2 feeding material, 3 dust exhaust, 4 final fineness – FRITSCH PULVERISETTE 1, Model I premium line User Manual
Page 36: Working with the laboratory jaw crusher
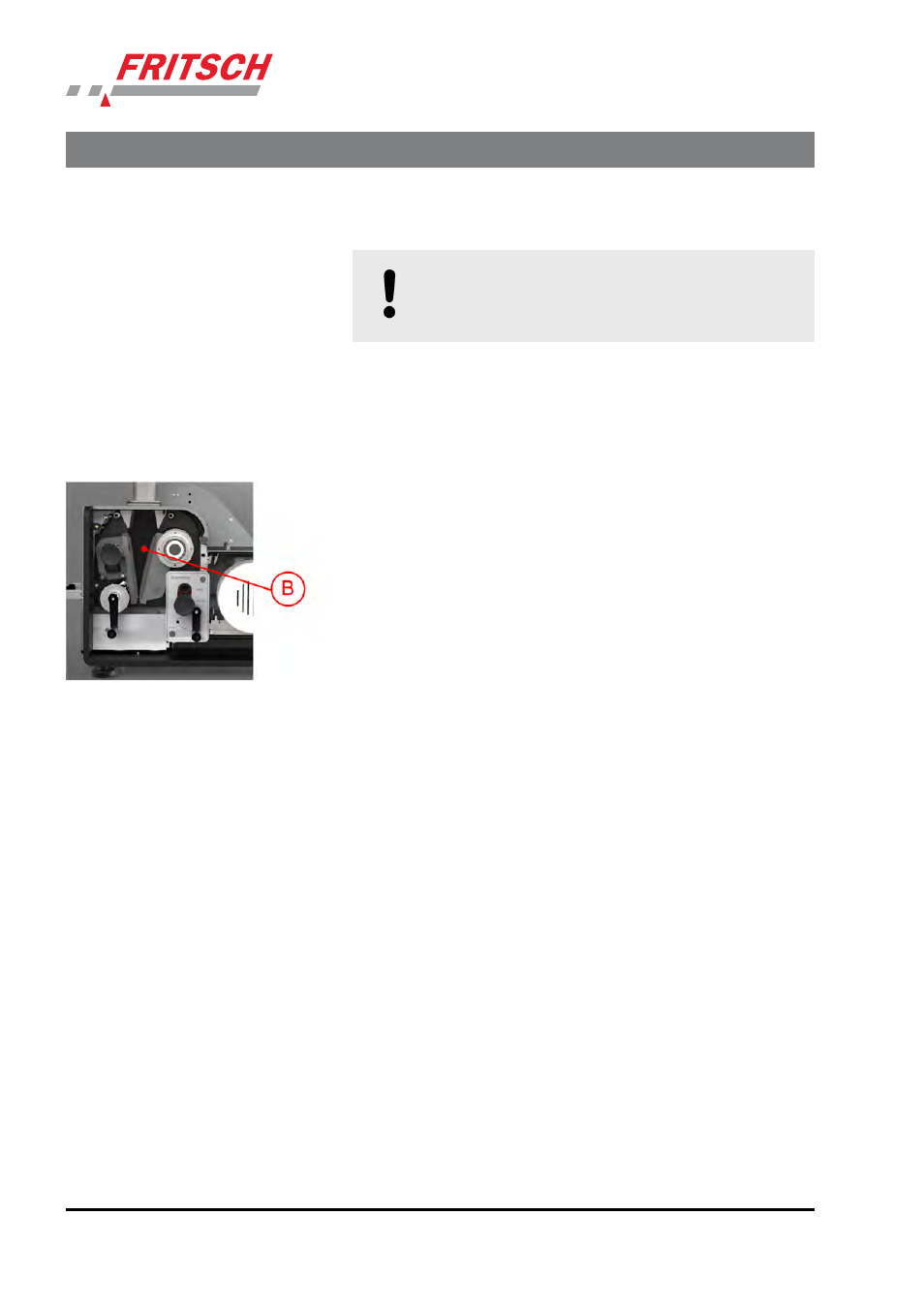
5.3.2 Feeding material
NOTICE!
Before filling the material into the funnel, switch on the
device.
Feed large chunks of material
n
model I, maximum edge length 60 mm,
n
model II, maximum edge length 95 mm
separately to the funnel.
Do not add more material until the crushing noise has fallen significantly.
Never fill more material to be crushed into the funnel than the actual
crushing chamber (B) can hold. This is limited by the upper edge of the
support walls (11) and by crushing plates (17; 21).
No material may lie above these edges. During continuous operation,
you may also only feed the same amount as is discharged as crushed
material.
The maximum amount to be fed depends on the material's crushing
capability and the selected gap width. Observe the crushing process
(crushing noise) for each new material and determine the optimum
amount to be fed.
5.3.3 Dust exhaust
Comminution of certain materials (e.g. coal, lumps of rock, stones) may
result in the development of dust, which accumulates in the crushing
chamber (B). To prevent it from spreading, the Jaw Crusher can be
equipped with a dust exhaust system. See Ä Chapter 6.1 ‘Dust exhaust’
5.3.4 Final fineness
The final fineness achieved depends on the material properties and the
gap setting between the two crushing plates. However, this gap width
only determines one dimension of the crushed material. This means that
for material crushed into plates, a second cycle can be applied to signifi-
cantly reduce the proportion of long parts or parts with a large surface.
At the smallest set gap width, the average particle size (d
50
) of the
crushed material is about 2mm.
Working with the laboratory jaw crusher
- 36 -