USG Plasters and Gypsum Cements for the Ceramic Industry User Manual
Page 6
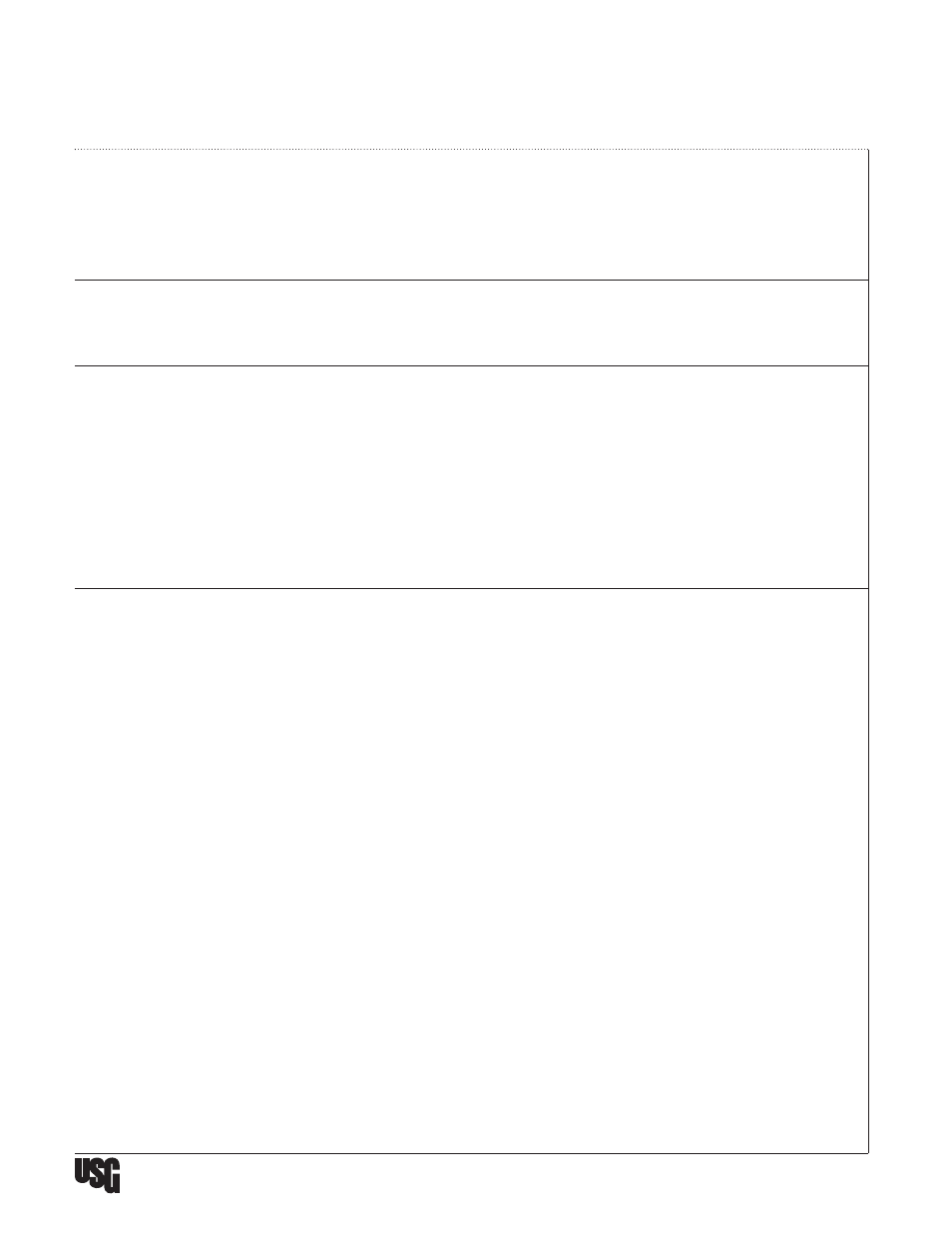
Manufactured by
United States Gypsum Company
550 West Adams Street
Chicago, IL 60661
800.487.4431
usg.com/industrialandspecialty
IG526/rev. 4-03
© 2003, United States Gypsum Company
Printed in U.S.A.
For blocking and casing, setting expansion is multiplied twice (once in block mold and once in case mold).
Consequently, it is good practice to block and case with specially formulated gypsum cements with setting
expansion of just 0.05%. These gypsum cements are dense and therefore not absorptive enough to serve as
working molds, but are eminently suited to accurate blocking and casing.
Handling Expansion
Many situations exist where flexible, rubber-faced or urethane elastomer case molds may be used to eliminate
Problems
or reduce expansion difficulties. Sometimes all that is needed is a small metal, rubber or urethane insert at a
particularly troublesome spot in an otherwise conventional case mold. Several sanitary potteries now use urethane
elastomer case molds for the majority of their long-run pieces. However, for maximum precision, several precautions
must be taken to prevent distortion of the elastomer. Either the rubber must be bonded to the backup or have
sufficient thickness to hold the dimensions.
Case and block molds must be properly stored, since considerable time may elapse between uses. It is important
to cover cases and blocks; place molds flat, or brace to prevent distortion caused by cold flow; maintain relative
humidity of at least 30%, and maximum temperature of 100 °F to prevent calcination; occasionally dampen stored
molds; use an indexing system to show names or code numbers on mold exteriors. This reduces breakage caused
by excessive handling and saves time in locating case molds.
Summary
Well-made molds handled with reasonable care on well-designed machines last longer and produce higher ware
quality than hand forming.
The causes of premature mold failure in mechanized and hand forming do not differ greatly. Generally, these are:
1. Abrasion, chipping and cracks caused by unduly weak molds, rough handling and mechanical wear.
2. Thermal shock and calcination from drying too fast or too long (jigger and hot press).
3. Weak or “rotten” molds from too little drying (casting molds).
4. Pinholes resulting from inadequate mixing.
5. Localized wear caused by repetitive machine stresses.
Best results are achieved only when mold shop variables are well controlled. Proper equipment should be provided
to make good control possible, and periodic checks on procedures should be made. Mold performance on the
machine should be followed regularly and adjustments made as needed. Painstaking attention to detail in production
and use result in satisfactory, long-wearing molds.