Rockwell Automation Flex/WebPak 3000 DC Drive DB Kit, 1.5 HP-150 HP-230V, 3HP-600 HP-460V w/o NEMA1 User Manual
Product description
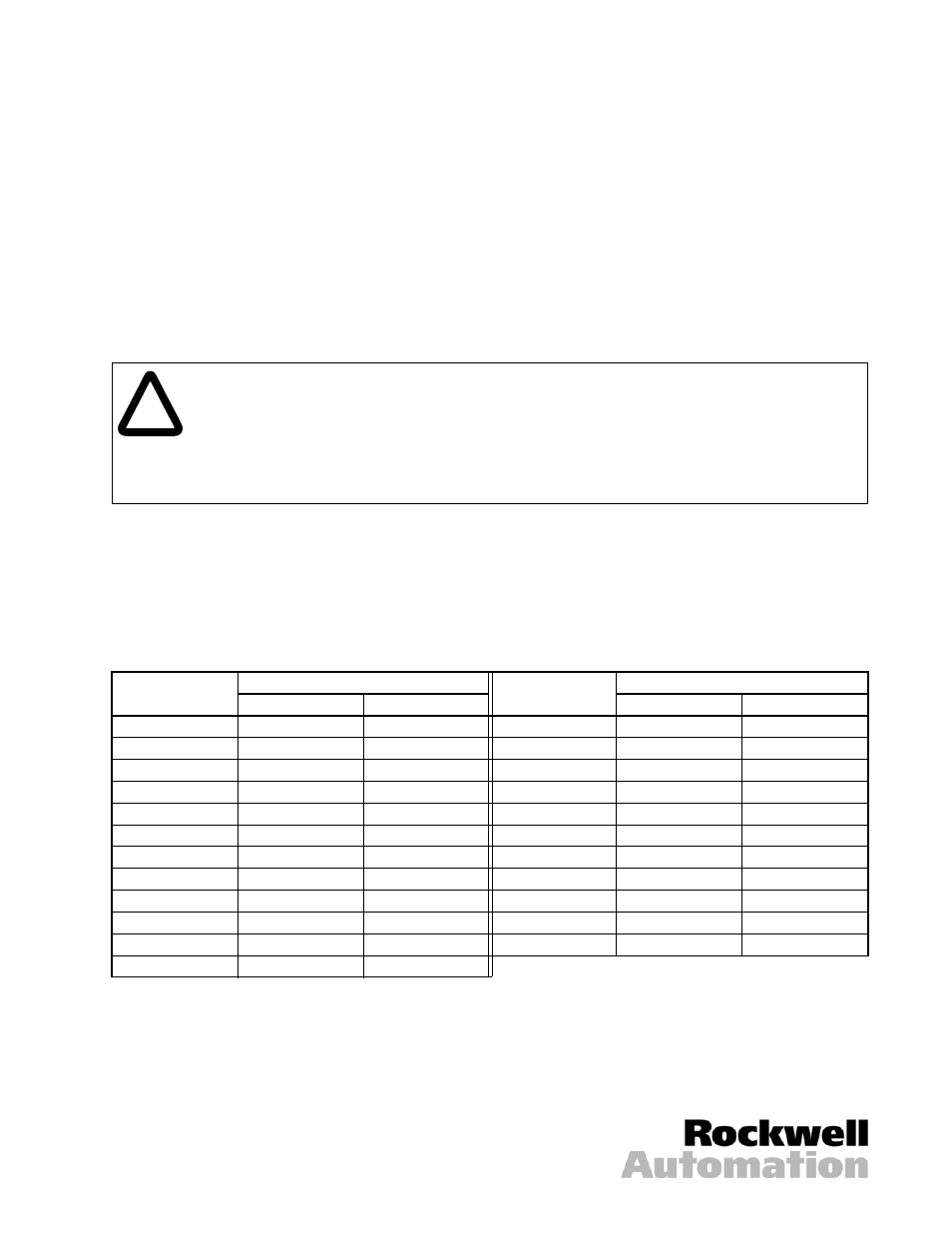
Reliance, FlexPak and WebPak are trademarks of Rockwell Automation.
© 2005 Rockwell International Corporation
Dynamic Braking Kit
for FlexPak 3000 and WebPak 3000 Digital DC Drives
1.5 HP to 150 HP @ 230 VAC, 3 HP to 600 HP @ 460 VAC
without NEMA1 Enclosures
Model Numbers 912FKxxxx and 913FKxxxx
Instruction Manual D2-3374-4
Product Description
This instruction manual describes how to install optional Dynamic Braking (DB) kits that are used with
FlexPak™ 3000 (1.5 HP to 150 HP @ 230 VAC, 3 HP to 600 HP @ 460 VAC) and WebPak™ 3000 (1.5 HP to
75 HP @ 230 VAC, 3 HP to 150 HP @ 460 VAC) DC drives. These kits consist of separate parts that must be
mounted by the customer. See the following table to verify the kit matches your drive.
!
ATTENTION: Only qualified personnel familiar with the construction and operation of this
equipment and the hazards involved should install, operate, and/or service this equipment. Read
and understand this instruction manual in its entirety before proceeding. Failure to observe this
precaution could result in severe bodily injury or loss of life.
ATTENTION: The user is responsible for conforming with all applicable local, national, and
international codes. Failure to observe this precaution could result in damage to, or destruction
of, the equipment.
Drive
Kit Model Number
Drive
Kit Model Number
Horsepower
230 VAC
460 VAC
Horsepower
230 VAC
460 VAC
1.5
912FK0010
—
60
912FK0500
913FK0500
2
912FK0020
—
75
912FK0750
913FK0750
3
912FK0030
913FK0030
100
912FK1000
913FK1000
5
912FK0050
913FK0050
125
912FK1250
913FK1000
7.5
912FK0070
913FK0070
150
912FK1500
913FK1500
10
912FK0100
913FK0100
200
—
913FK2000
15
912FK0150
913FK0150
250
—
913FK2500
20
912FK0200
913FK0200
300
—
913FK3000
25
912FK0250
913FK0200
400
—
913FK4000
30
912FK0300
913FK0300
500
—
913FK5000
40
912FK0400
913FK0400
600
—
913FK6000
50
912FK0500
913FK0500
Document Outline
- Model Numbers 912FKxxxx and 913FKxxxx
- Instruction Manual D2-3374-4
- Product Description
- Installing the Dynamic Braking Kit for 1.5 HP to 150 HP @ 230 VAC and 3 HP to 300 HP @ 460 VAC Drives
- Step 1. Turn off, lock out, and tag power to the drive.
- Step 2. Determine where you will mount the Dynamic Braking kit. Typically, the Dynamic Braking kit mounts on the roof of the dri...
- Step 3. Follow the wiring diagram in figure 3 to connect the motor armature, the DB contactor, and the DB resistor assembly to the drive.
- Step 4. Install the supplied suppressor (P/N 600686-33A) across the contactor coil. This suppressor is resistor 2SSR shown across the DB coil in figure 3.
- Step 5. Remove the jumper from the Field/DB terminal block on the drive (terminals 3 to 4). See figure 3. Connect the auxiliary contactor (DB AUX), terminals 13 and 14, to terminals 3 and 4, respectively, on the Field/DB terminal block.
- Step 6. Connect the user-supplied 115 VAC control power to the Dynamic Braking contactor (DBCR) and control circuit (Field/DB te...
- Step 7. Remove the lockout and tag from the power to the drive.
- Step 8. Turn on power to the drive.
- Dimension
- A
- B
- C
- D
- E
- F
- G
- H
- I
- Installing the DB Kit in 400 HP to 600 HP @ 460 VAC Drives
- Mounting the Resistor Assembly
- Step 1. Turn off, lock out, and tag power to the drive.
- Step 2. Refer to the parts listed in table 3. Determine where you will mount the Dynamic Braking kit. For typical applications, hardware is included for mounting on the roof of the drive cabinet enclosure.
- a. Drill 4 mounting holes and one wire access hole in the cabinet using the dimensions in figure 4.
- b. Install a grommet in the cabinet wire access hole.
- c. Mount the resistor assembly to the roof using 5/16” x 3/4” carriage bolts and nuts.
- d. Route the resistor assembly harness through the holes in the resistor assembly base and cabinet roof.
- e. Remove the top panel from the enclosure and set the screws aside.
- f. Mount the enclosure to the resistor assembly base using 10-32 screws and washers supplied.
- g. Replace the enclosure top panel and reattach screws.
- Wiring the DB Kit
- If you are using the Basic Configuration:
- Step 1. Follow the wiring diagram in figure 5 to connect the motor armature and the Dynamic Braking Resistor assembly to the FlexPak 3000 drive.
- Step 2. Route the resistor assembly harness as required. Use M10 x 25 mm screws, nuts and washers to attach resistor assembly harness to DBR and A2/S1 connections on the drive.
- Step 3. Follow the wiring diagram in figure 5 to verify that the jumper across terminals 3 and 4 on the FIELD/ DB terminal block is installed.
- Step 4. Remove the lockout and tag from the power to the drive.
- Step 5. Turn on power to the drive.
- If you are using DB with an Inverting Fault Circuit Breaker:
- Step 1. Follow the wiring diagram in figure 7 to connect the motor armature and the Dynamic Braking Resistor assembly to the FlexPak 3000 drive.
- Step 2. Remove the Removable Link (see figure 6). It is a bus section below the A2/S1 terminal and is accessed through the top o...
- Step 3. Replace the lower two vertically-spaced bolts and tighten to 23 Nm (200 in-lb).
- Step 4. Replace the A2/S1 terminal fastening it with the upper two horizontally-spaced nuts and bolts previously removed. Tighten to 23 Nm (200 in-lb).
- Step 5. Route the resistor assembly harness as required. Use M10 x 25 mm screws, nuts and washers to attach resistor assembly harness to DBR and A2/S1 connections on the drive. See figure 7.
- Step 6. Connect the Inverting Fault Circuit Breaker kit to the DRV and MOT terminals as shown.
- Step 7. Route the customer-supplied wire (cable) and attach to the connections A2/S1 and MOT (or A2) as shown.
- Step 8. Follow the wiring diagram in figure 5 to verify that the jumper across terminals 3 and 4 on the FIELD/ DB terminal block is installed.
- Step 9. Remove the lockout and tag from the power to the drive.
- Step 10. Turn on power to the drive.
- If you are using DB with a Motor Series Field, S1 connected to A2 with an Inverting Fault Circuit Breaker:
- Step 1. Follow the wiring diagram in figure 8 to connect the motor armature and the Dynamic Braking Resistor assembly to the FlexPak 3000 drive.
- Step 2. Remove the Removable Link (see figure 6). It is a bus section below the A2/S1 terminal and is accessed through the top o...
- Step 3. Replace the lower two vertically-spaced bolts and tighten to 23 Nm (200 in-lb).
- Step 4. Replace the A2/S1 terminal fastening it with the upper two horizontally-spaced nuts and bolts previously removed. Tighten to 23 Nm (200 in-lb).
- Step 5. Route the resistor assembly harness as required. Use M10 x 25 mm screws, nuts and washers to attach resistor assembly harness to DBR and A2/S1 connections on the drive. See figure 8.
- Step 6. Connect the Inverting Fault Circuit Breaker kit to the DRV and MOT terminals as shown. Ignore the dashed-line connection.
- Step 7. Route the customer-supplied wire (cable) and attach to the connections A2/S1 and Motor A2 (or Motor S1) as shown.
- Step 8. Connect the Series Field between the terminals Motor S1 and Motor S2.
- Step 9. Follow the wiring diagram in figure 5 to verify that the jumper across terminals 3 and 4 on the FIELD/ DB terminal block is installed.
- Step 10. Remove the lockout and tag from the power to the drive.
- Step 11. Turn on power to the drive.
- If you are using DB with a Motor Series Field, S1 connected to A2 without an Inverting Fault Circuit Breaker:
- Step 1. Follow the wiring diagram in figure 8 to connect the motor armature and the Dynamic Braking Resistor assembly to the FlexPak 3000 drive.
- Step 2. Remove the Removable Link (see figure 6). It is a bus section below the A2/S1 terminal and is accessed through the top o...
- Step 3. Replace the lower two vertically-spaced bolts and tighten to 23 Nm (200 in-lb).
- Step 4. Replace the A2/S1 terminal fastening it with the upper two horizontally-spaced nuts and bolts previously removed. Tighten to 23 Nm (200 in-lb).
- Step 5. Route the resistor assembly harness as required. Use M10 x 25 mm screws, nuts and washers to attach resistor assembly harness to DBR and A2/S1 connections on the drive. See figure 8.
- Step 6. Connect the S2 terminal to Motor S1 terminal (see the dashed-line in figure 8). Ignore the Inverting Fault Circuit Breaker illustrated in this figure.
- Step 7. Route the customer-supplied wire (cable) and attach to the connections A2/S1 and Motor A2 (or Motor S1) as shown.
- Step 8. Connect the Series Field between the terminals Motor S1 and Motor S2.
- Step 9. Follow the wiring diagram in figure 5 to verify that the jumper across terminals 3 and 4 on the FIELD/ DB terminal block is installed.
- Step 10. Remove the lockout and tag from the power to the drive.
- Step 11. Turn on power to the drive.
- If You are using DB with a Motor Series Field, S1 connected to A2/S1 with an Inverting Fault Circuit Breaker:
- Step 1. Follow the wiring diagram in figure 9 to connect the motor armature and the Dynamic Braking Resistor assembly to the FlexPak 3000 drive.
- Step 2. Remove the Removable Link (see figure 6). It is a bus section below the A2/S1 terminal and is accessed through the top o...
- Step 3. Replace the lower two vertically-spaced bolts and tighten to 23 Nm (200 in-lb).
- Step 4. Replace the A2/S1 terminal fastening it with the upper two horizontally-spaced nuts and bolts previously removed. Tighten to 23 Nm (200 in-lb).
- Step 5. Route the resistor assembly harness as required. Use M10 x 25 mm screws, nuts and washers to attach resistor assembly harness to DBR and A2/S1 connections on the drive. See figure 9.
- Step 6. Connect the Inverting Fault Circuit Breaker kit to the DRV and MOT terminals as shown. Ignore the dashed-line connection.
- Step 7. Route the wire (cable) and attach to the connections A2/S1 and Motor A2 as shown.
- Step 8. Similarly, as shown, route the customer-supplied wire (cable) and attach to the connections A2/S1 and the Motor S1 terminal.
- Step 9. Connect the Series Field between the terminals Motor S1 and Motor S2.
- Step 10. Follow the wiring diagram in figure 5 to verify that the jumper across terminals 3 and 4 on the FIELD/ DB terminal bloc...
- Step 11. Remove the lockout and tag from the power to the drive.
- Step 12. Turn on power to the drive.
- If you are using DB with a Motor Series Field, S1 connected to A2/S1 without an Inverting Fault Circuit Breaker:
- Step 1. Follow the wiring diagram in figure 9 to connect the motor armature and the Dynamic Braking (DB) Resistor assembly to the FlexPak 3000 drive.
- Step 2. Remove the Removable Link (see figure 6). It is a bus section below the A2/S1 terminal and is accessed through the top o...
- Step 3. Replace the lower two vertically-spaced bolts and tighten to 23 Nm (200 in-lb).
- Step 4. Replace the A2/S1 terminal fastening it with the upper two horizontally-spaced nuts and bolts previously removed. Tighten to 23 Nm (200 in-lb).
- Step 5. Route the resistor assembly harness as required. Use M10 x 25 mm screws, nuts and washers to attach resistor assembly harness to DBR and A2/S1 connections on the drive. See figure 9.
- Step 6. Connect the S2 terminal to Motor S1 terminal; see the dashed-line in figure 9. Ignore the Inverting Fault Circuit Breaker illustrated in this figure.
- Step 7. Route the wire (cable) and attach to the connections A2/S1 and Motor A2 as shown.
- Step 8. Similarly, as shown, route the customer-supplied wire (cable) and attach to the connections A2/S1 and the Motor S1 terminal.
- Step 9. Connect the Series Field between the terminals Motor S1 and Motor S2.
- Step 10. Follow the wiring diagram in figure 5 to verify that the jumper across terminals 3 and 4 on the FIELD/ DB terminal bloc...
- Step 11. Remove the lockout and tag from the power to the drive.
- Step 12. Turn on power to the drive.
- Figure 4 - Resistor Assembly Mounting Dimensions for 250 HP to 600 HP @ 460 VAC Drives
- Figure 5 - DB Kit Wiring Diagram for 400 HP to 600 HP @ 460 VAC Drives
- Figure 6 - Removable Link Accessed Through the Top of the Drive
- Figure 7 - DB with Inverting Fault Circuit Breaker
- Figure 8 - DB with Series Field and Inverting Fault Circuit Breaker (S1 to A2)
- Figure 9 - DB with Series Field and Inverting Fault Circuit Breaker (S1 to A2/S2)
- If you are using the Basic Configuration:
- Mounting the Resistor Assembly
- Technical Specifications