4 udc/pmi communication – Rockwell Automation SA3100 AutoMax Distributed Power System User Manual
Page 44
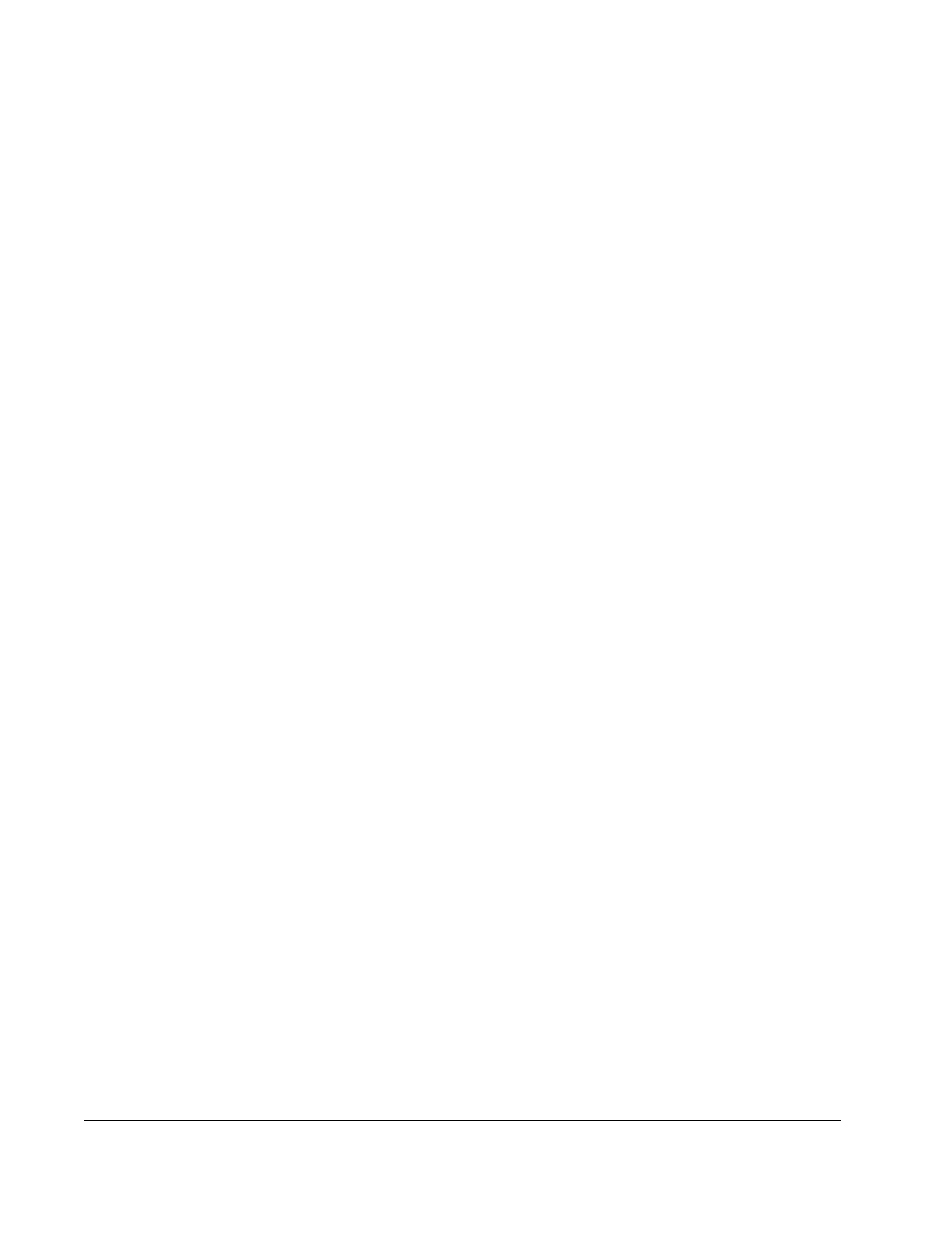
3-6
AutoMax Distributed Power System Overview
•
Command data
This information consists of data stored in the UDC dual port memory. The UDC
task or an AutoMax task writes to these registers to enable or disable the control
algorithm, to request self-tuning of certain system characteristics, and to specify the
reference to the control algorithm.
•
Pre-defined variables
This information consists of the pre-defined variables used to store data such as
minor loop gain data, resolver calibration data, and diagnostic data. These
variables, which vary by drive type, must be defined in every UDC task.
3.4
UDC/PMI Communication
When the UDC module and PMI are first connected over the fiber-optic link, the PMI
will request its operating system from the UDC module. As long as the UDC module
has its own operating system and the drive parameters are loaded, it will download the
appropriate operating system to the PMI.
Communication between the two PMIs (drives A and B) and the UDC module running
the corresponding UDC tasks consists of synchronized command and feedback
messages sent over the fiber-optic link.
A command message is sent to the PMI by the UDC module at the end of every scan
of the UDC task. Each message contains the command data, rail data, and the values
of the pre-defined variables that have changed.
A feedback message is sent to the UDC module by the PMI immediately before the
beginning of every scan of the UDC task. Each message contains the feedback data,
as well as any rail data that has changed from the last message.