System design – Rice Lake Weigh Modules/Mount Assemblies User Manual
Page 7
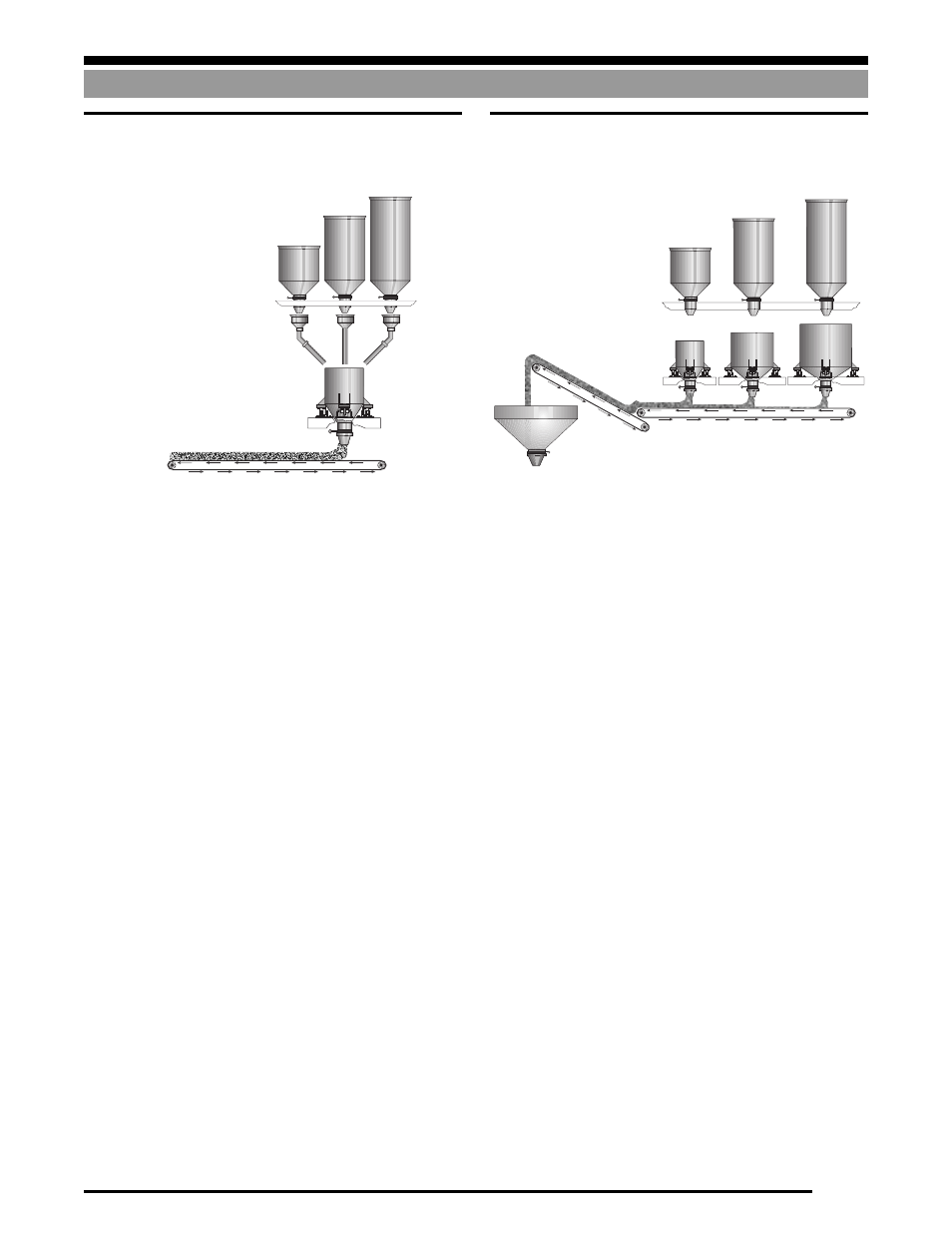
1-5
SYSTEM DESIGN
Bulk Material Weighing Systems
G. Figure 1-11 illustrates a multiple-ingredient batching sys-
tem where all the ingredients are weighed one at a time in a
single weigh hopper.
Advantages of this system are:
•
Lower cost than multiple-weigh hoppers
•
Scale calibration may not be critical, as all ingredients are
weighed in a single scale, assuring correct proportions.
Disadvantages of this system are:
•
The accuracy of minor ingredients may suffer where the scale
capacity is large compared to the weight of ingredient.
•
System is somewhat slow because each material must be
batched in one at a time, and the cycle cannot repeat until the
weigh hopper has been discharged.
Note: We recommend that you do not attempt to weigh a batch of
material which is less than 20 scale divisions since the accuracy
will be questionable.
For example, if a hopper scale has a .5 lb division size, we recom-
mend that you not weigh less than a 10-lb batch on that scale. It’s
better to weigh minor ingredients accurately on a scale suited to
the purpose, and add those ingredients to the batch by hand. For
example, if making raisin oatmeal cookies, it may not be too much
of a problem to batch-weigh the raisins along with the oatmeal.
However, it may be prudent to weigh the salt on a more sensitive
bench scale and hand-add it to the hopper at completion of the
weigh cycle.
Figure 1-11
Figure 1-12
H. The system illustrated in Figure 1-12 below is a multi-
ingredient batching system which has a separate weigh hop-
per for each ingredient.
Advantages of this system are:
•
Weigh hopper capacity can be sized appropriately for each
material so that each weighment is close to the scale capacity,
providing greater accuracy.
•
Faster throughput, since all materials can be weighed and
discharged simultaneously.
Disadvantages of this system are:
•
Higher cost.
•
Each scale must be accurate to ensure correct proportioning.