Reducing electrical interference – Rockwell Automation 9000 Series Sensor User Manual
Page 20
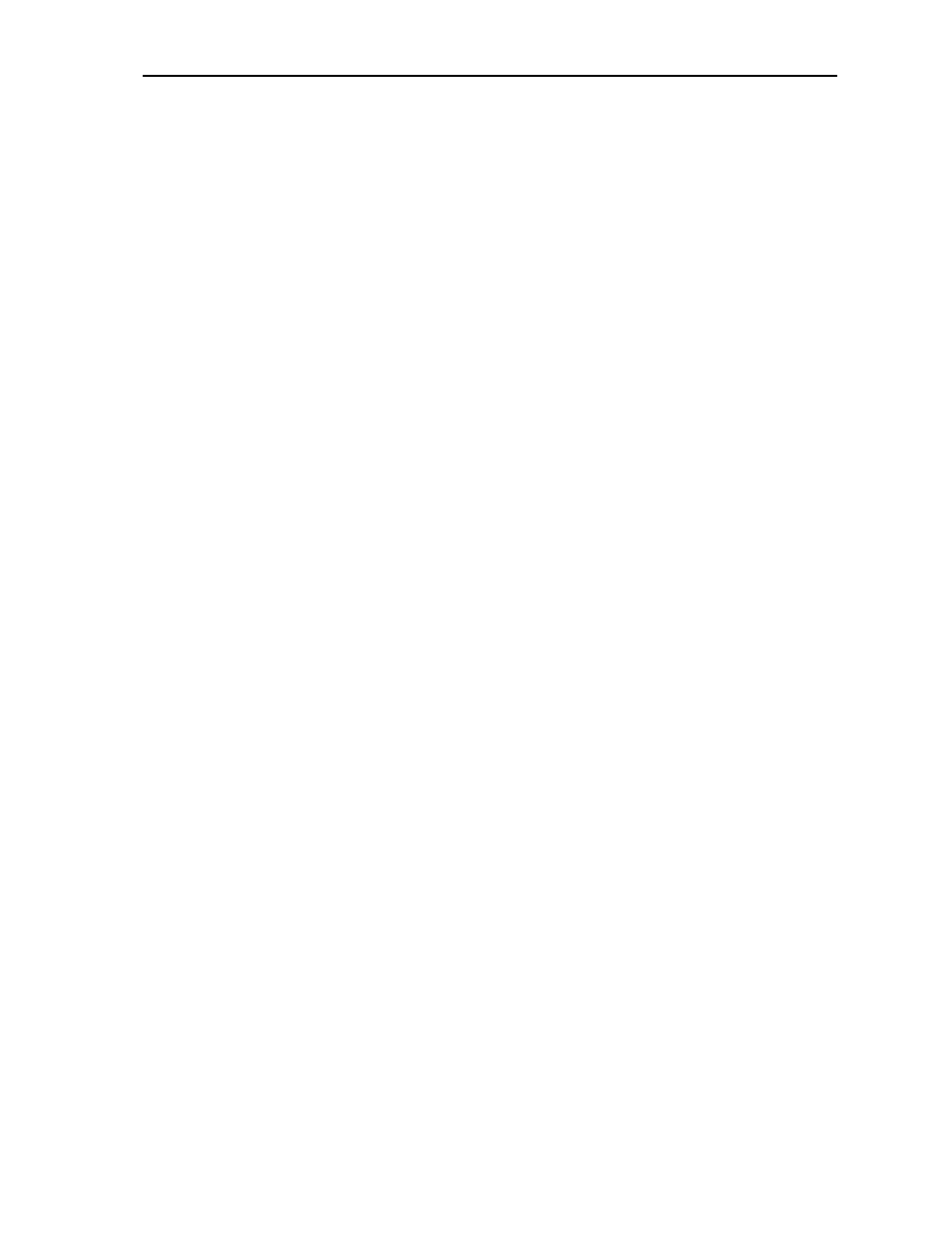
12
Entek 9000 Series Sensor Installation Guide
Sensor Cable Guidelines
For example, when running a 100ft. cable with a capacitance of 30 pF/ft, the total
capacitance is 3000 pF. This value can be found along the diagonal cable capacitance lines.
Assuming the sensor operates at a maximum output range of 5 volts and the constance
current signal conditioner is set at 2 mA, the ratio on the vertical axis can be calculated to
equal 5. The intersection of the total cable capacitance and this ratio result in a maximum
frequency of approximately 10.2 kHz.
The nomograph does not indicate whether the frequency amplitude response at a point is
flat, rising, or falling. For precautionary reasons, it is good general practice to increase the
constant current (if possible) to the sensor (within its maximum limit) so that the frequency
determined from the nomograph is approximately 1.5 to 2 times greater than the maximum
frequency of interest.
Reducing electrical interference
The small electrical signal coming from a sensor can be affected by electrical interference.
Make every effort to reduce the electrical interference in cables to the lowest acceptable
levels. Interference can come from many sources, including power cables, switching
devices, motor controllers, walkie-talkies, robot transmitters, arc welders, induction heating
equipment, motors, and high voltage ignition systems.
The following methods are effective for minimizing electrical interference:
!
Use twisted pair wires in each cable.
!
Use individual foil shields around each pair, with a shield drain wire grounded at only
one point for each shield. Do not ground the shield at both ends of the cable. Grounding
the cable shield at both ends causes a “ground loop.” This can cause interference
because in most cases the ground potential differs at the two ends.
!
Electrically isolate (insulate) each sensor circuit from all others.
!
Surround all cables with grounded steel conduit where possible.
!
Do not use conduits containing sensor cables for any other circuits.
!
Avoid running 9000 series sensor cables parallel to other cables, such as non-9000
series sensor, or communication cables.
!
Avoid running sensor cables parallel to power wiring. When this cannot be avoided,
make sure that sensor cables are at least 12 inches away from all power wiring carrying
120 V or less. For power circuits of 120–240 V, the minimum spacing is 24 inches. For
circuits of 480 V or higher, the minimum spacing is 48 inches.
!
If the cable must cross power wiring, maintain the above spacing between the wires.
Cross the wires at a right angle (90°) to minimize interference.
!
Make sure the cable is securely fastened to reduce low frequency noise from cable
movement. This is particularly important at the sensor end of the cable.