USG Plasters and Gypsum Cements for the Ceramic Industry User Manual
Page 4
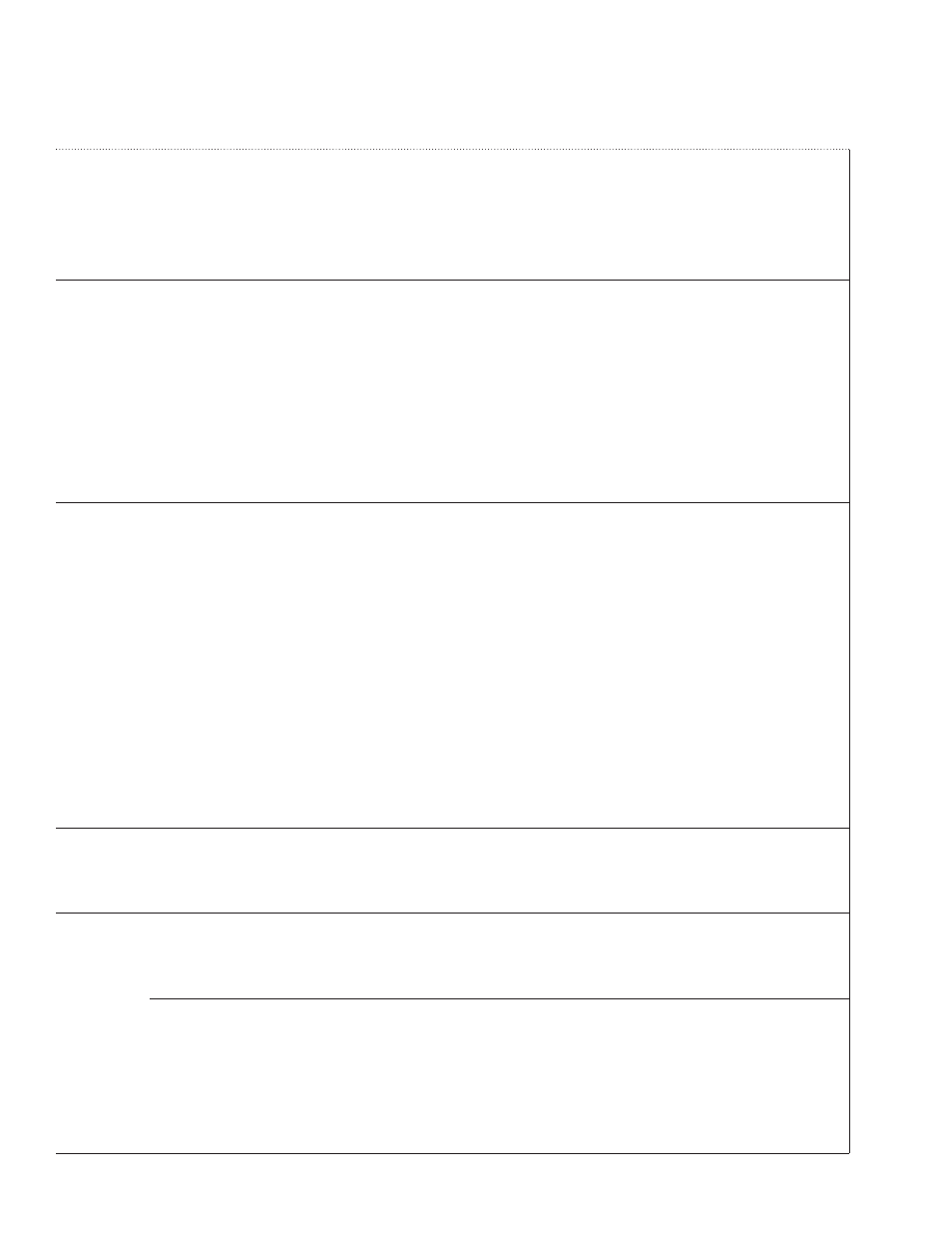
In mechanical jiggering, a clay bat of measured size is cut off a column of pugged clay so as to fall on the mold
face. A stamping or rotary pressing operation pre-forms the clay shape and a jigger tool is applied. Mold and ware
are carried automatically through a regulated drying atmosphere. After the partly dried ware is removed, the empty,
dry mold is returned for another cycle.
The press forming of electrical porcelain bodies is quite similar to automatic jiggering, except that a flame is con-
stantly applied to the forming tool to facilitate fabrication. Here the clay piece is also dried on, or in, the mold.
In the R
AM
process, the clay bat is shaped by mating male and female dies made of C
ERAMI
-C
AL
®
Gypsum Cement.
The dies are sufficiently permeable for use with air pressure or vacuum, as desired, and the greenware is removed
immediately after forming. Drying the dies is not a problem, since water is removed immediately by pressure-
induced evaporation.
Characteristics of
In manual fabrication of clayware, a skilled craftsman is able to make adjustments, within limits, to compensate
Mechanized Fabrication
for variations in the absorption, dimensions, strength, and relative dryness of molds.
Mechanization greatly changes this situation. Instead of relying on the craftsman to adjust for changed conditions,
everything possible is standardized so desired results will be obtained uniformly and automatically.
Once adequate control is established over the forming process, it is typical to mechanize subsequent operations,
such as trimming and finishing.
With mechanized forming, superior process control is required all along the line. This is especially true for molds,
which must be uniform in size and shape, smoothness, amount and rate of water absorption, strength and tough-
ness, and ability to produce acceptable ware.
Ordinarily, mechanized production molds enter or are retired from service in sets rather than individually. This
practice simplifies cost accounting, facilitates experimentation and analysis, reduces the work of mold makers
and handlers, tends to produce more uniform clayware, and results in fewer damaged molds. Batching demands
that all molds in a given set wear at about the same rate. Otherwise, downtime for partial mold replacement will
minimize the advantages of mechanization.
Mechanization Shortens Time Cycle
An additional advantage of mechanization is faster production per mold. Careful mold-drying for automatic casting
has allowed fabrication of three times as many pieces per mold per day. Automatic jigger cycles have been cut to a
matter of minutes. These improvements make it possible to reduce mold inventory, conserve space, allow more
time for mold-drying and generally improve integration production efficiency between mold shop and clay shop.
Obtaining Best Results
The three important factors to be considered in mechanization of clayware fabrication are:
with Plaster Molds
1. machine design and operation,
2. model, block, and case mold tooling, and
3. control of mold shop variables.
Machine Design
The natural properties of plaster molds must be recognized. Some of these fundamental characteristics are:
and Operation
1. Plaster molds calcine destructively when the time-temperature-humidity factors are not balanced properly.
2. Plaster molds have a thermal expansion coefficient of approximately 0.0000083 in./in./°F, and will crack when
suddenly cooled from temperatures over about 100 °F. Plasters containing thermal shock ingredients better with-
stand temperature changes.
3. The compressive strength of a dry, well-made conventional plaster mold is approximately 2,000 psi.
4. The tensile strength of a dry, well-made conventional plaster mold is approximately 290 psi.
4