USG Plasters and Gypsum Cements for the Ceramic Industry User Manual
Page 3
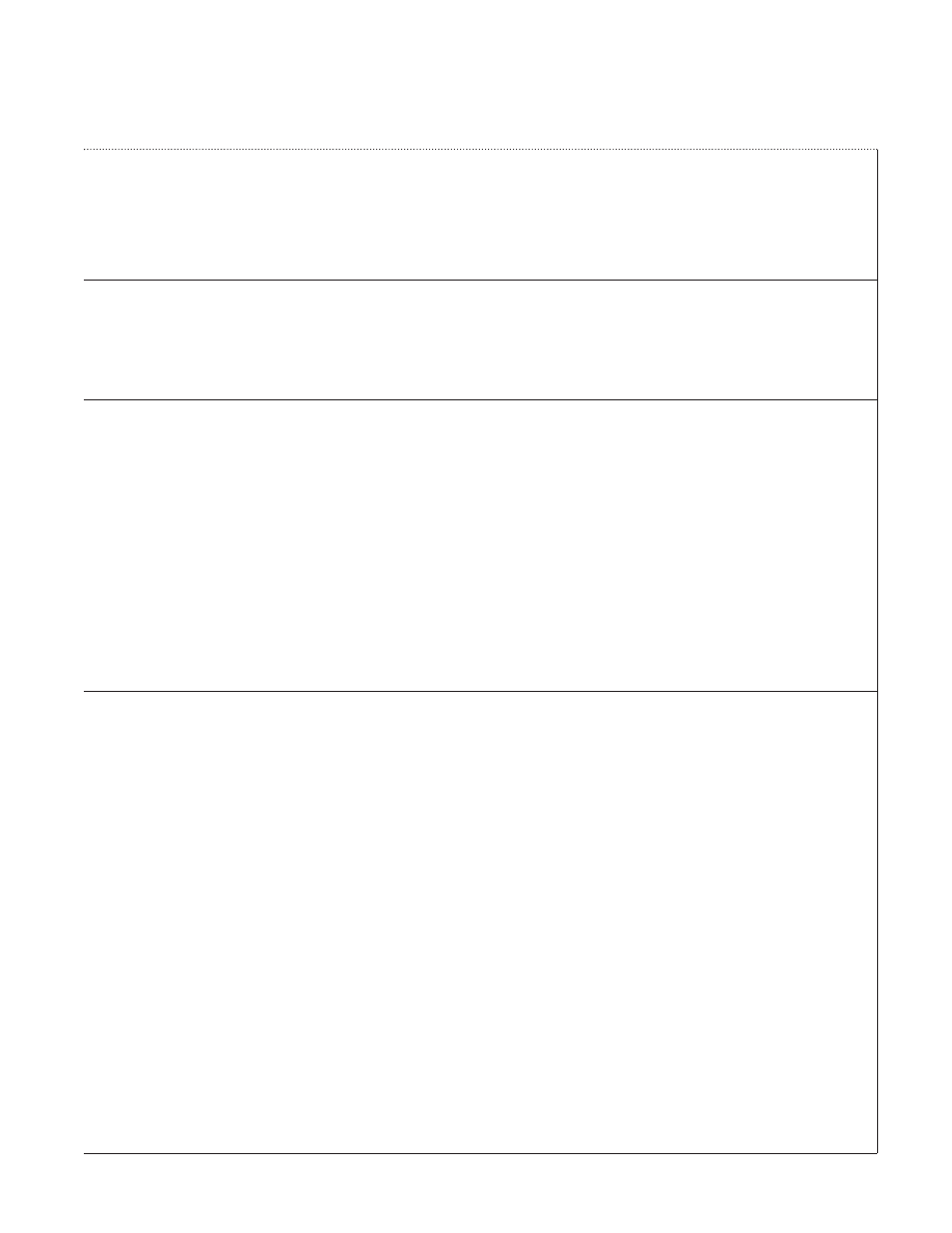
To hold down costs, use as dense a mold as shop conditions permit. Denser molds are stronger, more resistant to
deterioration, and longer lived. Many shops could improve quality and productivity by using denser molds.
Summary: as free water in the mold is removed by drying and evaporation, pores of the mold seal to some degree.
For optimum performance, they must be re-opened. This is accomplished by immersing the dried mold in water,
then re-drying and re-immersing to condition; or by immersing to condition and discarding the first casting.
Absorptive Rates
In early service life, casting molds gain markedly in rate of absorption, improving until the mold reaches
equilibrium with the drying environment. At this early stage, absorptive power of the mold is limited by either
the rate at which water can be taken from the slip, or the rate at which water is removed from the mold by drying.
In most shops, rate of drying is the limiting factor. Typical rates of absorption for conventionally made molds:
partial immersion of a new dry mold–0.38 g/cm
2
/min.; partial immersion of a new mold after three wetting
and drying cycles–0.60 g/cm
2
/min.; estimated safe rate of casting of plastic clay slip–0.30 g/cm
2
/min.;
drying rate in typical clay shop environment–0.01 g/cm
2
/min.
In the average shop, ability of the mold to function consistently depends greatly upon how efficiently it is dried
between cycles. If the rate of mold drying is adequate, molds may be denser since comparatively large reservoir
action is not needed. (See U.S. Gypsum Bulletin IG-502 for drying information.) The chief advantages of a
denser mold are longer life and greater economy.
Rates of absorption previously listed are considered maximum for plaster molds. In practice, shop conditions
affect absorptive rates, probably lowering them. Actual values in the clay shop should be determined by successive
weighings of molds when new, dry, in good condition, and periodically during service.
Some Tests for Absorption
Rate of absorption can be tested as follows:
If molds are not casting fast enough or are sticking, weigh them. Molds of the same design should weigh about
the same at the same point in the casting cycle. If they are much different, reweigh the molds elsewhere in
the casting cycle. If the molds do not lose the same percentage of weight during the drying cycle, drying is the
problem. On the other hand, consistency and, therefore, total pore volume could be different. If identical dry molds
differ significantly in weight, the problem is lack of uniformity from batch to batch.
Predictable water movement requires only with sound, homogeneous, properly made molds. Homogeneous molds
in turn are maintained only by practicing proper mixing and casting methods. (For recommended mixing methods,
see U.S. Gypsum Bulletin IG-503.)
Rate of absorption can be checked by claying small metal rings on the surface of a dried mold. By timing the
absorption of a certain volume of water through the surface area within the ring, you can compare the rate of one
mold versus another. Also, by running a check at various times in the life of a mold, relative rates can be retested.
When the clay shop bench-casts greenware, the design of the plaster tooling and working molds has considerable
latitude. The mold’s shape, wall thickness, etc., can be varied to create the best casting mold. However, when the
clay shop is mechanized, considerable latitude is lost. Some of the basic operations in a mechanized clay shop are
a continuing casting line, mechanical jiggering and the R
AM
®
process.
In mechanized casting, a mold is usually delivered to a pouring spout and clay slip is poured into the mold. The
filled mold is carried through controlled temperature and humidity in a set time interval, after which the partly
dried ware is removed. The empty mold passes through controlled drying conditions for a specific time and the
cycle is repeated. A modification of this procedure is to pressure-cast the slip while subjecting the mold exterior
to a vacuum. (For hollow-cast ware, drying must be preceded by draining the excess slip.)
3