Cypress CY7C1312AV18 User Manual
Page 13
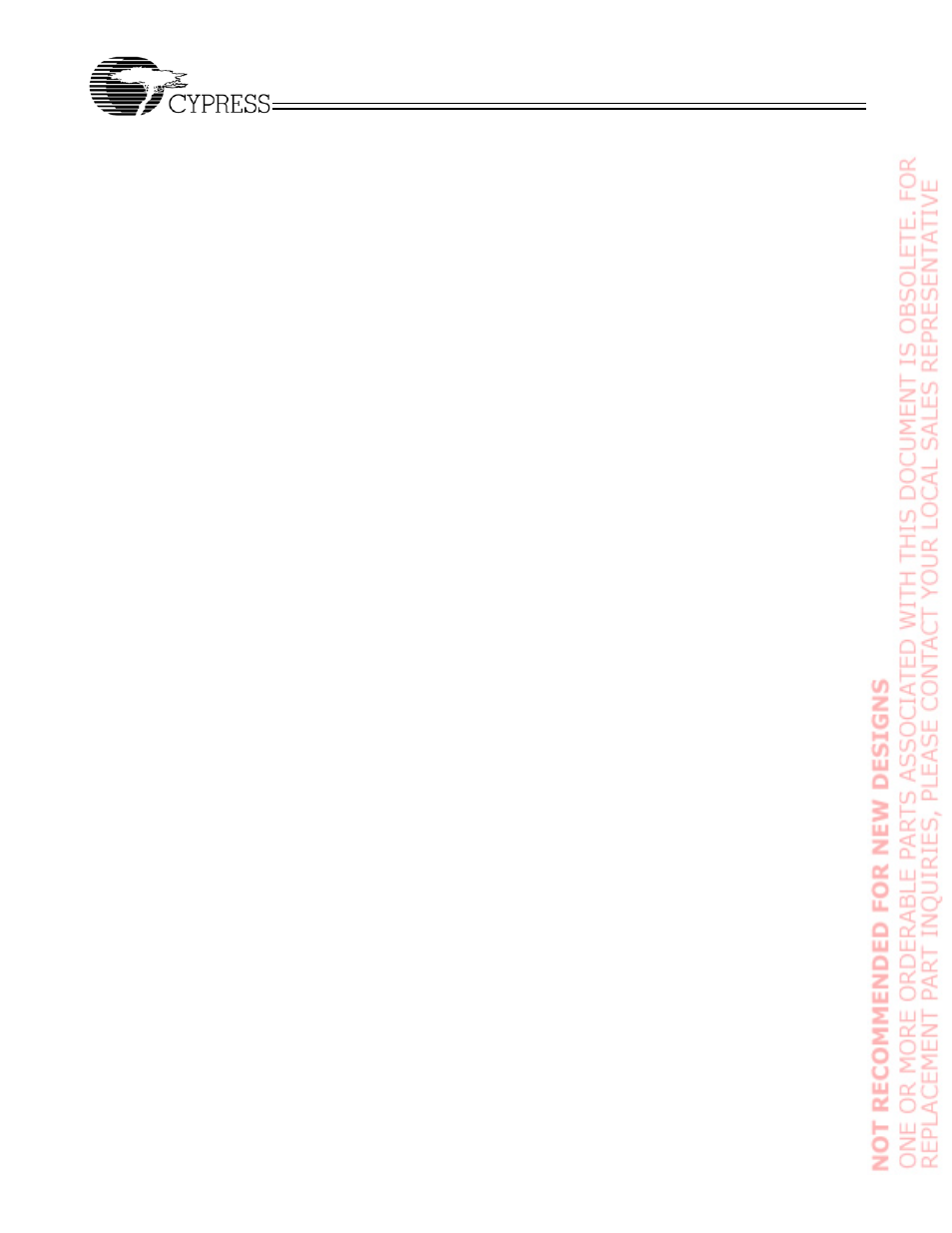
CY7C1310AV18
CY7C1312AV18
CY7C1314AV18
PRELIMINARY
Document #: 38-05497 Rev. *A
Page 13 of 21
IEEE 1149.1 Serial Boundary Scan (JTAG)
These SRAMs incorporate a serial boundary scan test access
port (TAP) in the FBGA package. This part is fully compliant
with IEEE Standard #1149.1-1900. The TAP operates using
JEDEC standard 1.8V I/O logic levels.
Disabling the JTAG Feature
It is possible to operate the SRAM without using the JTAG
feature. To disable the TAP controller, TCK must be tied LOW
(V
SS
) to prevent clocking of the device. TDI and TMS are inter-
nally pulled up and may be unconnected. They may alternately
be connected to V
DD
through a pull-up resistor. TDO should
be left unconnected. Upon power-up, the device will come up
in a reset state which will not interfere with the operation of the
device.
Test Access Port–Test Clock
The test clock is used only with the TAP controller. All inputs
are captured on the rising edge of TCK. All outputs are driven
from the falling edge of TCK.
Test Mode Select
The TMS input is used to give commands to the TAP controller
and is sampled on the rising edge of TCK. It is allowable to
leave this pin unconnected if the TAP is not used. The pin is
pulled up internally, resulting in a logic HIGH level.
Test Data-In (TDI)
The TDI pin is used to serially input information into the
registers and can be connected to the input of any of the
registers. The register between TDI and TDO is chosen by the
instruction that is loaded into the TAP instruction register. For
information on loading the instruction register, see the TAP
Controller State Diagram. TDI is internally pulled up and can
be unconnected if the TAP is unused in an application. TDI is
connected to the most significant bit (MSB) on any register.
Test Data-Out (TDO)
The TDO output pin is used to serially clock data-out from the
registers. The output is active depending upon the current
state of the TAP state machine (see Instruction codes). The
output changes on the falling edge of TCK. TDO is connected
to the least significant bit (LSB) of any register.
Performing a TAP Reset
A Reset is performed by forcing TMS HIGH (VDD) for five
rising edges of TCK. This RESET does not affect the operation
of the SRAM and may be performed while the SRAM is
operating. At power-up, the TAP is reset internally to ensure
that TDO comes up in a high-Z state.
TAP Registers
Registers are connected between the TDI and TDO pins and
allow data to be scanned into and out of the SRAM test
circuitry. Only one register can be selected at a time through
the instruction registers. Data is serially loaded into the TDI pin
on the rising edge of TCK. Data is output on the TDO pin on
the falling edge of TCK.
Instruction Register
Three-bit instructions can be serially loaded into the instruction
register. This register is loaded when it is placed between the
TDI and TDO pins as shown in TAP Controller Block Diagram.
Upon power-up, the instruction register is loaded with the
IDCODE instruction. It is also loaded with the IDCODE
instruction if the controller is placed in a reset state as
described in the previous section.
When the TAP controller is in the Capture IR state, the two
least significant bits are loaded with a binary “01” pattern to
allow for fault isolation of the board level serial test path.
Bypass Register
To save time when serially shifting data through registers, it is
sometimes advantageous to skip certain chips. The bypass
register is a single-bit register that can be placed between TDI
and TDO pins. This allows data to be shifted through the
SRAM with minimal delay. The bypass register is set LOW
(V
SS
) when the BYPASS instruction is executed.
Boundary Scan Register
The boundary scan register is connected to all of the input and
output pins on the SRAM. Several no connect (NC) pins are
also included in the scan register to reserve pins for higher
density devices.
The boundary scan register is loaded with the contents of the
RAM Input and Output ring when the TAP controller is in the
Capture-DR state and is then placed between the TDI and
TDO pins when the controller is moved to the Shift-DR state.
The EXTEST, SAMPLE/PRELOAD and SAMPLE Z instruc-
tions can be used to capture the contents of the Input and
Output ring.
The Boundary Scan Order tables show the order in which the
bits are connected. Each bit corresponds to one of the bumps
on the SRAM package. The MSB of the register is connected
to TDI, and the LSB is connected to TDO.
Identification (ID) Register
The ID register is loaded with a vendor-specific, 32-bit code
during the Capture-DR state when the IDCODE command is
loaded in the instruction register. The IDCODE is hardwired
into the SRAM and can be shifted out when the TAP controller
is in the Shift-DR state. The ID register has a vendor code and
other information described in the Identification Register
Definitions table.
TAP Instruction Set
Eight different instructions are possible with the three-bit
instruction register. All combinations are listed in the
Instruction Code table. Three of these instructions are listed
as RESERVED and should not be used. The other five instruc-
tions are described in detail below.
Instructions are loaded into the TAP controller during the
Shift-IR state when the instruction register is placed between
TDI and TDO. During this state, instructions are shifted
through the instruction register through the TDI and TDO pins.
To execute the instruction once it is shifted in, the TAP
controller needs to be moved into the Update-IR state.
IDCODE
The IDCODE instruction causes a vendor-specific, 32-bit code
to be loaded into the instruction register. It also places the
instruction register between the TDI and TDO pins and allows
the IDCODE to be shifted out of the device when the TAP
controller enters the Shift-DR state. The IDCODE instruction