Troubleshooting and fault elimination 8 – Lenze MDSLS Servo spindle motor User Manual
Page 33
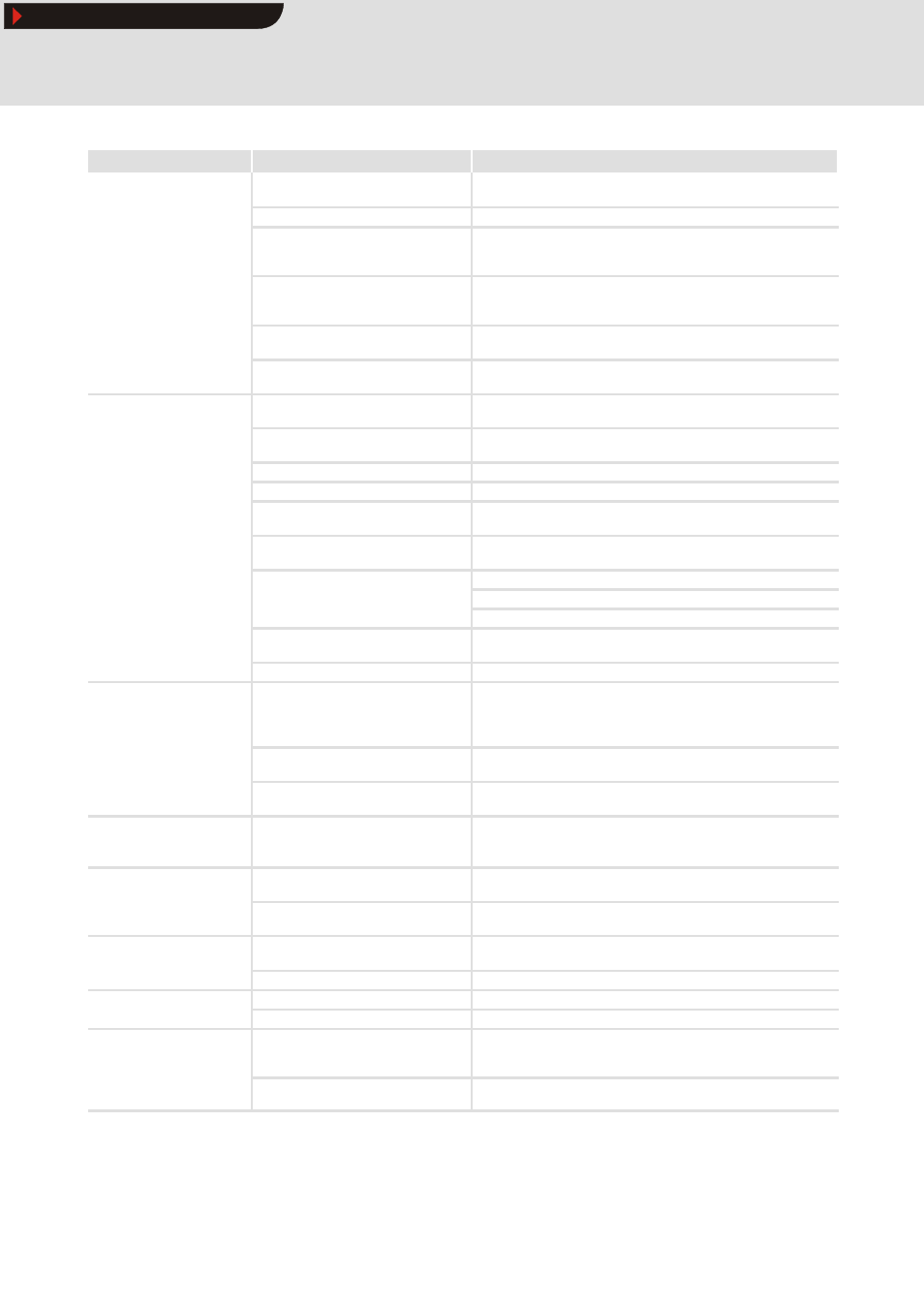
Troubleshooting and fault elimination
8
33
BA 33.0003 EN 1.0
Fault
Cause
Remedy
Motor becomes too warm
Can only be determined
Cooling-air volume is too low,
cooling-air passages are blocked
Ensure that cooling-air inlet and outlet are unrestricted
Can only be determined
through measurements;
permissible surface
Cooling air is prewarmed
Ensure that fresh air is present
permissible surface
temperatures:
z
non-ventilated motors
up to 140 °C
Overload, with normal mains voltage
the current is too high and the speed
too low
Install a larger drive (determination through power
measurement)
up to 140 C
z
forced- or self-ventilated
motors up to 110 °C
Exceeded rated operating mode (S1
to S8 DIN 57530)
Adjust rated operating mode to the specified operating
conditions. Determination of correct drive by expert or Lenze
customer service
Loose contact in supply cable
(temporary single-phase operation!)
Correct loose contact
Fuse is blown (single-phase
operation!)
Replace fuse
Motor does not start
Voltage supply interrupted
z
Check error message at drive controller
z
Check electrical connection (E Ch. 5)
Controller inhibited
z
Check display at drive controller
z
Check controller enable
Fuse is blown
Replace fuse
Motor protection responded
Check motor protection for correct setting and adjust it
Motor contactor does not engage,
fault in the control
Check control of motor contactor and remove fault
Resolver cable is interrupted
z
Check error message at drive controller
z
Check resolver cable
Brake does not release
Check electrical connection
Check air gap (see Brake operating instructions)
Check continuity of magnetic coil
Drive is blocked
Check components for easy movement, remove foreign bodies
if necessary
Motor cable polarity is reversed
Check electrical connection
Motor stops suddenly and
does not restart
z
Motor cable polarity is reversed
or
z
Polarity of resolver cable is
reversed
z
Align the phases at the connection of the motor cable
and
z
Perform the correct connection of the encoder
Overtemperature protector switch
responds
z
Let the motor cool off
– Reduce loading through longer acceleration times
Overload monitoring of the inverter
responds
z
Check settings at the drive controller
z
Reduce loading from longer acceleration times
Wrong direction of rotation
of the motor, correct
display at controller
Reversed motor cable and resolver
cable
z
Swapping two phases of the motor cable
and
z
+COS/-COS connections of the resolver connection
Uneven running
Insufficient shielding of motor or
resolver cable
Check shielding and earthing (E Ch. 5.1.1)
Drive controller gain too large
Adjust the gains of the controllers (see Drive controller
operating instructions)
Vibrations
Insufficient alignment of the drive
train
Realign the machine set, check foundation if necessary
Loose fixing screws
Check and secure screwed connections
Running noises
Foreign bodies inside the motor
Repair by manufacturer, if necessary
g
Bearing damage, spindle damage
Repair by manufacturer, if necessary
Surface
temperature > 140 °C
Overload of drive
z
Check overload and reduce through longer acceleration
times, if necessary
z
Check winding temperature (E Ch. 9.2.2)
Heat removal restricted due to
deposit build-up
Clean surface and cooling ribs of the drives
Show/Hide Bookmarks