If you are using the basic configuration, Step 5. turn on power to the drive, Step 10. turn on power to the drive – Rockwell Automation Flex/WebPak 3000 DC Drive DB Kit, 1.5 HP-150 HP-230V, 3HP-600 HP-460V w/o NEMA1 User Manual
Page 10
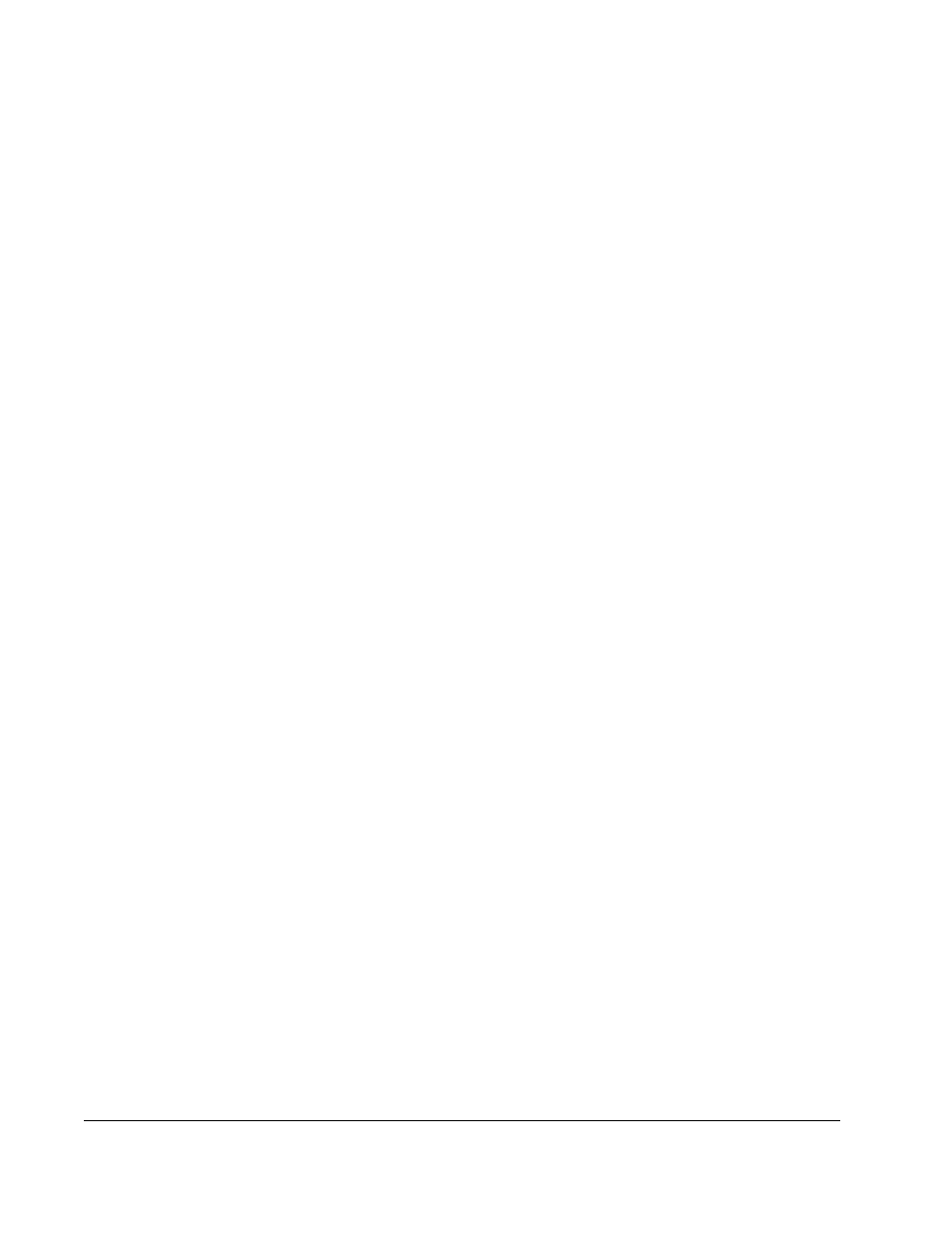
10
Dynamic Braking Kits for FlexPak 3000 and WebPak 3000 Digital DC Drives
•
DB with a Motor Series Field, S1 connected to A2
without an Inverting Fault Circuit Breaker (figure 8)
•
DB with a Motor Series Field, S1 connected to A2/S1
with an Inverting Fault Circuit Breaker (figure 9)
•
DB with a Motor Series Field, S1 connected to A2/S1
without an Inverting Fault Circuit Breaker (figure 9)
Locate and follow the steps for your drive configuration.
If you are using the Basic Configuration:
Step 1. Follow the wiring diagram in figure 5 to connect the motor armature and the Dynamic Braking Resistor
assembly to the FlexPak 3000 drive.
Step 2. Route the resistor assembly harness as required. Use M10 x 25 mm screws, nuts and washers to
attach resistor assembly harness to DBR and A2/S1 connections on the drive.
Step 3. Follow the wiring diagram in figure 5 to verify that the jumper across terminals 3 and 4 on the FIELD/
DB terminal block is installed.
Step 4. Remove the lockout and tag from the power to the drive.
Step 5. Turn on power to the drive.
If you are using DB with an Inverting Fault Circuit Breaker:
Step 1. Follow the wiring diagram in figure 7 to connect the motor armature and the Dynamic Braking Resistor
assembly to the FlexPak 3000 drive.
Step 2. Remove the Removable Link (see figure 6). It is a bus section below the A2/S1 terminal and is
accessed through the top of the drive as shown. At the top, the A2/S1 terminal and Removable Link
are fastened with two nuts and bolts, spaced horizontally. Remove them and set them aside along
with the A2/S1 terminal for subsequent re-installation. At the bottom, remove the two bolts spaced
vertically and set them aside. Take the Removable Link (bus section) out of the drive.
Step 3. Replace the lower two vertically-spaced bolts and tighten to 23 Nm (200 in-lb).
Step 4. Replace the A2/S1 terminal fastening it with the upper two horizontally-spaced nuts and bolts
previously removed. Tighten to 23 Nm (200 in-lb).
Step 5. Route the resistor assembly harness as required. Use M10 x 25 mm screws, nuts and washers to
attach resistor assembly harness to DBR and A2/S1 connections on the drive. See figure 7.
Step 6. Connect the Inverting Fault Circuit Breaker kit to the DRV and MOT terminals as shown.
Step 7. Route the customer-supplied wire (cable) and attach to the connections A2/S1 and MOT (or A2) as
shown.
Step 8. Follow the wiring diagram in figure 5 to verify that the jumper across terminals 3 and 4 on the FIELD/
DB terminal block is installed.
Step 9. Remove the lockout and tag from the power to the drive.
Step 10. Turn on power to the drive.