USG Plasters and Gypsum Cements for the Ceramic Industry User Manual
Page 5
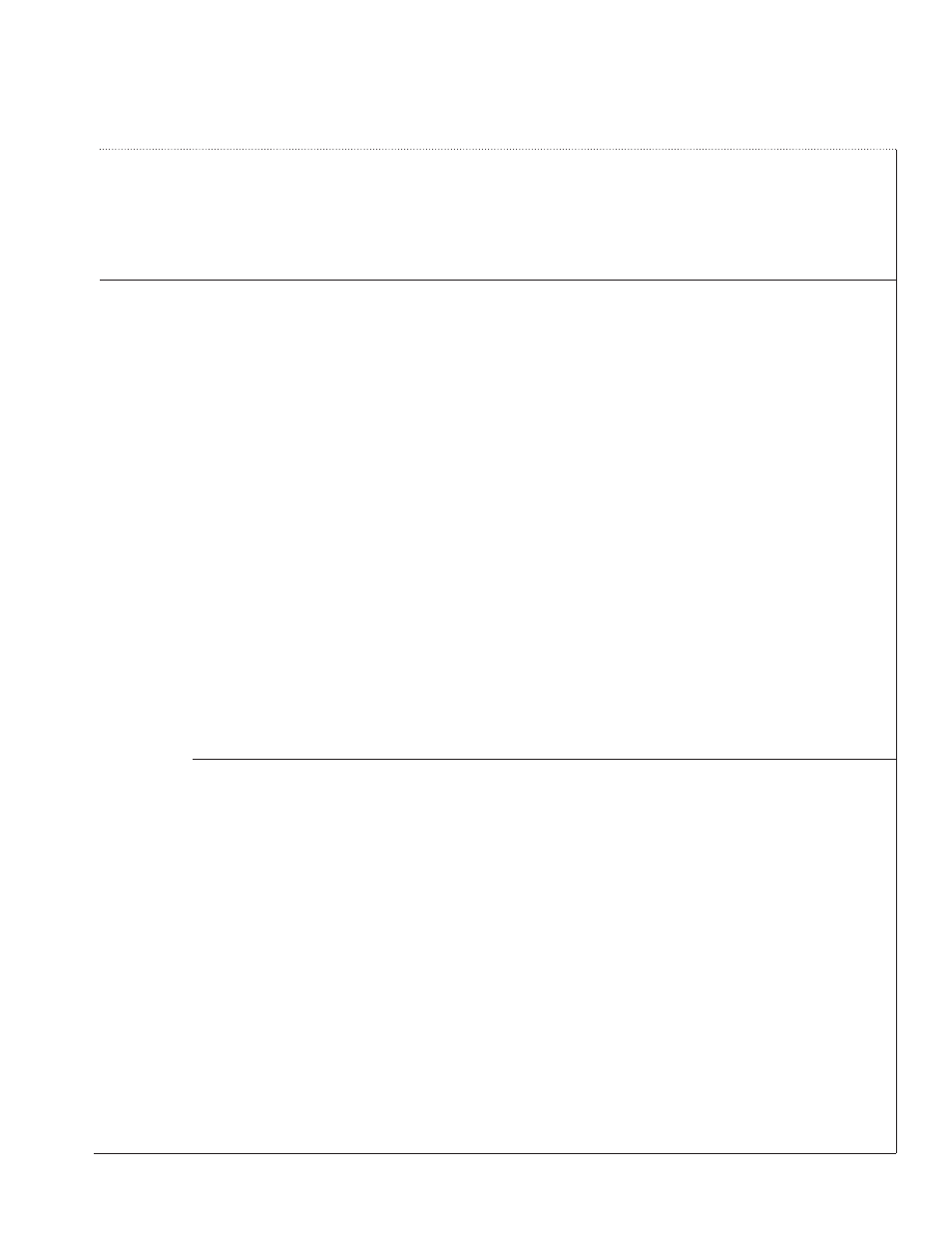
5. The resistance of plaster molds to shearing stresses is very low, approximately 450 psi.
6. The compressive strength and abrasion resistance of a wet mold are approximately half that of a dry mold.
7. Gypsum has a moderate degree of solubility—0.2% in distilled water at room temperature—somewhat more in
warmer water and in water containing sodium sulfate.
When these important points are overlooked, results have been as follows:
– Too rigorous drying with consequent calcination and thermal shock. (See U.S. Gypsum Bulletin IG-502 for drying
information.)
– Punched centers or cracks from excessive forming pressure exerted over inadequately supported molds.
– Excessive localized wear resulting from repetitious stress such as undue solution and abrasion of gypsum caused
by injecting slip in exactly the same spot cycle after cycle.
– Excessive wear on mold bottoms from long travel on abrasive belt conveyors.
In general, it is good practice to confine stresses in molds to those of a compressive nature, and to make sure the
mold is well supported while forming the ware.
Mechanization affords an unparalleled opportunity to dry molds properly to prevent excessive loss from “sweatout”
(too wet), calcination (too dry), and thermal shock (cooled too fast). (See U.S. Gypsum Bulletin IG-502 for drying
information.)
Special pottery plasters designed for maximum resistance to calcination and thermal shock are available and
should be used where these problems exist.
In general, molds ruined on automatic forming equipment is often the result of carelessness. For example, cold air
from open windows may blow directly on hot molds and crack them. Or, clearance between jigger tools and mold
faces may be poorly set, so molds are gouged or scraped. Also, clay may collect under the ring or between molds
to prevent good fit and result in breakage.
Model, Block and
For best results in mechanized forming, design the original model to cope with stresses likely to be encountered.
Case Mold Tooling
In general, it is good practice to:
– Provide for snug fit between model and ring or jig that will carry the working mold, to improve ware quality and
minimize grinding and chipping of molds.
– Avoid thin mold edges that will be susceptible to calcination.
– Avoid significant variations in cross-sectional mold thickness to minimize differential thermal stresses during
heating and cooling.
– Provide integral metal reinforcement where needed.
– Allow adequate volume of plaster; 1-1⁄2-in.minimum wall thickness for casting molds usually is appropriate.
High-speed mechanized forming requires more accurate molds than manual forming. For example, dimensional
tolerance on the jigger mold for a plate is frequently specified as ± 0.008 in. The average model-maker with a
“twirler” can turn only to ± 0.03 in. Mechanization requires suitable model-forming and measuring equipment.
Ordinarily, pottery plaster will expand approximately 0.17% in all directions upon setting, if free movement is
permitted. If expansion is restricted in one direction, it will take place to a greater degree in another. The amount
and direction of setting expansion should be determined by experience for the piece being made, and anticipated
in the blocking and casing process.
5