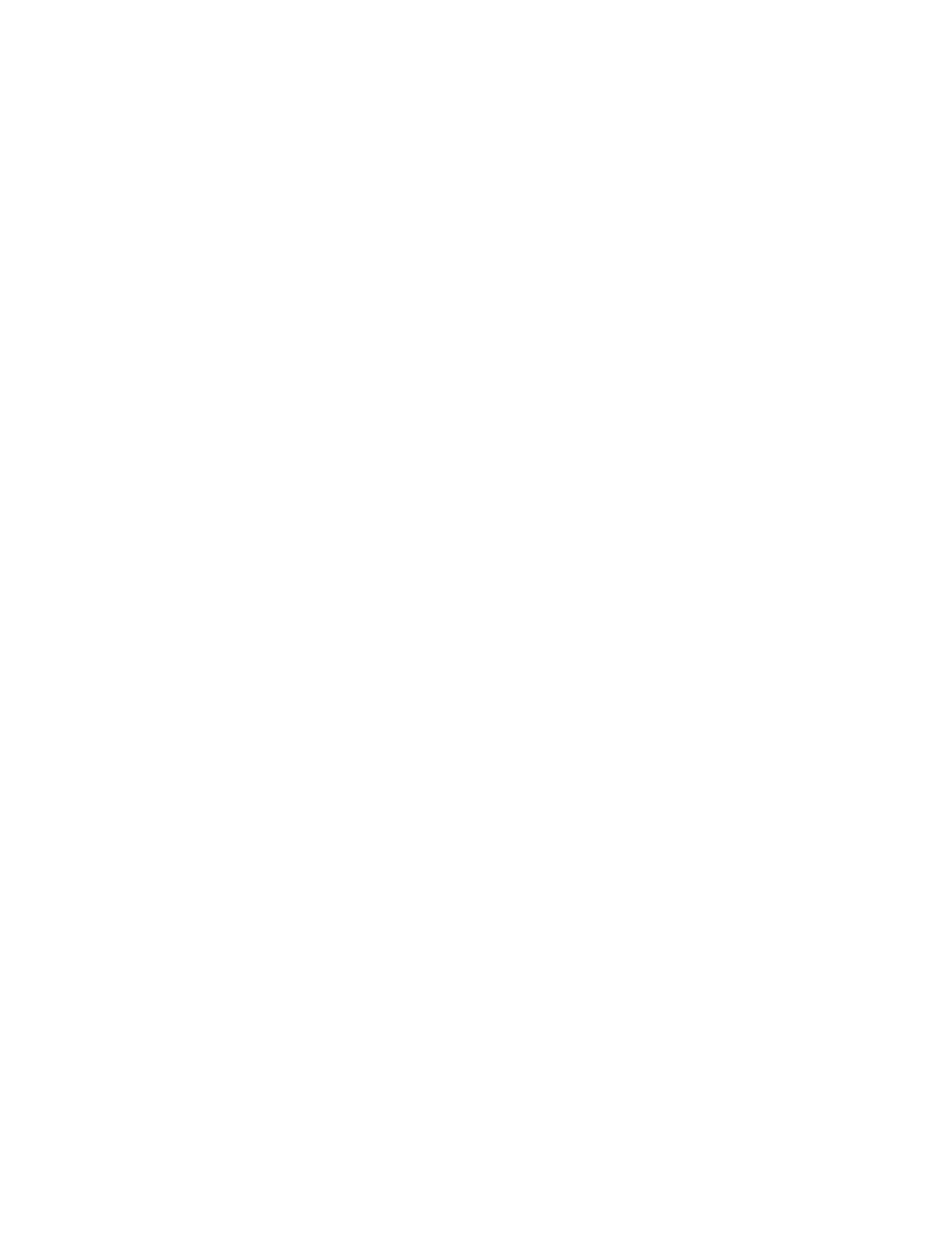
2180A
Table 3-1. Mnemonics
ANALOG COM
AZ
CM
DATA
DCLK
DE+
DE-
DIGITAL COM
D.P./NEG
INT 1
LINEAR
WRT
WRT ADR
X10
X100
A 2
+SENSE
-SENSE
+Vm
-V
Measurement common
Auto-Zero
Compare input to the microcomputer
Data on bus
Data clock
Positive read command
Negative read command
—15V with respect to Analog Com
Drives decimal point, depending on reading and resolution
Causes the unknown voltage to be integrated
Used to command the microcomputer to display linear counts
Write
Write address, signals that an address is being transmitted
Selects a buffer gain of X10 (0.1° resolution)
Selects a buffer gain of X100 (0.01° resolution)
Hold command
Voltage sense wires from RTD - no current flows In these wires
Voltage sense wires from RTD - no current flows in these wires
An intermediate voltage - not used directly
Current return
3-9. CIRCUIT ANALYSIS
3-10. Circuit analysis of the 2180A is discussed in two
sections: digital and analog. The digital section is covered
first; particular attention is paid to digital control of the
analog section. The analysis of the analog section covers
the analog measurement circuitry and the 2180A power
supply.
3-11. Digital Section
3-12. The digital section of the 2180A consists of a
single-chip
microcomputer
with
a
self-contained,
programmed, read only memory (U9), a hex CMOS open
drain buffer (U13), and an LED display. This section,
shown in Figure 3-2, will provide the following functions:
1.
Conversion of the non-linear RTD probe
voltage, as measured by the analog section, into a
linear digital display.
2. Control of the analog section.
3. Control of all accessories on the accessory bus.
3-13. The microcomputer (U9) contains all of the 2180 A
programming, control logic, and linearizing capability. It
also provides all signals necessary to update the display.
Linearization of the RTD signal is accomplished by using
a piece-wise, 4th order, curve-fit approximation for each
3-2
type of RTD. One of the seven operating programs is
selected for the RTD type by setting S1 on the RTD Input
Module. A table showing RTD switch setting numbers
and corresponding RTD types is printed on the RTD
Input Module PCB.
3-14. Measurement data is continuously strobed out of
the
microcomputer
in
decoded-seven-segment,
bit-
parallel, character-serial format. This data is then sent to
the LED display.
3-15. The total measurement cycle takes 300 ms. The
cycle consists of the following periods:
1. Auto-Zero period (100 to 200 ms).
2.
Integrate period (100 ms). A 1 ms nominal hold
signal is inserted at the beginning and end of the
Integrate period to accomodate settling times in the
analog section.
3. Read period (variable 0 to 100 ms).
3-16. Analog Section
3-17. ANALOG MEASUREMENT CIRCUIT
3-18. The analog measurement circuitry consists of an
RTD input circuit, two voltage reference circuits, a
ground sense amplifier, a buffer amplifier, a dual slope