Marshalltown SP684 SURFACE SHARK Surface Planer User Manual
Page 15
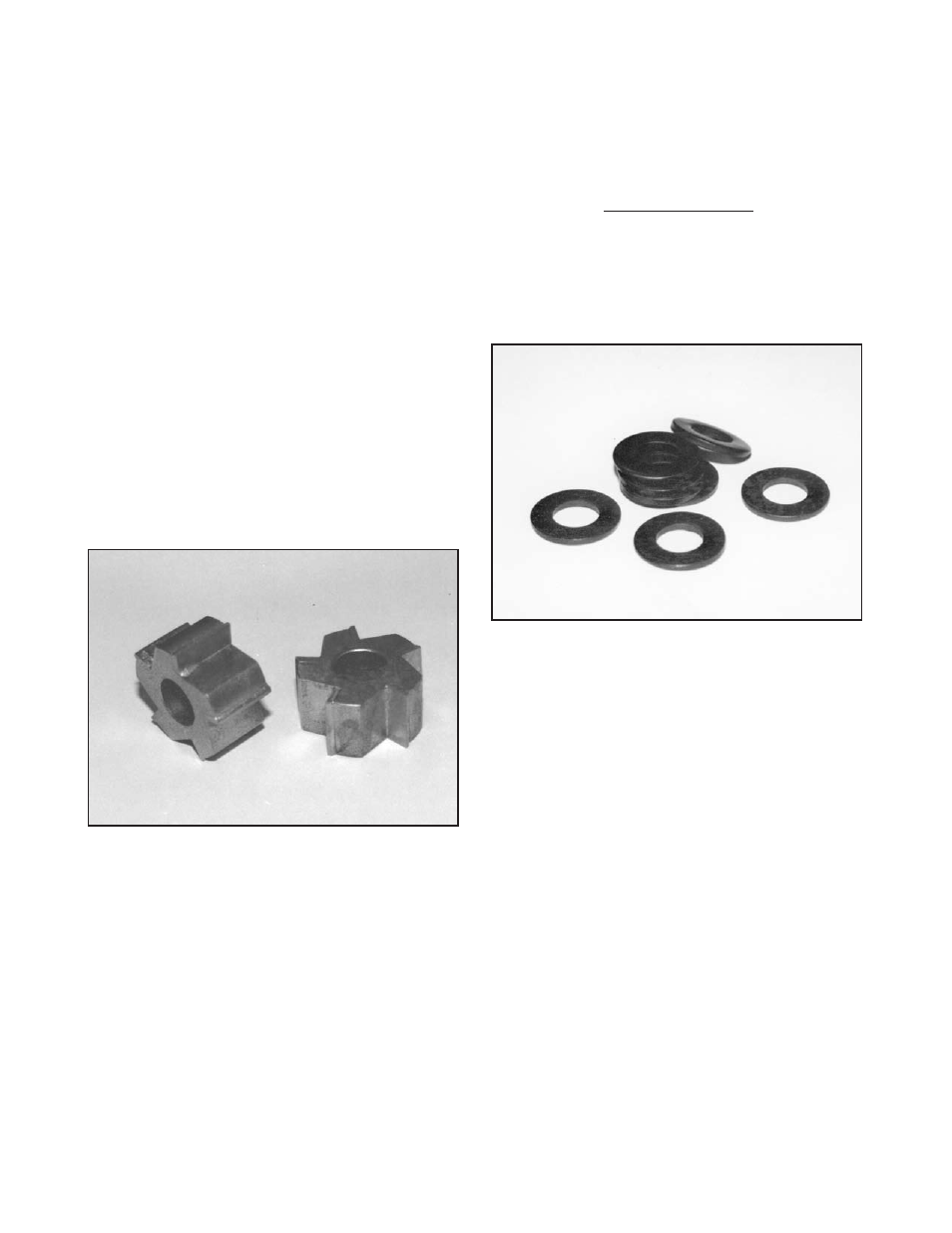
SP684 SuRFACE ShARK SuRFACE PLANER
PAGE 15
The pentagonal flail should be replaced when two
successive tungsten carbide inserts break off or the
inside diameter elongates to approximately 3/4 inch.
In service, the flail body will wear much faster than
the tungsten carbide inserts. The copper brazing
used to weld the inserts into the body can fail and an
insert break off. The flail can still be used in service.
It will just wear a little faster and more uneven in that
particular area. As a general rule, a pentagonal flail
can be utilized until there has been body wear that will
no longer support the tungsten carbide inserts.
Milling Flail
The milling flail is manufactured from high carbon,
alloy steel that is heat treated for additional service
life. FIGuRE 4. Each section of the five sided design
features a rectangular, tungsten carbide insert that is
held in position with copper brazing. The milling flail
is primarily designed for “climb” milling applications.
This requires that the Surface Planer be pulled toward
the operator when being utilized. Removal rates are
dependent upon both surface and substrate material
composition.
FIGuRE 4
Suggested applications:
Removing synthetic coatings, thermoplastic and cold
plastic marking and lines from concrete and asphaltic
surfaces.
COST 10
PRODUCTIVITY 7
SERVICE LIFE 7
Milling flails are designed to remove a variety of
traffic line materials from concrete and asphaltic type
surfaces. With proper techniques, minimal amounts
of parent work surface material will also be removed
during the planing process. Milling flails are expensive.
To realize maximum service life, milling flails should
not be utilized for the direct removal of concrete
and asphaltic work surface materials. Such use will
drastically reduce their service life and substantially
increase project costs.
SPACER WASHERS
Application: SP684 SURFACE SHARK
Spacer washers are stamped from high carbon, alloy
steel that is heat treated for additional service life.
FIGuRE 5.
FIGuRE 5
The function of spacer washers:
1) Reduce the number of flails required to be mounted on
the flail drum, thus reducing purchase and operational
costs.
2) Arrange the flails in a sequence or pattern that
minimizes “blind” or “open” spots created by the
additional support plates of the two section flail drum.
Always insert at least one spacer washer between
two (2) consecutive flails. The exception to this rule
is a configuration where its design does not require
the use of spacer washers. A flail drum set up with
only pentagonal flails and no spacer washers will
not penetrate the work surface at satisfactory rates.
Typical configurations minimize the hammering or
impact action of the flails. however, this can also be
useful when removing traffic lines.
3) Allow the flails to be arranged on the one section
flail drum in configurations of specific widths for many
job applications. An example would be the use of
pentagonal flails to groove a concrete floor. The spacer
washers are used to position the pentagonal flails at
the desired width. FIGuRE 6.