Marshalltown SP684 SURFACE SHARK Surface Planer User Manual
Page 33
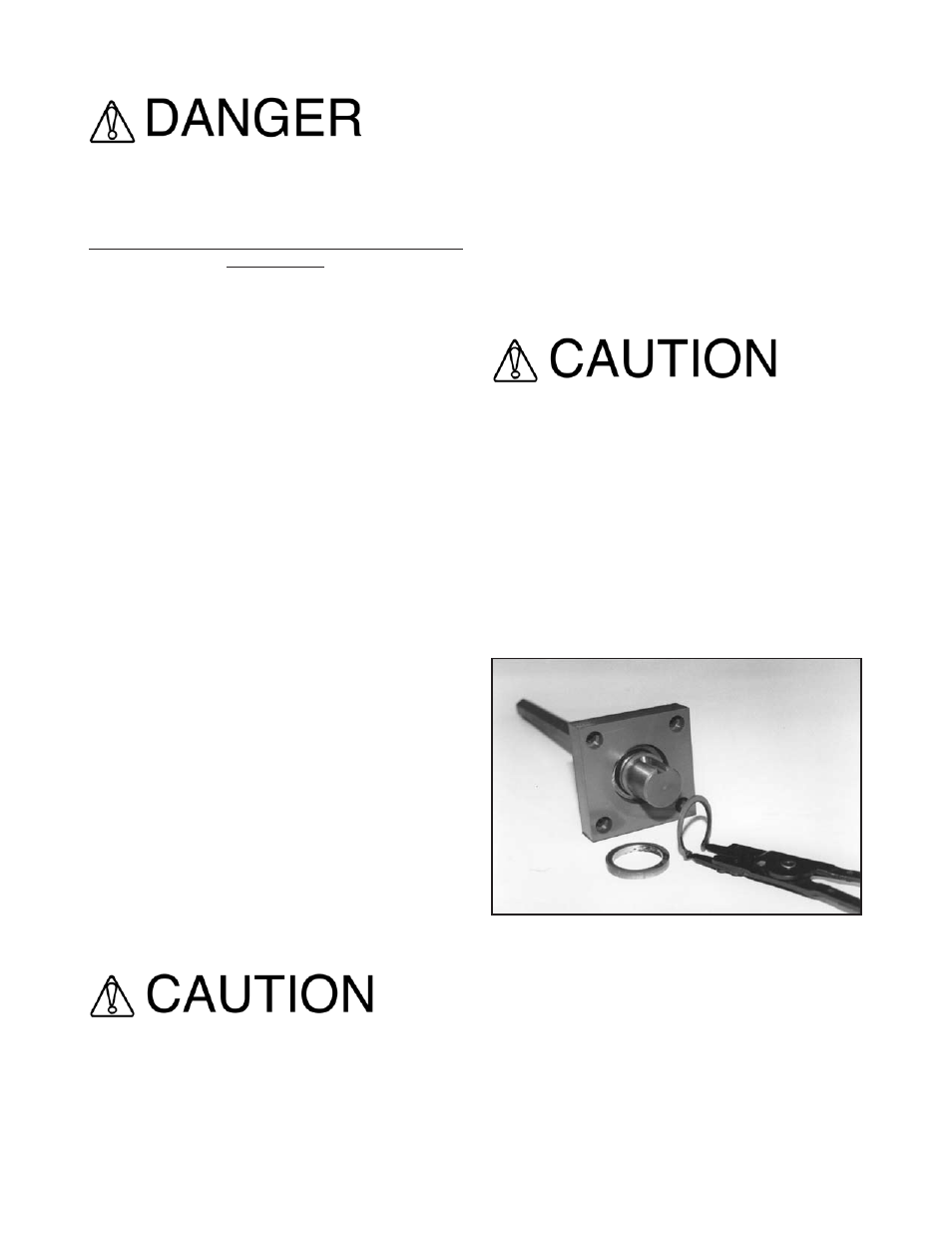
SP684 SuRFACE ShARK SuRFACE PLANER
PAGE 33
UNEXPECTED MACHINE START UP CAN RESULT
IN PROPERTY DAMAGE AND/OR PERSONAL
INJURY.
INSTALLING A REPLACEMENT BEARING ON THE
V-BELT SIDE
Application: SP684 SURFACE SHARK
Tools Required:
1 each, 7/16 inch wrench
1 each, 9/16 inch wrench
1 each, racket, suitable extension and 9/16 inch
socket
1 each, torque wrench, 35 ft lbs (47 Nm.) capacity
with 9/16 inch socket
1 each, 5/16 inch Allen wrench
1 each, pliers for large, external-type, snap rings
1 each, 1-7/8 inch diameter steel shaft of appropriate
length
1 each, 2-1/16 inch outside diameter x 1-5/8 inch
inside diameter x 2-1/4 inch long sleeve
1 each, shop press
various support blocking as required.
Parts Required:
1 each, Part# M5208-2RS sealed ball bearing
1 each, container of bearing and shaft locking grade,
anaerobic adhesive/sealant
1 each, Part# M5160-156 snap ring (if required)
1 each, Part# MSP8-0241 driveshaft (if required)
1) Disconnect the spark plug wire from the spark plug.
2) Position the Surface Planer on a suitable work
surface with the v-belt approximately at waist level.
3) using the racket, extension and 9/16 inch socket,
remove the belt guard from the main frame. Clean the
inside of the belt guard with an appropriate solvent.
Check for signs of wear and damage.
Observe all applicable safety precautions for the
solvent.
4) Remove the v-belt and driveshaft pulley. Refer
to INSTALLING A REPLACEMENT V-BELT OR
PULLEY for specific information.
5) using the 5/16 inch Allen wrench and 9/16 inch
wrench, remove the bearing block/driveshaft assembly
from the main frame. For accuracy and alignment
purposes, the main frame incorporates tapped holes to
properly position the cap screws.
6) Position the driveshaft assembly on a suitable work
surface. use the snap ring pliers to remove the snap
ring. FIGuRE 35. Remove the spacer.
Wear safety glasses and other appropriate safety
apparel when removing the snap ring or performing
any work with an arbor press. Caution all onlookers
about the possibility of flying debris and personal
injury.
7) Position the driveshaft assembly in a suitable
arbor press. Determine that the outer race of the
bearing is properly supported. Press the bearing/
driveshaft assembly from the bearing block. FIGuRE
36. Reposition the support blocking and press the
bearing from the bearing block utilizing the 1-7/8 inch
diameter steel rod as a punch. FIGuRE 37.
FIGuRE 35
8) Clean and inspect the driveshaft and housing for
wear and damage. If any damage is evident, replace
the applicable component.
9) Clean the outside bore diameter of the replacement
bearing. Apply a suitable amount of anaerobic