6 commissioning, Commissioning, Commissioning 6 – Lenze MDSLS Servo spindle motor User Manual
Page 26: 6commissioning
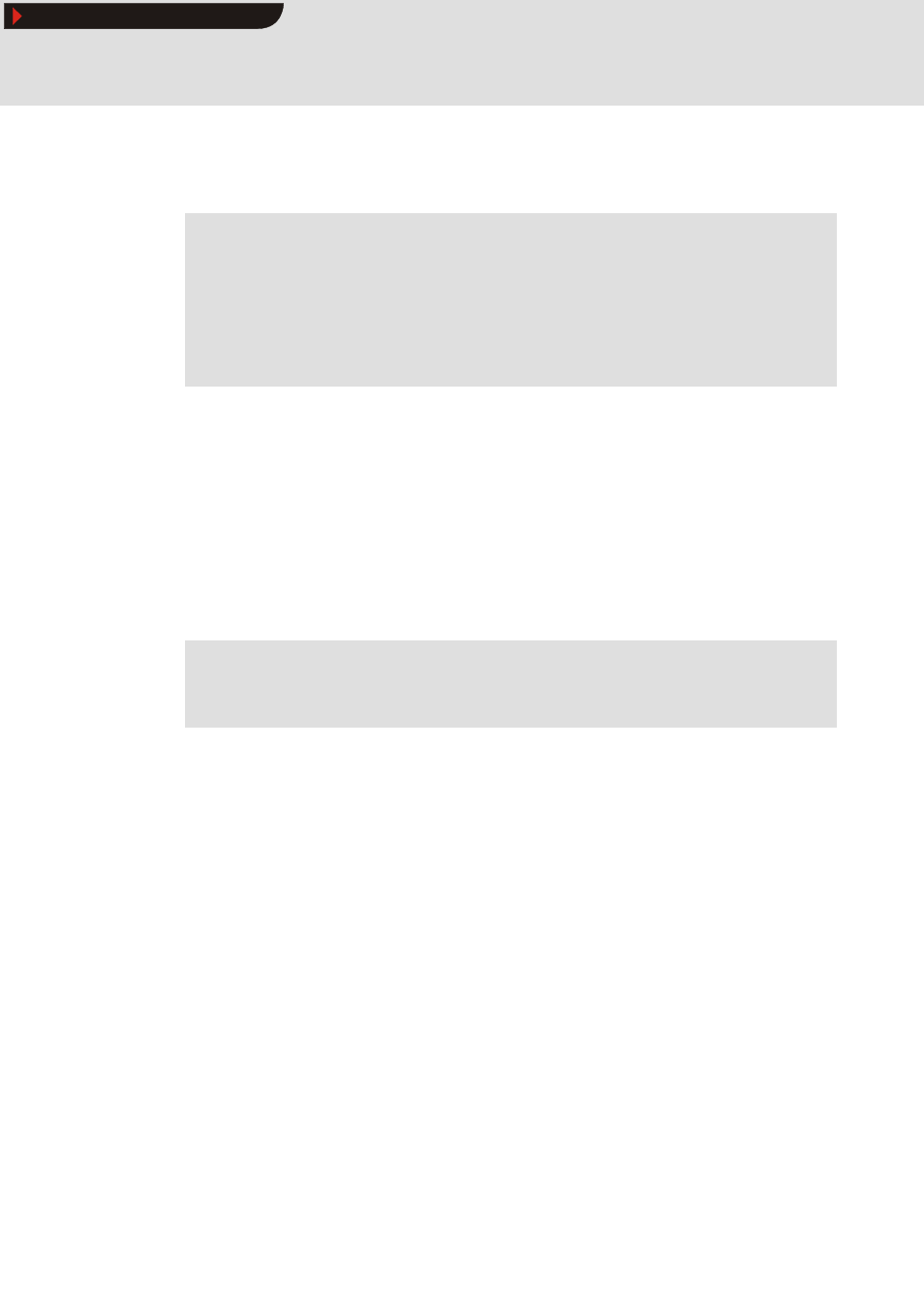
Commissioning
6
26
BA 33.0003 EN 1.0
6
Commissioning
Stop!
The integrated thermal sensor does not prevent overload under all conditions!
At commissioning, reduce the maximum current, e.g. to the rated current of
the motor!
Perform function block interconnection (servo inverter 9300) or I
2
xt
monitoring (servo inverter ECS) with disconnection after several seconds of
operation with I>I
N
, particularly in case of danger of blocking.
ƒ Commission the drive system according to the operating instructions of the drive
controller.
– Entering motor data, parameter setting via Global Drive Control
– Parameter setting of motor temperature detection (is carried out automatically
with parameter setting via GDC)
– Specifying feedback system for speed and position control
– Selecting the operating mode (control structure)
– Entering machine data
– Optimising the drive behaviour, if necessary (optimisation of current, speed, field
and field-weakening control; observe the notes below!).
Stop!
The parameter data that are set via GDC are used as default setting and must
be optimised specific to each application!
Servo controller 9300
The input variable of the current controller is normalised to the maximum device current
I
max. device
. This allows the maximum device current to directly influence the current
controller gain Vp. If a smaller or larger device is used after the current controller
adjustment, the current controller must be adjusted again or the Vp must be matched.
The input and output variables of the speed controller are normalised to the maximum
currentI
max.
(C0022) and themaximum speed n
max.
(C0011).This allows C0022 and C0011
to directly influence the gain of the speed controller Vpn.
ƒ The following applies to the servo controller 9300:
– Vp proportional I
max. device
– Vpn proportional n
max.
(C0011)
– Vpn proportional 1/I
max.
(C0022)
Show/Hide Bookmarks